Injection molding relies on having the right amount of molten plastic, or “shot size”, to completely fill the mold cavity. The cushion refers to extra shot capacity beyond what is required to fill the mold. This plastic cushion serves the vital purpose of maintaining pressure against the cooling, shrinking material in the mold during the packing phase of the injection molding cycle.
Understanding cushion helps molders optimize part quality, tolerances, and consistency. Read on, as a professional plastic injection molding manufacturer, I will break down this critical injection molding concept.
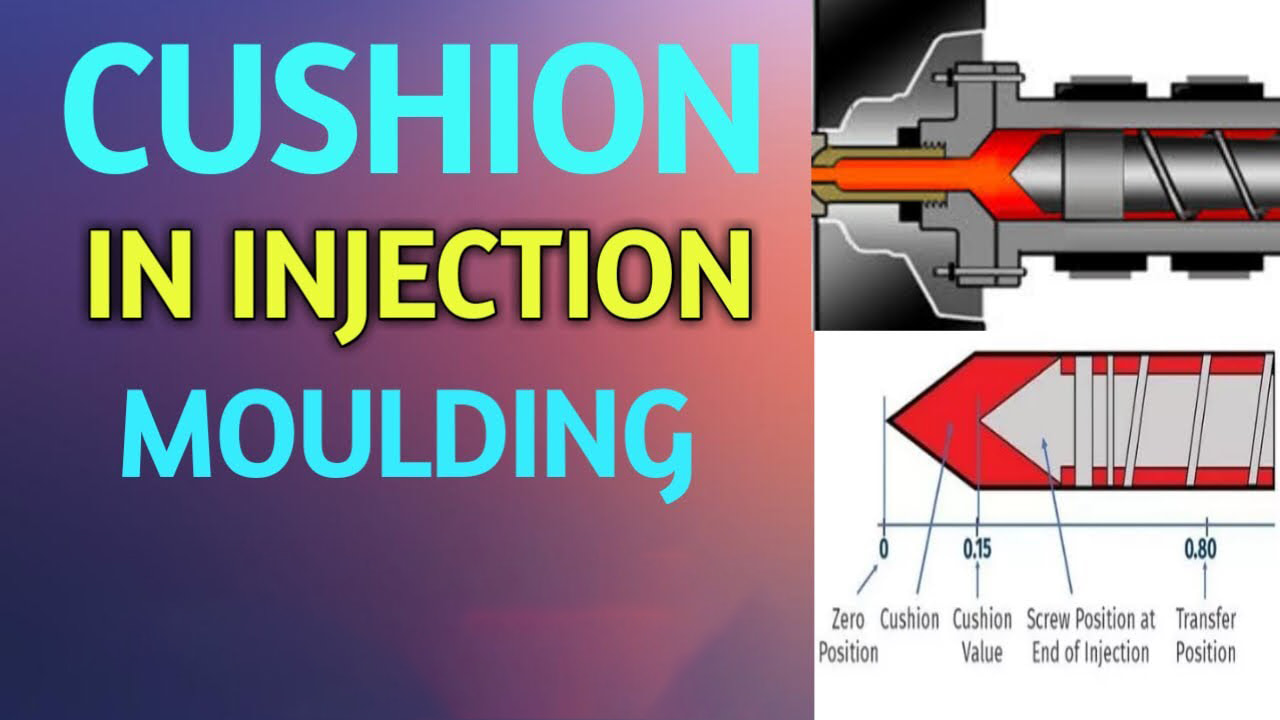
Why Cushion Matters in Injection Molding
Maintaining pressure during packing is key for proper part formation. As hot plastic flows into a relatively cooler mold, it starts losing heat to the mold walls. The cooling plastic also shrinks in volume. Without adequate pressure, the material would shrink away from the mold surfaces, reducing part accuracy and quality.
The cushion provides a reservoir of molten plastic to keep exerting pressure on the curing material. This pressure drives additional plastic into the shrinking areas to maintain contact with the mold. Proper packing pressure is required to produce complete, dimensionally accurate parts.
Preventing Part Defects
Inadequate cushion can directly cause common part defects like short shots, sink marks, and warped parts. As packing pressure drops off prematurely, material shrinkage forms visible defects. Maintaining packing pressure for the required duration helps ensure complete parts within spec.
How Cushion Works in Injection Molding
Now that you know why cushion matters, let’s look at how this extra shot capacity enables better part quality:
The Injection Unit
Modern injection molding machines use a screw inside a heated barrel to melt plastic pellets. As the screw rotates, it moves the melting material forward through a check valve. The buildup of molten plastic in front of the screw tip is called the shot.
