Injection molding is one of the most versatile and cost-effective manufacturing processes used to produce plastic parts at scale. From Legos to iPhone cases, injection-molded plastics are everywhere.
But what types of plastics can you use for injection molding? As a professional plastic injection molding manufacturer, I will share many options for you to choose from.
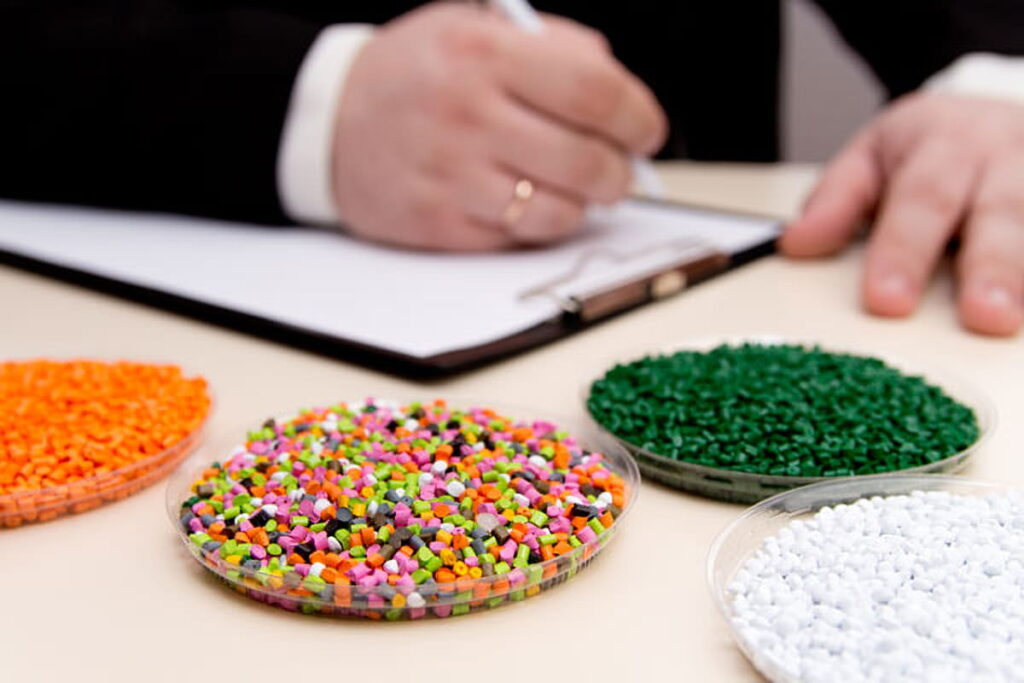
An Overview of Plastics for Injection Molding
The plastics used in injection molding are thermoplastics, which become liquid when heated and return to a solid state when cooled. This property allows them to be injection molded, unlike thermoset plastics which only liquefy once.
Within thermoplastics, there are two main categories:
- Amorphous plastics – These have no sharp melting point and shrink/expand gradually when temperature changes. Examples include acrylonitrile butadiene styrene (ABS), polystyrene (PS), acrylic, and polycarbonate.
- Semi-crystalline plastics – These have a distinct melting point and tend to expand/contract more rapidly with temperature swings. Examples include polypropylene (PP), polyethylene (PE), nylon, and polyoxymethylene (POM).
Now let’s explore some of the most common injection molding plastics in more detail.
What Type of Plastic Is Used in Injection Molding?
Acrylonitrile Butadiene Styrene (ABS)
ABS is an opaque thermoplastic known for its strength, rigidity, and impact resistance. Despite its high durability, ABS plastic is lightweight.
It’s one of the most ubiquitous injection molding materials. ABS can be found in Legos, plastic pipes, car interior parts, and electronics cases to name a few applications.
Key Properties:
- High impact strength and rigidity
- Good dimensional stability
- Resilient – doesn’t easily scratch, dent, or break
- Versatile – takes colorants and textures well
Drawbacks: Doesn’t resist weather or UV light. Emits toxic fumes when burned.
Polypropylene (PP)
Polypropylene is a versatile, food-grade plastic that has high chemical resistance and fatigue strength. Known for its durability, PP plastic retains its shape even with heavy use.
Common injection molded polypropylene applications include food containers, dishwasher safe items, automotive parts, and hinges. Many plastic bottle caps are also made of PP.
Key Properties:
- Naturally glossy
- Excellent chemical resistance
- Flexible but durable – ideal for living hinges
- Recyclable
Drawbacks: Degrades in UV light. Flammable. Glue doesn’t bond well to PP.
