Injection molding and extrusion are two of the most common manufacturing processes for producing plastic parts. At a glance, they may seem similar – after all, both processes involve melting down plastic and forming it into custom shapes.
However, injection molding and extrusion utilize different equipment and techniques to serve unique applications. As a professional plastic injection molding manufacturer, I will break down the key differences between these two pivotal plastic molding methods.
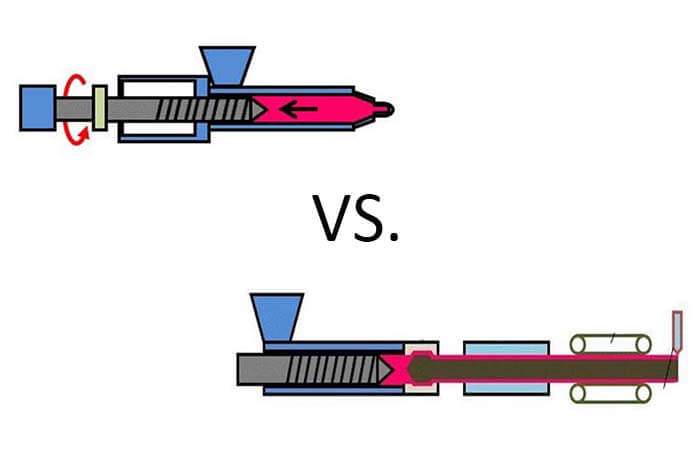
How Injection Molding and Extrusion Work
First, let’s look at how exactly injection molding and extrusion work.
The Injection Molding Process
Injection molding produces three-dimensional plastic parts by injecting molten plastic material into a mold cavity. Here are the key steps:
- Plastic pellets are fed into the injection molding machine’s heated barrel
- The pellets are melted down into a liquid state
- This molten plastic is injected under high pressure into a steel mold
- It flows to fill the mold cavity, taking its shape
- After cooling and solidifying, the mold opens and the part is ejected
This technique is ideal for intricate, detailed plastic products thanks to the mold’s precision. Parts like gadget cases, automotive trim, and medical supplies are often injection molded.
The Extrusion Process
Unlike injection molding, extrusion continuously forms plastic profiles with a fixed cross-sectional shape. This is how it works:
- Plastic pellets are gravity-fed into the extruder barrel
- Friction from rotating screws melts the material
- This molten plastic flows through a die opening with the desired shape
- It emerges, cooling and solidifying into this continuous form
- The line is cut to length for further processing or use
With its continuous production, extrusion excels at items like pipes, tubing, fencing, and window frames.
Key Differences Between Injection Molding and Extrusion
Now that you know the fundamentals, let’s explore five major ways injection molding and extrusion differ:
1. Dimensionality
- Injection molding produces three-dimensional, discrete plastic parts. The enclosing mold cavity defines intricate forms.
- Extrusion makes two-dimensional, continuous plastic profiles with a fixed cross-section. Its shape governed by the die opening.
This makes injection better suited for complex geometries like enclosures and housings, while extrusion shines for uniform profiles like tubes and rails.
2. Setup Cost
- Injection molds are complex CNC-machined steel tools with many intricacies to enable detail. This makes them very expensive – often tens of thousands of dollars.
- Extrusion dies are simpler, mainly consisting of steel blocks drilled with the profile shape. Far cheaper than injection molds.
If producing low volumes, extrusion wins on cost. But with scale, injection molding becomes vastly more cost-efficient.
3. Speed
- Thanks to continuous production, extrusion offers higher overall throughput compared to injection molding.
- However, injection boasts faster cycles for individual parts, capable of molding thin-walled items in under 30 seconds once tuned.
So for very long parts like 12-foot pipes or sheets, extrusion is faster. But injection outpaces it for discrete components.
4. Strength
- The high pressures from injection molding enable stronger bonding between plastic molecules, bolstering strength. The enclosed mold also prevents air bubbles.
- As an open process, extrusion forms weaker bonds between materials. Plus, trapped air can manifest as voids in the finished profile, risking structural integrity.
Applications where reliability matters favor injection molding plastic over extruded forms.
5. Tolerances
- Thanks to precision steel molds, injection molding can reliably hold dimensional tolerances down to +/- .005 inches for tight clearance fits.
- The open nature of extrusion makes it harder to achieve the same consistency, usually only holding around +/- .010 inches tolerance.
Thus, injection molding works for assemblies requiring tight clearances like connectors and fittings.
Example Applications: Injection Molding vs Extrusion
Their specific strengths make injection molding preferable for:
- Intricate enclosures, frames, and housings
- Interlocking connectors and fittings
- Small, detailed plastic products
- Low-volume production
Meanwhile, common extrusion applications include:
- Plastic pipes and tubes
- Railings, rods, and bars
- Fences and window profiles
- Films and plastic sheeting
- High-volume production
Both serve important roles across industries like construction, consumer goods, and more.
Bottom Line: Injection Molding vs Extrusion
In essence, injection molding excels at complex, three-dimensional plastic components, while extrusion shines for long, continuous, two-dimensional profiles.
Injection molding suits small batches thanks to lower tooling costs, while extrusion only becomes affordable at production scales. Determining application requirements helps select the ideal process.
With this overview of their differences and capabilities, you can make an informed choice between injection molding versus extrusion for your next plastic manufacturing project. Reach out if you need assistance selecting the best technique!