Weld lines, also known as knit lines, are a common injection molding defect that can affect both the appearance and strength of molded plastic parts. As an injection molder, it’s crucial to understand what causes these defects and how to prevent them.
In this definitive guide, as a professional plastic injection molding manufacturer, we’ll cover everything you need to know to solve weld line issues, including:
- What are weld lines and what causes them
- The impact of weld lines on plastic parts
- Tips for preventing weld lines
- How to fix existing weld lines
- Advanced solutions for stubborn weld line problems
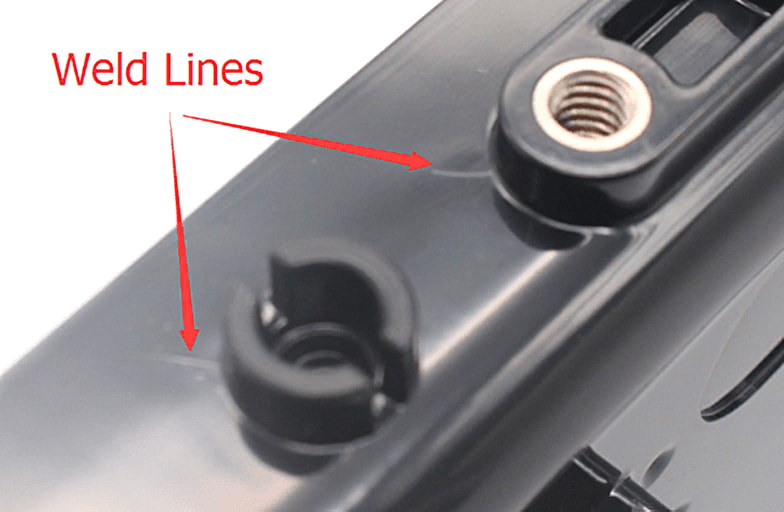
What Are Weld Lines and What Causes Them?
When molten plastic flows into a mold cavity, it moves in a continuous flow front. If the flow hits an obstruction like a hole, boss, or core pin, it splits into two separate flow fronts that flow around the obstruction. When the flows rejoin on the other side, they’re supposed to fuse back together into one continuous flow.
However, if the two flow fronts don’t mix properly, a visible line called a weld line forms at the point where they meet. The plastic along the weld line will have different material properties than the surrounding plastic.
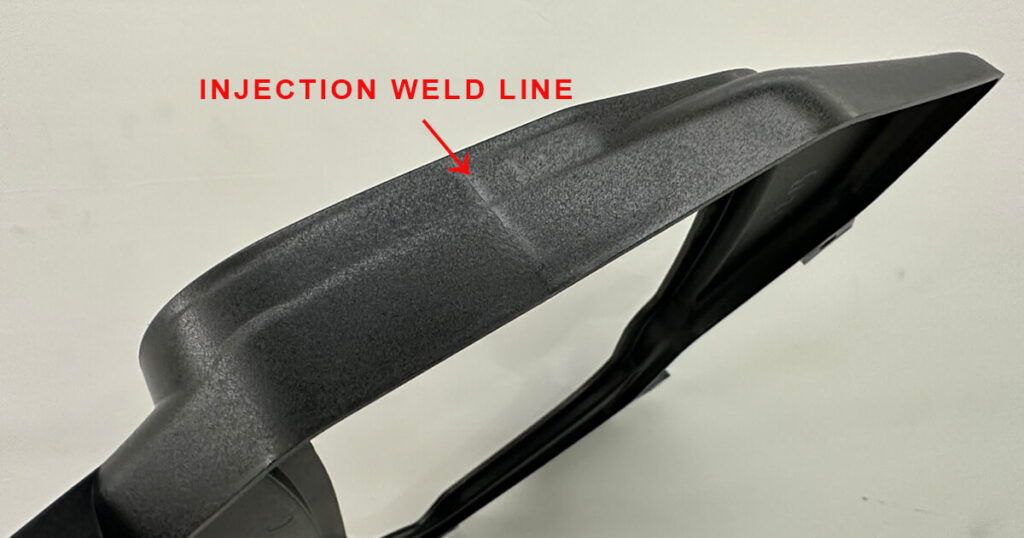
Weld lines form due to:
- Obstructions in the flow path like holes, ribs, edges etc. These split the flow into multiple fronts.
- Premature cooling of the flow fronts before they reunite. This prevents proper fusion.
- Trapped gases between flow fronts which keeps them separated.
