Splay is a common cosmetic defect in plastic injection molding where silver or white streaks appear on the surface of a part. Identifying what causes splay is key to correcting this issue and improving quality control. As a professional plastic injection molding manufacturer, after analyzing thousands of injection molded parts, I’ve discovered the main culprits behind splay defects.
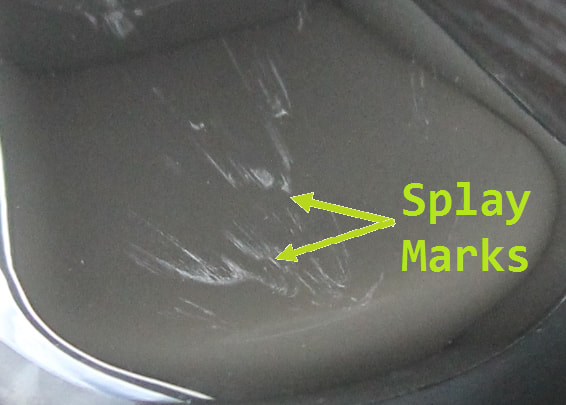
What causes splay in plastic injection molding?
Splay is a common cosmetic defect in plastic injection molding, characterized by off-colored streaks, often silver in hue, on the surface of molded parts. The primary causes of splay are moisture, shear, plastic degradation, and overheating.
Moisture
Moisture is by far the most common cause of splay in injection molded plastic parts. What causes splay in plastic injection molding often comes down to improper drying of the plastic resin.
When plastic resin absorbs ambient humidity or water, that moisture vaporizes into steam when the pellets are heated inside the injection barrel. As the mold fills, the steam bubbles migrate to the surface causing streaky splay marks.
I’ve seen splay caused by moisture cover an entire part randomly. It rarely appears in the same exact location from part to part. That’s a key indicator that moisture is the culprit.
Hygroscopic resins like nylon and polycarbonate readily absorb moisture and require proper drying before molding. But even non-hygroscopic resins can contribute to splay without sufficient drying.
Follow your material supplier’s recommendations for drying temperature and duration. Consider installing a moisture analyzer to validate that the plastic pellets remain below a maximum moisture content through the drying process.
Shear
While moisture is the most prevalent source of splay, shear forces can also drag bubble and degrade plastic to cause splay during filling.
There are two main ways shear induces splay streaks:
Screw shear
If the screw speed, back pressure, or melt temperature are set too high it can overshear the plastic melt leading to gassing and degradation. Both create a foamy melt that shows splay on the part surface.
Lower the screw rpm, reduce back pressure, and decrease melt temperature to limit shear. Give any changes 20 minutes to take effect before assessing their impact.
Gate shear
An improperly sized gate for the part geometry can also impose excessive shear as the polymer enters the mold cavity. The result is likely splay marks right in front of the gate area.
Carefully examine the location of splay relative to the gate. Adjust the gate dimensions or add additional gates to minimize shear exposure. Slowing fill velocity can further reduce gate shear effects.
Plastic degradation
While moisture and shear are the primary causes, degraded plastic can also offgas and lead to splay.
Think of plastic resin like a ball of yarn – long molecular chain polymers all tangled up. Excess residence time in the barrel paired with overly high temperatures slowly snips and clips those molecular chains through thermal degradation. The resulting small gaseous molecules then appear as splay.
Carefully monitor factors like barrel set points, residence time, and melt temperature to prevent degradation issues. Adding screw delay recovery can help ensure the screw finishes mixing right before injection to minimize polymer breakdown.
Overheating
Finally, splay can simply result from overheating during plastic injection molding. Barrel temperatures that exceed recommendations produce a hot, gas-filled melt that transfers into streaky splay patterns.
Overdrying plastic is a common and hidden contributor here. While you want resin dry, overdrying literally cooks out the molecular structure of polymers. Close control of both drying protocol and barrel temperatures are key.
Confirm what causes splay in your injection molding
Isolating moisture, shear, degradation, and overheating helps narrow down what causes splay in plastic injection molding. But every molding workcell has nuances requiring good old-fashioned molding know-how.
