Plastic injection molding has revolutionized manufacturing. This pivotal process produces everything from Legos to iPhone cases using specialized machinery. But what exactly is plastic injection molding? And what role does it play in the global economy?
In this complete guide, as a professional plastic injection molding manufacturer, we’ll break down the plastic injection molding process step-by-step. You’ll also discover why major manufacturers rely on injection molding to mass produce plastic goods.
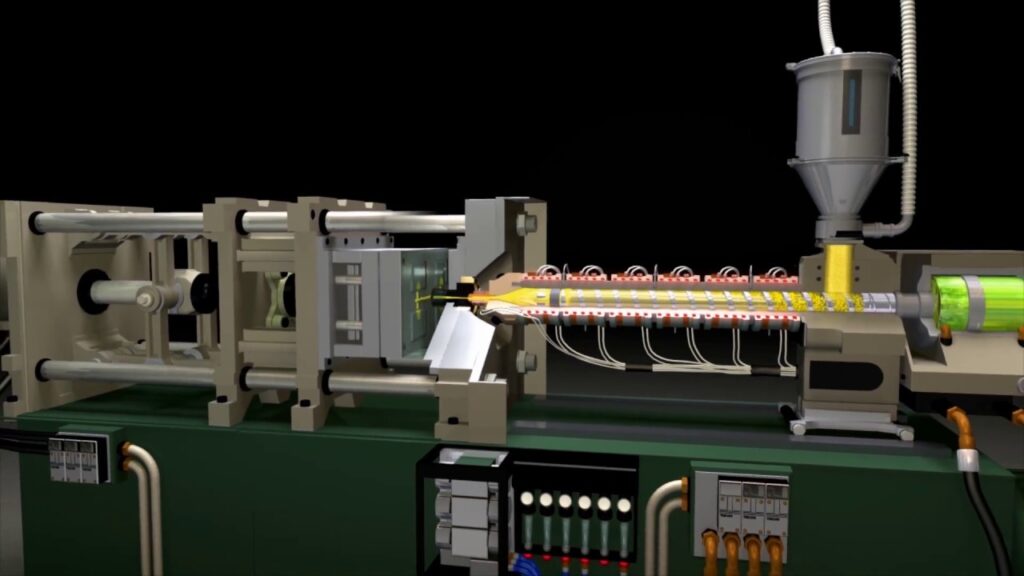
What Is Plastic Injection Molding Process?
Plastic injection molding is a manufacturing process that converts plastic pellets into fully formed parts. Specialized machines melt plastic resin and inject it at high pressure into custom steel molds. After the plastic cools and hardens, the mold opens to reveal newly created products.
This high-volume process makes plastic injection molding ideal for mass production. In fact, manufacturers use it to produce billions of identical plastic components each year. Common injection molded parts include bottle caps, fishing lures, and even medical devices. The automotive industry also utilizes this technique to craft intricate dashboard pieces.
The 4 Steps of Plastic Injection Molding Process
The plastic injection molding process can be broken down into four main steps:
- Clamping
- Injection
- Cooling
- Ejection
This defines the complete molding cycle that repeats to create part after part using a high-volume production technique.
Step 1: Clamping
To start the injection molding sequence, the two halves of the injection mold close, forming the mold cavity. The mold halves are securely clamped together under pressure to keep the mold closed during the injection process.
Tie bars outside the mold connect the stationary half to the movable half to provide rigidity and withstand the pressure during clamping.
Step 2: Injection
With the mold securely closed, the next step is to inject molten plastic into the mold cavity. The injection unit of the injection molding machine contains a hopper, barrel, screw and nozzle.
The plastic pellets are fed from the hopper into the barrel. The screw rotates and moves backwards, allowing pellets to enter and move forward.
Powerful heater bands melt the plastic pellets under high temperatures. As the screw moves forward, it builds sufficient pressure to inject molten plastic through the nozzle and into the mold cavity.
Step 3: Cooling
After the cavity fills, the holding pressure is maintained to allow the gate to solidify and prevent the molten plastic from flowing backwards. This packing happens at an optimal temperature and pressure.
At this stage, cooling channels carry coolant around the mold surface to solidify the molten plastic. The exact cooling time depends on the wall thickness and complexity of the plastic part. Thicker walls need a longer cooling cycle.
Proper temperature control is vital to ensure uniform cooling. This prevents defects from fast cooling and avoids long cycles from slow cooling.
Step 4: Ejection
As the temperature lowers, the solidified part is ready to be removed. The clamping force holding the two halves weakens and the mold opens.
Finally, ejector pins push the finished plastic parts out of the mold cavity, allowing the operator to remove parts from the molding machine. The mold closes again, the production cycle repeats and a new plastic part takes shape.
Tools Required for Plastic Injection Molding Process
Carrying out the injection molding process needs an injection molding machine and a mold. The mold is secured inside the injection molding machine and receives the molten plastic to form parts.
Injection molding machine – It contains a hopper, barrel, heating units, ram, mold, and clamping unit. Available in horizontal and vertical layouts, newer all-electric machines offer superior precision and energy efficiency. Press sizes range from 5 to over 6,000 tons of clamping force.