- Uneven flow fronts meeting at different temperatures/speeds.
The Impact of Weld Lines on Plastic Parts
Weld lines can range from a barely visible cosmetic issue to severely compromising the strength of a plastic part along the weld line.
Some potential impacts include:
- Weakness – The weld line area has significantly lower strength, making parts prone to breakage.
- Stress cracking – Stresses concentrate at the weld line, increasing chances of cracking.
- Reduced impact strength – Weld lines tend to have poor impact resistance.
- Cosmetic defects – Weld lines can be visible as a scar on the plastic surface.
For load-bearing or safety-critical applications, the reduced mechanical properties along weld lines are unacceptable.
Even for non-critical applications, the cosmetic issues or increased chances of breakage mean weld lines should be minimized whenever possible.
Tips for Preventing Weld Lines
Here are some best practices to incorporate from the design stage to mold construction that can help avoid weld line defects:
Optimize Part Design
- Use uniform wall thickness to ensure consistent flow fronts. Variations exceeding 25% should be avoided.
- Minimize obstructions like holes, ribs and changes in wall thickness along the flow path.
- Place gates so that dangerous weld lines don’t form in critical high-stress areas. Simulate filling if required.
Build a Weld Line-Optimized Mold
- Minimize obstructions by changing component layout, consolidating hole locations etc.
- Use hot runner systems for better temperature control vs cold runners.
- Ensure adequate venting near expected weld line areas to prevent trapped gases.
- Polish cavities to prevent flow hang-ups that cause uneven flow fronts.
Dial-In Process Settings
- Increase melt & mold temperatures to improve flow and fusion but avoid degradation.
- Raise injection speed to fill cavity before premature cooling. Faster is better.
- Increase packing pressures to improve fusion along weld lines.
Careful application of these guidelines during design, moldmaking and processing setup should allow you to produce parts free of dangerous weld line defects.
How to Fix Existing Weld Lines
For existing molds producing parts with weld line defects, here are some process tweaks to try:
Melt Temperature
Increasing melt temperature can improve flow and bonding along weld lines. But don’t exceed the temperature range specified for the resin to avoid degradation issues.
Injection Speed
Faster fills allow less time for the melt to cool, keeping weld interfaces hotter. But don’t exceed recommended velocity limits.
Packing Pressure
Higher packing pressures physically push the two melt fronts together, improving bonding at the weld line. But apply pressure gradually.
Mold Temperature
Slightly higher mold temperatures slow down cooling, allowing better fusion. But drastic changes may cause other defects.
Gate Sequence
If weld lines always form in the last area to fill, changing gate opening sequence can allow problematic areas to fill while melt is still hotter.
These adjustments allow you to improve weld line strength without any mold or tooling modifications. But changes should be made gradually and their impact verified with measurements before settling on new settings.
Advanced Solutions for Stubborn Weld Lines
For challenging situations where weld line defects persist despite corrective attempts, several advanced fixes are possible:
Porous Inserts
Using porous steel inserts allows venting right along the weld line location to prevent trapped gases from keeping flows separate.
Flow Tab
A sacrificial tab protruding from the product acts as a flow leader, improving flow front uniformity. It fills last, taking the weld line with it when trimmed off in secondary ops.
Gas Counterpressure
Injecting inert gas like nitrogen to “push back” against advancing melt flow fronts can foil trapped gas issues if venting alone doesn’t suffice.
Material Change
Switching to a resin with better flow characteristics or lower shrinkage may intrinsically eliminate weld line problems at the cost of material performance impact.
Mold Modifications
If all else fails, welding a patch plate to “redirect” the problematic flow paths or replace problem inserts may be needed.
These advanced fixes demand expert assessment of mold construction, material characteristics and processing dynamics. Consult an experienced injection molding specialist before attempting these solutions to ensure success.
In Summary
As you can see, weld lines have the potential to severely diminish the functionality and appearance of injection molded components. But with vigilance during design and moldmaking coupled with proper processing, these defects can be avoided outright or at least rendered harmless.
Some trial and error is expected when dialing in a mold, but persistent weld line issues should prompt a reexamination of the fundamentals of part and mold design. In rare cases where weld lines simply cannot be designed out, purposeful placement away from high stress regions or secondary operations to eliminate them may be necessary.
Hopefully this guide gave you a comprehensive overview on solving weld line defects. As always, leveraging simulation and expert assistance is highly recommended when dealing with such injection molding problems. Let me know in the comments if you have any other tips for tackling weld lines!