Get granular by analyzing factors like:
- Actual barrel, nozzle, mold hot runner temperatures
- Fill time, velocity, pressure
- Screw rpm, back pressure
- Gate, runner dimensions
- Dryer time, temp
- Moisture content
How to get rid of splay in injection molding
Now that you know what’s behind those pesky silver streaks, let’s get into the business of actually eliminating splay defects from your injection molded components.
Step 1: Inspect parts for defect patterns
As a first step, carefully check your molded pieces for patterns in the splay defects.
- If marks occur randomly all over, moisture is likely the culprit.
- Defects mainly at the gates point to shearing.
- Consistent marks indicate a mold-based issue like lubricant bleeding out of lifters.
So pay close attention to exactly how and where the splay manifests before jumping into fixes. The defect pattern will guide appropriate solutions.
Step 2: Address moisture-related causes
Since moisture is the most common root cause of splay, let’s go through a systematic process to tackle it:
A. Check hygroscopic materials
Scan your material types and data sheets to see if any resins are hygroscopic like nylon or PC. Even small amounts of moisture in these materials can cause major splay.
B. Verify drying temperature & time
Check drying temperature and duration against resin supplier recommendations. For example, nylons need 8 hours at 180°F. Make no assumptions here.
C. Inspect dryers
Physically check that supply air lines are hot and returns are warm. Use probes to confirm temperatures match setpoints. Faulty dryers mean wet plastic!
D. Adjust throughputs
If using undersized dryers, materials may not spend sufficient time inside to fully dry out. Increase drying time by reducing throughput rates.
E. Drain loaders
Moisture can re-absorb into cooled plastic sitting in loaders. Always drain out initial portions before molding from any given dryer load.
Follow this methodology to systematically rule out or address moisture-related causes. This tackles the majority of splay issues.
Step 3: Tackle heat-related splay
If moisture is definitively not the culprit, excessive heat is the next likely suspect. Here’s how to resolve thermal splay defects:
A. Compare melt temps
Check recorded melt temperatures against material supplier guidelines. If too high, incrementally drop barrel temp and retest parts.
B. Reduce back pressures
Excessive back pressure risks overheating and degrading resins. Gradually decrease back pressure until eliminating splay.
C. Lower feed zone temps
Cooler feed zones reduce the time resin sits in the hot barrel, minimizing degradation from prolonged heat exposure.
D. Delay screw recovery
If cooling times are long, delay screw rotation to finish recovery just before mold open. This prevents overheating from residency.
Methodically addressing heat-related factors will resolve many remaining splay issues.
Step 4: Address shear-related causes
If heating and moisture are conclusively not factors, then shear heat is likely contributing to those silver streak woes. Here are tips for countering shear:
A. Lower screw RPM
High screw speeds generate excess shear heat, degrading plastic. Gradually decrease RPMs until splay disappears.
B. Widen gates
Undersized gates cause shearing of material. Widen gates or use fan gates to minimize shear heating.
C. Slow injection
The fastest way to resolve gate shear is to slow injection speeds. This gives resin more time to flow through.
D. Eliminate obstructions
Check nozzle tips and mold venting channels for signs of debris or burrs that could disrupt smooth melts flow.
As a last resort, addressing shear causes should tackle residual splay defects not resolved by other fixes.
Step 5: Address contamination factors
If splay still persists after addressing heat, moisture and shear, contamination may be the sneaky culprit. Here’s how to tackle contaminated plastic and molds:
A. Eliminate regrind
If regrind or recycled plastic is used, purge it all out and exclude for testing purposes. Contaminants in reused resin frequently cause splay.
B. Increase purging
Purge extensively with specialty compounds to fully clean screw, barrel, nozzle and hot runners of debris or accumulated oils, waxes and contaminants.
C. Clean molds
Tear down molds and meticulously clean out any accumulated lubricants, rust preventatives or other foreign matter on cavity surfaces using suitable solvents.
Thoroughly addressing contamination leaves no stone left unturned in your fight against splay foes.
The bottom line
As they say, “the devil is in the details” with injection molding. By meticulously examining process data and parts you gain priceless insight into correcting defects like splay.
What causes splay likely comes down to moisture absorption or excess shear forces degrading the melt. But improper setup anywhere along the way can induce streaky splay marks. Methodically work through potential issues until you isolate the root cause solve it accordingly.