Undercut is one of the most common yet confusing concepts in injection molding. As a professional plastic injection molding manufacturer, I often get questions from customers about what undercuts are and how to design parts with them.
In this complete guide, I’ll explain everything you need to know about undercuts in injection molding – from what they are to why they matter and how to successfully implement them in your molds. Whether you’re new to injection molding or a seasoned pro, you’ll learn something new here.
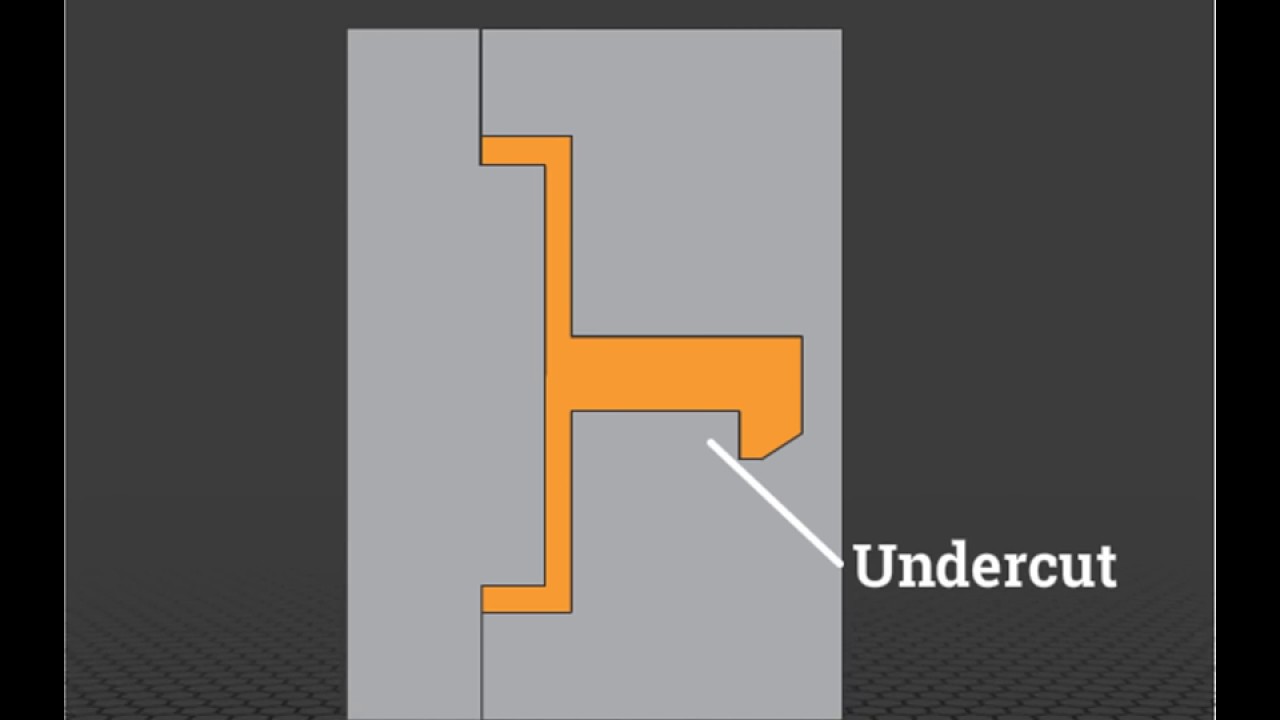
What is Undercut in Injection Molding?
Simply put, an undercut in injection molding is any feature that prevents the part from being pulled straight out of the mold. Undercuts create projections or indentations that stop the part from releasing cleanly when the mold opens.
Common examples of undercuts include:
- Threads
- Snap fits
- Slots
- Holes
- Textures
Without a way to get around the undercut, the part would be stuck in the mold and unable to eject.
Undercuts can occur on both the inside and outside surfaces of a part. External undercuts are features sticking out from the outer surface, while internal undercuts are indentations that go into the part.
Why Do Undercuts Matter in Injection Molding?
Undercuts may seem like nuisance features to avoid, but they serve important functional purposes in plastic parts. Here are some of the main reasons undercuts are used:
1. Enable Interlocking/Connecting Features
Undercuts allow for interlocking parts like snaps, slots, and threads that let plastic components connect together. These features are often vital for products like toys, containers, and consumer electronics.
For example, a threaded bottle cap needs undercuts on the inside surface to grip the bottle neck. Without them, the cap would just slide off instead of sealing.
2. Improve Strength and Rigidity
Undercuts can strengthen parts by creating I-beams and trusses on the inside surface. The projections help reinforce thin walls against bending and warping forces.
By optimally placing undercuts, you can maximize strength without using excess material or making overly thick walls.
3. Assist Part Function
In many cases, undercuts directly contribute to how a plastic part works. For instance, barbed tubing connectors use undercuts to create a tight seal for fluid flow systems.
The angled ridges grip tubing to prevent leaks and separation under pressure. Removing the undercuts would make the connectors completely ineffective.
4. Reduce Post-Molding Machining
Rather than machining complex geometries after molding, undercuts allow forming the full shape in the injection process. This saves secondary processing steps.
