Plasticizing capacity is a critical parameter to consider when selecting an injection molding machine. As a professional plastic injection molding manufacturer, I want to provide a detailed yet easy-to-understand overview of what plasticizing capacity is, how it impacts the injection molding process, and key factors to consider regarding plasticizing capacity.
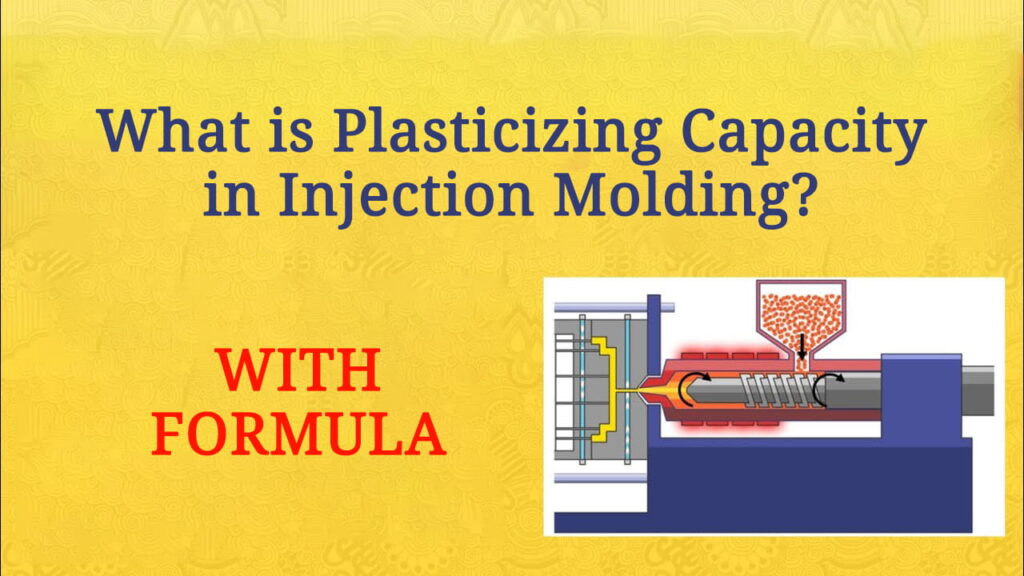
What is Plasticizing Capacity in Injection Molding?
Plasticizing capacity refers to the volume of molten plastic material that an injection molding machine can prepare within a unit of time. It determines the volume of molded parts that can be produced. An insufficient plasticizing capacity relative to shot size can result in a number of issues such as long residence times, material degradation, poor process control, and part defects.
As mentioned above, the plasticizing capacity indicates the volume of molten resin that can be produced per unit time, typically measured in pounds per hour or kilograms per hour. To calculate it accurately, you need to know the parameters of the injection molding machine’s plasticizing screw. We’ll explore the formula for plasticizing capacity shortly.
First, let’s quickly walk through what plasticizing entails in the injection molding process.
How Plasticizing Works in Injection Molding
Injection molding machines accept plastic in pellet form. To mold the pellets into parts, they must first be melted, homogenized, and pressurized. This preparation process is called plasticizing and it occurs in the machine’s plasticizing unit.
The plasticizing unit consists of a heated barrel and a rotating screw inside it. As the screw rotates, it conveys resin pellets forward into areas of the barrel with increasing temperature. The pellets melt into a homogeneous fluid mass and accumulate ahead of the screw. The molten plastic is then injected under pressure into the mold where it cools and solidifies into the finished part.
The rate at which the plasticizing screw can melt, homogenize, and convey the resin governs the machine’s plasticizing capacity. The capacity needs to be matched to the shot size and molding cycle time requirements of the parts being produced. An insufficient plasticizing capacity will starve the molding process.
Key Factors Affecting Plasticizing Capacity
The main factors that influence an injection molding machine’s plasticizing capacity are:
- Screw Diameter – Larger screw diameters allow for higher throughputs of resin.
- Screw Geometry – The channel depth in relation to diameter impacts melting rate.
- Screw RPM – Faster screw speeds convey more resin per unit time.
- Barrel Temperature Profile – Hotter temperatures increase resin fluidity.
- Resin Type – Thermoplastic materials have differing rates of melting.
Next, let’s look at how to quantify plasticizing capacity and ensure optimal matching to part shot size.
How to Calculate Plasticizing Capacity
The plasticizing capacity formula considers the above screw parameters along with material density:
Plasticizing Capacity (g/sec) = 2.5 x (Screw Diameter (mm) / 2.54)2 x (Channel Depth (cm) / 2.54) x Screw RPM x Material Density (g/cm3) x 1000 / 3600 / 2
While this gives the theoretical capacity, it’s recommended to operate between 50-80% of the calculated rate for optimal quality and consistency.
As an example, let’s assume:
- 40mm diameter screw
- Channel depth of 1.2cm
- Max screw speed of 200 RPM
- Polypropylene density of 0.8g/cm3
Plugging this into our formula:
Plasticizing Capacity = 2.5 x (40mm / 2.54) 2 x (1.2cm / 2.54) x 200 RPM x 0.8 (g/cm3) x 1000 / 3600 / 2 = 10.2 kg/hr
So for this setup, a shot size between 5.1 and 8.2 kg/hr would be recommended to leverage 50-80% of maximum plasticizing capacity for optimal quality and repeatability.
The Importance of Balancing Shot Size and Plasticizing Capacity
To reiterate, the plasticizing capacity determines the maximum volumetric flowrate of molten resin into the injection molding machine’s barrel.
If the capacity is substantially less than the required shot size volume, you will likely experience a variety of processing issues and defects:
- Long resin residence times leading to material degradation
- Poor temperature control and inadequate melting
- Sink marks, voids, and other part defects
- Overall process instability and repeatability problems
On the flip side, specifying a machine with way more plasticizing capacity than needed is also problematic:
- Wasted capital expenditure for unnecessary capability
- Potential material degradation from excessive barrel residence time
- Excessive machine footprint and operating costs
The bottom line: properly balancing shot size requirements and plasticizing capacity is crucial for part quality, process stability, and economics.
While the plasticizing capacity formula provides theoretical guidance, resin suppliers can also provide more specific recommendations tailored to individual materials. Finding the optimal balance comes down to thoroughly analyzing part design considerations, production throughput targets, operating budgets and conducting process capability testing.
Key Takeaways on Plasticizing Capacity
To wrap things up, here are the key things to know about plasticizing capacity in injection molding:
- It indicates the volume of molten plastic resin that can be produced per unit time
- The capacity is governed by screw and barrel parameters along with resin type
- A mismatch between capacity and shot size causes major processing problems
- Optimal quality and economics are achieved by leveraging 50-80% of maximum plasticizing capacity
While sizing a machine’s plasticizing capacity can get complex quickly, the above overview covers the basics of this critical injection molding process parameter. Reach out in the comments below if you have any other questions!