Filling the Mold
For the injection process, the screw moves forward, acting like a plunger to force the shot through the nozzle, sprue, runners and into the mold cavities. The stroke of the screw determines the shot size.
Packing Out the Part
After filling the mold, molten plastic continues flowing in during the packing phase. This applies pressure against the cooling material, shrinking inside the mold.
Maintaining this pressure is key to producing complete, dimensionally sound parts. As the material loses heat and shrinks, the packing pressure drives extra material in to compensate. When plastic pressure equals mold clamp force, the gate freezes off, ending the packing phase.
Why Cushion is Vital For Packing Pressure
Packing out the mold requires plastic pressure pushing against the curing material. Without a cushion between the screw tip and mold inlet, there would be nothing to exert this essential pressure during packing.
Measuring Cushion
Cushion refers to the leftover shot capacity between the end of injection travel and maximum screw stroke. It is typically measured as a linear distance between the screw tip and nozzle at the end of packing.
Typical cushion distance for a standard size machine ranges from 5 – 10 mm. Larger injection units require appropriately bigger cushions. The optimum size cushion depends on the mold, material, fill rate and other factors.
Monitoring Cushion
Since cushion enables packing pressure, maintaining a consistent cushion shot-to-shot is key for part consistency. Allowable variation depends on part tolerance requirements.
Typical cushion tolerance is ±10%, providing enough leeway for machine variances while enabling repeatable performance. Historical data review helps molders optimize allowable cushion variability based on capability requirements of each mold.
How to Increase Cushion in Injection Molding
If your current cushion is inadequate, here are proven ways to safely increase it:
1. Check Your Process Settings
Start by ensuring your transfer and injection speeds aren’t set too fast. Excessive velocity can “overrun” available cushion prematurely.
Next, reduce your pack and hold pressures. Using lower pressures often allows for increased cushion accumulation.
Finally, extend pack times slightly. This gives extra leeway for the screw to progress before locking in position.
2. Increase Back Pressure
Dialing up back pressure directly resists screw movement, allowing more material to build up. Start conservatively and increment upwards gradually.
Too much back pressure risks overheating/degrading the polymer. Carefully observe for any indications of unwanted material property changes.
3. Verify Nozzle Shutoff
If nozzle openings don’t fully close off between shots, melt can flow backwards unnecessarily.
Inspect check rings, recip screws, and hot runner nozzles for proper sealing. Replace worn components as needed.
4. Lower Fill Speeds
Filling the mold too rapidly reduces how much cushion gets established upfront. Try reducing fill speeds in small increments until target cushion value stabilizes.
Excessively slow fill rates can also cause issues though. Ensure acceptable part appearance is maintained when adjusting fill speeds.
5. Check for Worn Components
Over time, barrels, screws, and check valves wear down and lose consistency. Have a qualified technician inspect key tooling components and replace if tolerances have drifted significantly.
While fixing worn parts can get expensive, restoring injection molding machine health pays dividends in improved process capability and reduced scrap rates.
Dialing in Proper Cushion Size
Several factors determine appropriate cushion size for each mold:
- Machine Size – Larger injection units need a bigger cushion distance.
- Material Viscosity – Higher viscosity materials require more cushion.
- Fill Rate – Faster fill demands more available pressure.
- Part Size – Larger parts need extended packing time.
- Tolerance Requirements – Tighter tolerances require less variance.
Within the operating window of these constraints lies the optimum cushion size and allowable variability. Pressure transducer sensors provide realtime cavity pressure data to help molders dial-in optimum cushion settings.
Once established, consistent adherence to these cushion specifications is vital for repeatable molding performance. Continual monitoring ensures any deviation gets corrected before producing bad parts.
Too Much or Too Little Cushion Can Cause Issues
Insufficient cushion provides inadequate packing pressure, while oversized cushions can overpack the material.
Oversized cushions also increase risks of degraded plastic entering the part. Finding the right balance avoids these defects. Historical data guides molders to optimize cushion for stable performance.
Takeaway
Maintaining packing pressure is essential to produce complete, dimensionally sound injection molded components. This packing reliance on pressure underscores the importance of cushion.
Tuning cushion enables molders to achieve necessary packing densities for each mold. Once defined, continually monitoring cushion is imperative to enable consistent output of good quality parts.
Understanding cushion sheds light on this vital element separating manufacturing high performance components from producing scrap.