For example, a part needing precision internal threads could get them molded directly using collapsible cores rather than tapping afterwards.
5. Improve Aesthetics
Undercuts grant more freedom to create decorative textures, patterns, and contours on visible outer surfaces. Without them, most injection molded parts would be fairly plain.
As one example, undercuts help make wood grain and leather textures possible on plastic components.
Now that you know what undercuts are and why they matter for injection molded components, let’s look at how to actually implement them…
How to Successfully Use Undercuts in Injection Molding
Molding parts with undercuts requires specialized tools and techniques compared to simple straight-pull molds.
If designed poorly, undercuts can make parts impossible to manufacture or require expensive equipment to produce.
Here are 7 design tips for successfully implementing undercuts:
1. Use Bump Offs for Flexible Parts
When the material is flexible enough, bump offs allow molding small undercut features. A bump off is an insert that leaves extra space for the plastic part to momentarily deform as it releases.
Bump offs work well for parts made from thermoplastic elastomers (TPEs), rubber, polyethylene, and other flexible resins. They avoid moving mold components.
However, the undercut depth is limited to what the material can spring back from without taking a permanent set. Also, bump offs placed near stiff ribs or walls may tear rather than releasing cleanly.
2. Incorporate Shutoffs for Internal Undercuts
Shutoffs are protrusions that form negative space within a plastic part. As the name implies, they shut off flow into a specific area of the mold cavity.
Shutoffs attached to one mold half slide into an opening in the other half. They make internal undercuts possible without needing side actions.
Common applications include holes, handles, and snap fit hooks. Just be sure to include a pocket for shutoff clearance. Also, add draft to ease assembly without binding.
3. Use Side Cores for Deep External Undercuts
A side core is a retractable insert that forms an undercut then pulls sideways out of the solidified part. Side cores most often form threads, ridges, and external protrusions deeper than bump offs allow.
They attach to mold plates and actuate by cam pins, hydraulic cylinders, or servos to move perpendicularly, avoiding obstructions. Side cores do add complexity, but make deeper external undercuts feasible.
4. Specify Collapsible Cores for Interior Threads
Collapsible cores are segmented tool steel inserts designed to form undercuts then radially collapse for withdrawal. This approach works very well for internal threads and spiraled undercuts.
The individual segments flex inward in sequence, enabled by the tapered pin in the middle. Common applications range from bottle cap threads to drive shafts and medical parts.
5. Consider Secondary Operations for Simple Undercuts
For low volume production, post-molding secondary operations present a simpler way to achieve some undercuts. This avoids complex mold components.
Common secondary undercut operations include:
- Drilling holes
- Tapping threaded holes
- Machining slots/textures
- Laser cutting outlines
While saving on tooling costs, secondary ops do require additional process steps and have volume limitations depending on equipment.
6. Adjust Draft for Easier Part Ejection
For any undercuts, make sure adequate draft facilitates part ejection. Draft refers to the slight taper added to vertical walls – typically 1-3 degrees. This helps the plastic part cleanly release when the mold opens.
Without draft, undercut features could bind into the steel mold causing galling damage or breaking. Always apply draft where possible unless a perfectly straight wall is absolutely needed.
7. Partner With an Experienced Injection Molder
The most valuable resource for properly implementing undercuts is an injection molding company with proven expertise. An experienced molder has created molds with every type of challenging feature.
By seeking input early in the design phase, they can guide you to the best solutions for your undercut needs while optimizing the manufacturability. This saves you headaches down the road.
FAQ About Undercuts in Injection Molding
Here are answers to some of the most frequently asked questions on dealing with undercuts for injection molded plastic parts:
Are undercuts always bad?
No, undercuts serve very useful purposes and often can’t be avoided if the part is to function properly. The key is intelligently designing them for manufacture with the right techniques.
How do you design around undercuts?
Look for ways to change the geometry or split features to open along mold separation. Consider alternate join methods. Evaluate secondary operations instead. Explore special mold components if needed.
What does an undercut look like?
Any indentation or protrusion on the inner or outer surfaces that crosses the path of direct mold opening. Common examples are threads, snaps, holes through walls, ribs across cores, etc.
Can you injection mold undercuts?
Yes, through creative application of bump offs, side cores, collapsible cores, secondary operations, and other specialized methods. It just requires more consideration compared to straight-pull, draft-only designs.
How deep of an undercut can you mold?
The maximum depth depends greatly on factors like material flexibility, part geometry, chosen mold technique, and acceptable cycle times. Bump offs typically allow the shallowest undercuts, while complex mechanical side actions can form deeper recesses.
Conclusion
After reading this guide, you should now have a solid grasp of undercut concepts for injection molding applications.
The key takeaways are:
- Undercuts are protrusions and indentations that prevent straight part pull
- When designed well, they improve function and manufacturing
- Many techniques exist for molding different undercut types
- Incorporate with consideration of mold complexity vs. capabilities
I hope these tips empower you to confidently incorporate undercuts to enhance your next injection molded component! Let me know in the comments if you have any other questions.