Weld lines, also known as knit lines, are a common injection molding defect that can affect the appearance and performance of molded plastic parts. In this complete guide, as a plastic injection molding manufacturer, we’ll cover everything you need to know about weld lines, including what causes them, how to prevent them, and how to minimize their impact.
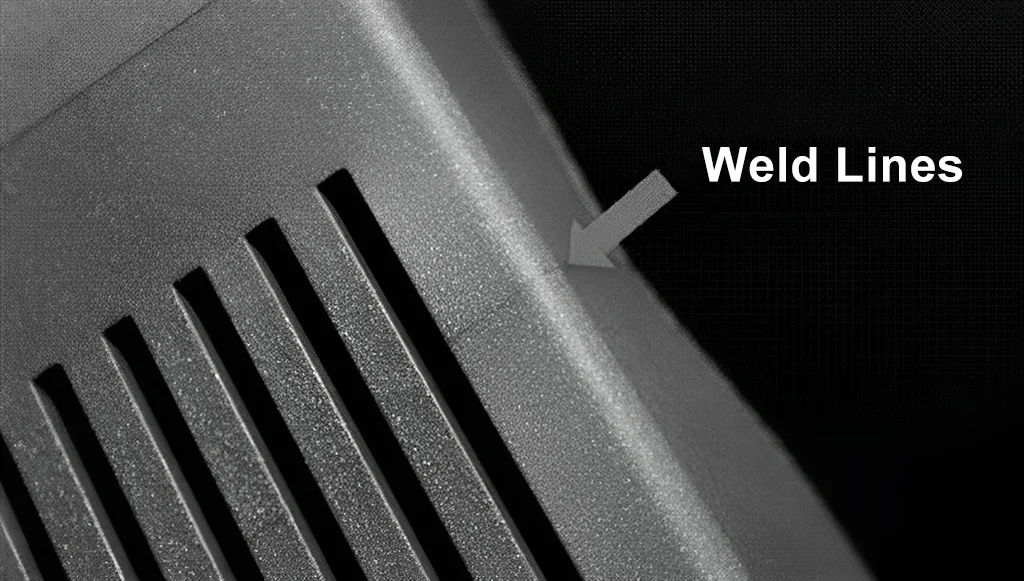
What Are Weld Lines?
Weld lines in injection molding occur when two flow fronts of molten plastic converge but do not fully blend together in the mold cavity. This leaves a visible line, discoloration, or surface depression where the two fronts meet.
The technical term for this phenomenon is a “cold weld” because the plastic starts to cool and solidify before the two fronts fully fuse. The result is an imperfect bond that creates a weak spot in the part.
Weld lines frequently form around holes, corners, inserts, changes in wall thickness, and other obstructions in the mold. As plastic flows around these objects, it splits into separate streams then rejoins on the other side.
What Causes Weld Lines to Form?
There are several potential root causes of weld line defects:
Insufficient Pressure – If injection pressure is too low, the two plastic flow fronts won’t have enough force to fully blend back together.
Premature Cooling – Molten plastic that’s too cold won’t properly fuse when the flows reconnect. This can happen if the injection speed is too slow or if there’s an unexpected drop in temperature.
Uneven Cooling – If one side of the obstruction cools faster than the other, you end up with two fronts at different temperatures that don’t meld correctly.
Trapped Gas – Air and gases emitted by the plastic during injection can get trapped at the weld line point, preventing the material from fusing.
Contaminants – Impurities in the plastic resin can lead to flow irregularities that inhibit proper fusion of the fronts.
Poor Venting – Inadequate venting causes gases to become trapped along the weld line.
Unbalanced Filling – Uneven flow rates between sections of the mold can lead to premature cooling on one side of the weld.
How Do Weld Lines Affect Parts?
For the most part, weld lines are purely a cosmetic issue that does not impact performance. However, in some cases they can cause weaknesses by:
- Reducing strength, durability and impact resistance
- Creating leak paths
- Introducing stress concentration points
The severity depends on the width and depth of the weld line, how well the polymer chains intermingled across the boundary, and whether it’s in a high-stress location.
Deep weld lines with little or no molecular bonding are most likely to affect function. But even shallow lines can potentially start cracks under certain conditions.
How to Reduce Weld Line in Injection Molding
While preventing weld lines completely may not be possible with some molds, here are solutions to help minimize the defects:
Optimize Part Design
- Use uniform wall thicknesses whenever possible to encourage even flow.
- Position any necessary inserts favorably to the flow pattern.
- Consider adding a fillet or generous radius at wall junctions.
Improve Mold Design
- Verify sufficient venting in problem areas. Enlarge vents if needed.
- Locate gates so flow continues together after converging.
- Reduce obstructions in the flow path such as ribs or holes.
Adjust Process Settings
- Increase injection speed and pressure.
