Liquid resin molding is often a more cost-effective manufacturing process compared to injection molding. But why is liquid resin molding less expensive than injection molding? As a professional plastic injection molding manufacturer, I will share an in-depth look at the key reasons behind the lower costs.
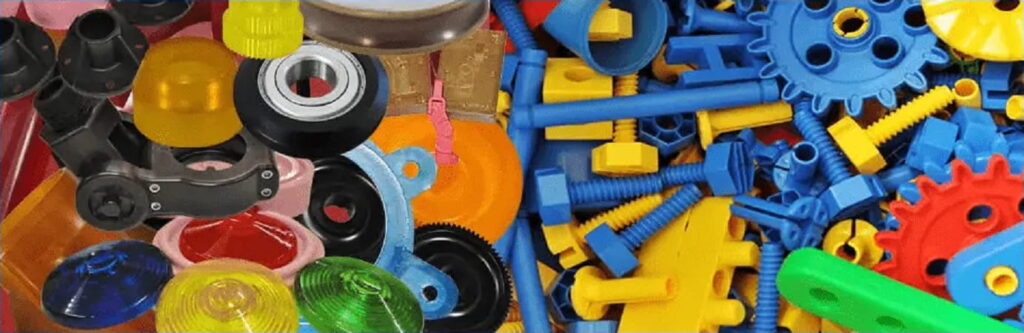
Why Is Liquid Resin Molding Less Expensive Than Injection Molding?
The liquid resin molding leverages cheaper raw materials, simpler tooling and equipment, faster mold fabrication, and an emphasis on smaller-scale runs of 25-100 units. Together these factors enable major cost reductions compared to injection molding.
Here’s an in-depth comparison that highlights why liquid resin molding can be more cost-effective:
Tooling Costs
Injection Molding:
- High Initial Investment: Injection molding requires the creation of high-precision, durable molds made from steel or aluminum. These molds are complex, involving precise machining and sometimes incorporating intricate cooling channels, leading to high upfront costs.
- Maintenance and Lifespan: Injection molds are designed for long production runs, which adds to their complexity and cost. They also require regular maintenance to remain in good working condition.
Liquid Resin Molding:
- Lower Tooling Costs: LRM often uses simpler, less expensive molds, which can be made from materials like silicone, epoxy, or other less costly substances. The mold-making process is less complex and cheaper.
- Shorter Lifespan: LRM molds are typically not as durable as injection molds and are suited for shorter production runs. However, this is often sufficient for prototyping, small batches, or custom parts, making it more economical for these applications.
Equipment Costs
Injection Molding:
- Expensive Machinery: Injection molding machines are costly due to their complexity, high precision, and the ability to handle high pressures and temperatures.
- Support Systems: These machines also require additional support systems, such as cooling systems, heaters, and sometimes robots for part removal, further increasing the investment.
Liquid Resin Molding:
- Simpler Equipment: The equipment for LRM is generally simpler and cheaper. This can include basic mixing and dispensing systems that are less complex and easier to maintain.
- Lower Pressure Requirements: LRM processes typically do not require the high pressures needed in injection molding, allowing the use of less robust and cheaper equipment.
Production Volume and Flexibility
Injection Molding:
- High Volume Production: Injection molding is highly efficient for large-scale production due to its fast cycle times once the mold is ready. However, the high cost of molds and setup makes it less economical for small batches.
- Less Flexible: The process is less adaptable to changes. Any design change usually requires costly and time-consuming modifications to the mold.
Liquid Resin Molding:
- Low to Medium Volume: LRM is more cost-effective for low to medium production volumes, including prototyping and custom parts. The lower setup costs and faster mold production are advantageous for these scales.
- Greater Flexibility: LRM allows for easy modifications to molds and quick changes in production, which is beneficial for iterative design processes and custom manufacturing.
Material Costs and Variety
Injection Molding:
- Material Efficiency: Injection molding can use a wide variety of thermoplastics and thermosetting plastics efficiently. However, material costs can be higher due to the need for specific grades that perform well under high-pressure and high-temperature conditions.
- Wastage: There can be more material wastage in the form of runners and sprues, although these can often be recycled.
Liquid Resin Molding:
- Wide Range of Resins: LRM can use a variety of liquid resins, including polyurethanes, epoxies, and silicones, which may be cheaper or more readily available in certain applications.
- Reduced Wastage: There is typically less wastage compared to injection molding, and the materials used can sometimes be less expensive per unit volume.
Labor and Operational Costs
Injection Molding:
- Skilled Labor: Operating and maintaining injection molding machinery requires skilled labor, adding to operational costs.
- Setup and Downtime: The setup process is time-consuming and costly, and any downtime for maintenance or mold changes can be expensive.
Liquid Resin Molding:
- Less Specialized Labor: LRM processes can be simpler to operate, requiring less specialized labor.
- Quick Setup: The setup time is generally shorter, reducing labor costs associated with setup and changeovers.
In Summary
Liquid resin molding is often less expensive than injection molding due to lower tooling and equipment costs, greater flexibility and suitability for low to medium production volumes, and potentially lower material and operational costs. While injection molding is ideal for high-volume, high-precision manufacturing, liquid resin molding offers a cost-effective alternative for prototyping, custom parts, and smaller production runs.