Nylon
Nylon injection molding produces durable plastic parts able to withstand high impacts, wear, and heat. With good chemical resistance, nylon plastic is found in mechanical parts like bushings, bearings, and gears.
Automotive applications utilize nylon’s strength, low friction, and weight reduction capabilities. Food packaging sometimes contains nylon as well.
Key Properties:
- High strength-to-weight ratio
- Withstands high impacts
- Low coefficient of friction – doesn’t heat up easily
- Good abrasion resistance
Drawbacks: Absorbs water. Expensive. Difficult to mold.
Polyethylene (PE)
Available in high-density (HDPE) and low-density (LDPE) versions, polyethylene offers unbeatable chemical resistance due to its nonpolar nature. It’s also quite flexible and resilient to cracking or tearing.
Injection molded PE is ubiquitous in products like plastic bottles, containers, pipes, bags, cable insulation, and children’s toys.
Key Properties:
- Excellent chemical resistance
- Elasticity – bends without breaking
- Moisture resistance
- Affordable
Drawbacks: Poor UV resistance. LDPE has low tensile strength.
Polystyrene (PS)
Polystyrene comes in general purpose (GPPS) and high impact (HIPS) versions. GPPS plastic is rigid and transparent while HIPS is opaque and more flexible.
You’ll find injection molded PS in food containers, medical devices, housings for electronics/appliances, and packaging for consumer goods. HIPS comprises toolboxes and electronics cases.
Key Properties:
- Clarity – makes good packaging
- Dimensionally stable
- Can be easily machined and fabricated
- Low cost
Drawbacks: Brittle. Flammable. Poor chemical/UV resistance.
Polycarbonate (PC)
Known for optical clarity and extreme impact resistance, polycarbonate injection molding produces durable transparent parts. Bulletproof glass, lenses, and headlight covers utilize these desirable attributes.
Electronic device housings and enclosures also leverage PC’s dimensional stability across temperature fluctuations. It serves as a lighter, shatter-resistant alternative to glass.
Key Properties:
- Transparent and glossy
- Extremely strong — doesn’t scratch or dent easily
- Heat resistance up to 140°C
- Excellent electrical insulation
Drawbacks: Degraded by UV exposure and harsh chemicals. Expensive.
Polyoxymethylene (POM)
Also called acetal plastic, POM or acetal has high tensile strength, durability, and rigidity properties. As an engineering-grade plastic, it possesses excellent fatigue life and resists creep deformation under load.
Injection molded POM/acetal is suitable for high performance gears, fasteners, bearings, springs, and other mechanical parts. Consumer goods like keyboards, knives, and eyeglass frames also utilize acetal plastic.
Key Properties:
- Excellent strength and stiffness
- Low coefficient of friction – doesn’t “gum up”
- Good chemical/solvent resistance
- Noise dampening capabilities
Drawbacks: UV degradation. Longer molding cycle times.
Luckily, plastic additives can minimize the drawbacks mentioned above for each resin.
Important Properties Based on Application
As summarized in the chart below, key factors in choosing an injection molding plastic include:
Application | Important Properties | Suitable Materials |
---|---|---|
Food packaging | FDA compliant, moisture resistance, chemical inertness | Polyethylene (HDPE/LDPE), Polypropylene |
Outdoor uses | Weatherability, UV light resistance | ABS, Acrylic, Nylon |
Transparent parts | Optical clarity, impact resistance, stiffness | Polycarbonate, Acrylic |
High temperature environments | Heat resistance, dimensional stability | Nylon, Polycarbonate, POM |
Flexible applications | Elasticity, fatigue strength | Thermoplastic elastomers (TPE), LDPE |
Mechanical/moving parts | Strength, wear resistance, low friction | POM, Nylon, ABS |
Electrical components | Electrical insulation, flame retardance | ABS, Polycarbonate |
Toys | Impact strength, safety, colorability | Polyethylene, ABS |
This covers the basics on what type of plastic resins can be used in injection molding. As you choose materials, prioritize properties that allow your plastic parts to function properly and safely while minimizing cost.
In Summary
To recap, injection molding relies on thermoplastic materials that flow upon heating and solidify when cooled. The most common injection molding plastics include:
- ABS – Strong, rigid, versatile
- Polypropylene – Durable, flexible, food-safe
- Nylon – High strength, abrasion/impact resistant
- Polyethylene – Excellent chemical resistance
- Polystyrene – Affordable, easily fabricated
- Polycarbonate – Optical clarity, high impact strength
- Polyoxymethylene/Acetal – Excellent mechanical properties
Always match your target application and working environment to the optimal balance of material properties and cost. Additives help tailor plastics to your specific needs.