- Raise barrel and mold temperatures slightly.
- Extend packing time to increase knit line pressure.
- Minimize use of mold release agents with silicones.
With attention to these areas, injection molders can reduce the occurrence of weld lines and produce stronger, better looking plastic parts. Proper venting, gating, uniform walls and optimal fill conditions make a big difference. Some trial runs may be needed to find the best balance for a given mold.
How to Prevent Weld Lines
Eliminating weld lines completely is usually impossible without removing necessary mold features. But you can take steps to minimize their occurrence and severity:
Optimize Gate Position – Locate gates so that plastic enters parallel to obstructions with enough space for flows to fuse downstream.
Balance Runner Layouts – Balance flow lengths and diameters so that plastic arrives at both sides of the weld line simultaneously.
Increase Wall Thickness – Extra material slows cooling to allow more time for the flow fronts to blend.
Add Vents and Overflow Tabs – Improved venting allows gases to escape rather than getting trapped between flows.
Polish Mold Inserts – Smoother surfaces of inserts reduces friction and shear heating that can contribute to uneven cooling between flow fronts.
Use Hot Runners – Hot runners keep the plastic molten for faster filling, less cooling variation, and better fusion of flow fronts.
Optimize Processing Settings – Dialing in the optimal temperature, pressure, speed, and time settings helps balance flow and reduce premature cooling.
How to Fix Existing Weld Line Problems
For parts already exhibiting weld line defects, here are some processing tweaks to try:
Increase Injection Speed – Faster filling reduces cooling time and makes it easier for polymer chains to intermingle properly across flow boundaries. But don’t increase speed so much that it causes other issues with fountain flow, jetting, or burning.
Raise Melt & Mold Temperatures – Hotter plastic fills the cavity faster, staying molten longer so chains can interdiffuse at the weld line for better strength. Just stay within the resin manufacturer’s recommendations.
Add Screw Back Pressure – Higher back pressure produces a more homogeneous plastic melt for smoother, more consistent flow.
Lower Clamping Force – Less clamp force allows tiny amounts of “flash” that enables gases to vent freely from weld locations.
Optimize Pack & Hold – Careful adjustment of pack pressure, time, and profiling can improve fusion at weld sites.
Minimizing the Appearance of Weld Lines
Although often unavoidable, there are methods of reducing the visibility of weld lines:
Gate Placement – Locating gates far from cosmetically sensitive surfaces pushes weld lines to less visible areas.
Material Selection – Translucent materials like crystal polystyrene naturally hide weld lines better than glossy materials. Or use special mold-flow enhanced grades.
Coloring – Darker resin colors conceal weld lines better than light colors.
Decoration – Painting, printing, texturing, or adding labels/logos can effectively camouflage surface weld lines.
Post-Mold Operations – Secondary machining, grinding, polishing, buffing, or abrasive flow machining can eliminate superficial weld lines.
So in summary, weld lines are a very common injection molding defect that happen when plastic flow fronts converge incorrectly. The keys to success are first understanding what’s causing them, then exploring different ways to prevent, minimize or conceal their effects based on what’s most critical for your application.
FAQs About Injection Molding Weld Lines
Here are answers to some common questions regarding weld lines:
Can you completely eliminate weld lines?
In most cases, no. Some level of weld line is generally unavoidable in conventional injection molding whenever the plastic flow has to split and rejoin around obstructions. But you can often minimize their occurrence through optimization.
When do weld lines actually weaken plastic parts?
Most are purely cosmetic. But if polymer chain entanglement is very poor across the intersection boundary, that spot will have substandard mechanical properties. Actual testing is the only way to know if there’s a meaningful loss of tensile or impact strength.
How do you know if a weld line will be a problem?
Factors that tend to make them more problematic are wider, deeper lines; high-stress locations; crystalline resins; glass-filled materials; and inadequate molecular interdiffusion. Short, shallow knit lines in non-critical areas are least likely to hurt performance.
Can changing the gate location eliminate weld lines?
Sometimes. The best bet is to locate gates so that plastic enters in a way that lets the split flows fuse back together downstream with ample distance to blend thoroughly. But repositioning gates risks creating new weld lines or other defects.
Why do some resins hide weld lines better than others?
Amorphous polymers like ABS, PC, and PMMA naturally diffuse back together better across flow fronts. Semi-crystalline resins like nylon, PET, and PP have a harder time intermingling and masking weld boundaries.
How can you strengthen a weak weld line?
If revising part geometry, tooling, and processing still doesn’t adequately fuse the boundary, you may need to specify a more flow-friendly material, add reinforcing ribs or gussets around the region, change to metal/composite inserts, or avoid high stresses near the location.
In Summary
So in closing, understanding the what, why and how of weld lines enables you to mold functional, durable parts faster through proactive optimization rather than reactive troubleshooting. Please reach out with any other weld line questions!