Mold – Molds have a cavity with the precise geometry of the final part. It may have a single cavity or multiple cavities for high volume production. Channels are machined for mold cooling, ejection system, etc. Complex molds can have slides, cams, rotary tables and other devices to manufacture intricate plastic parts.
Raw Material Used in Injection Molding
There’s a wide range of thermoplastic polymers suitable for injection molding applications. The most common include polyethylene (PE), polyvinyl chloride (PVC), polystyrene (PS), acrylonitrile butadiene styrene (ABS) and polypropylene (PP).
These plastic materials are available in pellet form for injection molding. Manufacturers can use various fillers, reinforcements, lubricants, colorants, flame retardants and other additives to modify material properties.
They select the optimum plastic type depending on mechanical properties, temperature capabilities, chemical resistance, color options, special performance additives and other requirements for the finished components.
Advantages of Plastic Injection Molding
Plastic injection molding offers unique manufacturing efficiencies that make it a highly preferred production method in many industries. Here are some of its benefits:
High Volume Production – Once the injection molding machine is set up, it can produce thousands of identical plastic parts in a single day. Automation allows mass production around the clock. Part costs are low.
Fine Tolerances – Injection molding can hold tighter tolerances than competing processes like CNC machining or casting. Parts have a high degree of precision with little variation among parts.
Material Versatility – Thermoplastic polymers offer tremendous variation in mechanical properties, aesthetics, chemical resistance, performance etc. Parts can be colored, filled or altered for special qualities. Recycled plastics lower costs.
Complex Geometries – Multi-cavity molds using side-action, unscrewing and collapsible core techniques can produce highly complex parts with no secondary machining required.
Assembly Consolidation – Insert molding allows placing pre-assembled components inside a plastic part during production. Multi-shot techniques use sequential shots of different plastics. This simplifies product assembly.
Fast Production – Once mold and machine are set up, injection molding production rates are vastly faster than alternatives like CNC machining or 3D printing. Shots take seconds or minutes. 24/7 automation maximizes production scheduling.
Lower Labor – Automating injection molding systems cuts labor costs substantially. Robots even handle finished parts. One operator can manage multiple machines/molds and oversee part handling systems.
Limitations of Plastic Injection Molding
Despite offering mass production capabilities, plastic injection molding does have certain limitations:
High Mold Costs – Precision steel molds have high initial cost. Aluminum molds have lower cost for short production runs but cannot sustain long cycles. However, higher part volumes distribute mold cost over total parts produced.
Material Waste – Scrap parts may be 5-10% by weight. Sprues, runners and gates end up as waste. Good designs optimize material usage. Granulators grind sprues/runners into regrind for recycling into parts.
Part Weight – Very large plastic parts tend to sag or warp under their own weight when cooling in open-faced molds. Most parts are limited to a couple of pounds but more if made hollow. Two-sided cored construction prevents sagging in large parts.
Secondary Machining – Some mold aspects like sharp external corners need machining after molding for best finish. Other secondary operations like threading holes or assembling inserts happen after molding.
Applications of Plastic Injection Molding
Injection molded plastics revolutionized manufacturing across industries from automotive to medical. Consumers use injection-molded plastic components in everyday household items.
Here are some key applications:
Automotive – Panels, bumpers, lighting components, fluid reservoirs, dashboard instrument housings and heat ventilation parts utilize injection molding extensively. Newer techniques mold hybrid plastic-metal composites and injection overmolded parts.
Electronics – Mobile device housings, computer keyboards, TV remote exteriors and other consumer electronics rely on precision plastic parts from injection molding. The process also molds tiny electrical connectors and precision enclosures.
Medical Industry – Disposable syringes, vials, valves, IV tubes, surgical instruments like forceps, and diagnostic devices molded from plastic engineered for medical devices. Newer lightweight prosthetics also use injection molded plastics.
Packaging Industry – Injection molding produces plastic bottles, containers, caps and closures, cases, trays and bags for consumer goods. Food packaging molds antibacterial plastics. Cosmetics packaging focuses heavily on aesthetic plastic parts.
Toys – From model assembly parts to dolls to board game pieces, injection molding offers the versatility and precision needed for mass-produced toys. Toys can replicate intricate product designs impossible with most other manufacturing techniques.
Household Items – Everyday plastic products use injection molding including storage containers, kitchenware, fans, vacuum components, organizers, home appliances and laundry accessories.
Injection molding leverages engineered thermoplastics to manufacture a majority of plastic components across diverse commercial and consumer applications!
In Conclusion
The plastic injection molding process reshapes select plastic polymers into usable consumer and industrial products using molds. This high volume manufacturing technique relies on scientific molding principles to achieve precision, repeatability and high production rates.
Injection molding transforms granular thermoplastic pellets into molded parts by feeding raw material to plasticate under controlled conditions of heat and pressure before injecting it into precision mold cavities. As parts cool and cure, they can be ejected from molds and the molding cycle repeats automatically.
With versatile thermoplastics, consolidation of assembly into parts, precision molding of tiny and complex components and automation maximizing production; injection molding delivers exceptional manufacturing productivity across nearly every industry.