Shear rate is one of the most important concepts to understand in injection molding. As a plastic injection molding manufacturer, today we’ll cover that optimizing shear rate is crucial for producing high-quality parts while protecting your molds.
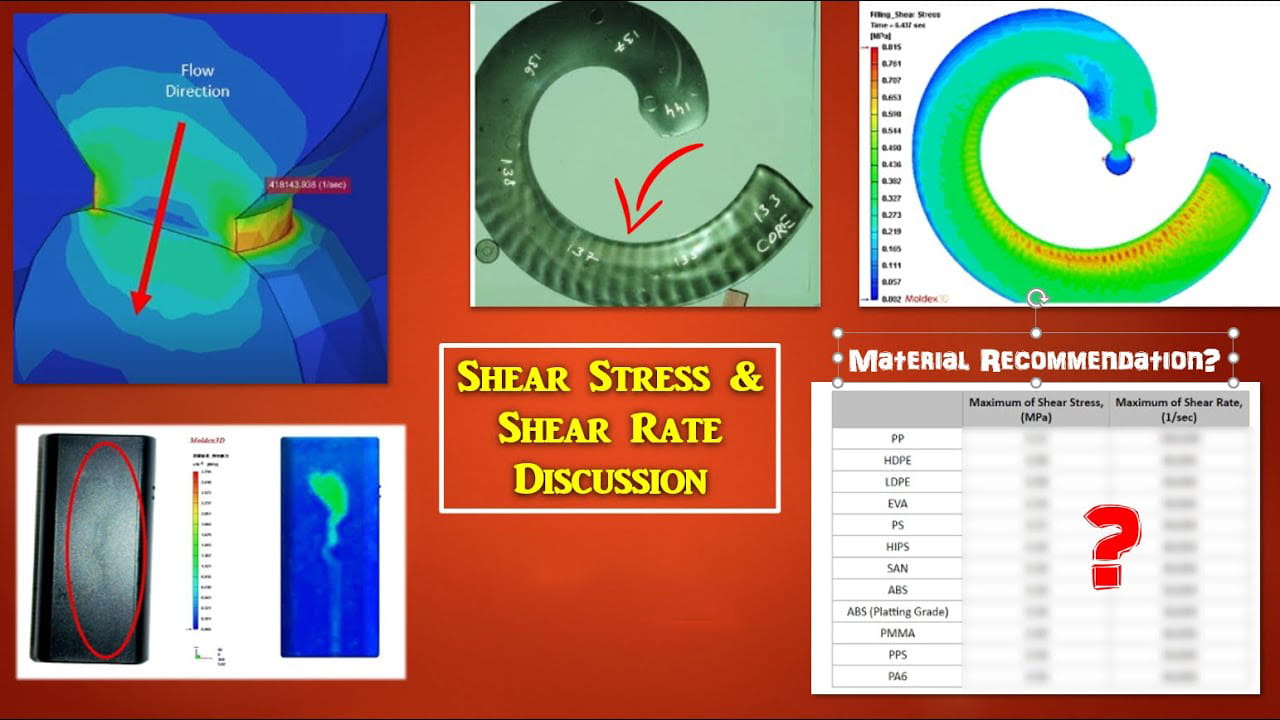
What Exactly is Shear Rate in Injection Molding?
In simple terms, shear rate measures the change in velocity between layers of molten plastic flowing through your mold. It indicates how fast the material is being “sheared” as it flows.
The shear rate is highest near the walls of the mold cavity where the plastic travels the slowest. Towards the center of flow, shear rate drops to zero since internal layers move at the same speed.
Controlling shear rate is critical because excessive levels can degrade the polymer, leading to defects and poor performance. Each resin has an optimal processing window for shear rate. Go too high and you’ll create issues; too low and the process becomes inefficient.
Why Understanding Shear Rate Matters
Let’s walk through some reasons why shear rate is worth learning about:
Improve Part Quality
Excessive shear rates generate heat through viscous dissipation, raising the melt temperature. These temperature spikes across the flow front create imbalanced conditions, negatively impacting dimensions, appearance, and mechanical properties.
Proper shear rates ensure stable, uniform melt conditions for consistent high-quality parts.
Protect Molds
In addition to part defects, excessive shear can literally destroy components like gates, pins, and cavities through erosive wear. Costly mold repairs or replacements can quickly erase your margins.
Using appropriate shear rates extends tooling life so you can keep producing parts.
Optimize Materials Use
Each resin has a shear rate processing window that balances quality and efficiency. Operations falling outside this sweet spot result in wasted materials and time.
Tuning your process shear rates to match the polymer window reduces scrap and ensures you’re running lean.
Standardize Processes
Documenting optimum shear rate guidelines gives technicians a processing target and helps reduce shoot-to-shoot variations. New molds can be developed to match shear rate limits.
Repeated success depends on well-defined, standardized procedures – shear rate is a key piece of that puzzle.
How to Calculate Shear Rate
Now that you know why shear rate matters, let’s look at how it’s actually calculated.
There are a few equations we’ll cover, depending on factors like:
- Channel geometry – round, rectangular, annular
- Resin type – Newtonian, non-Newtonian
- Analysis complexity – basic approximations or advanced modeling
We’ll focus on two straightforward formulas suitable for most purposes.
Shear Rate Formula for Round Channels
For simple circular cross-sections like nozzle tips, sprues, and direct gate molds, the common shear rate equation is:
g = (4 x Q) / (π x R3 x n)
Where:
- g = Shear Rate (1/s)
- Q = Volumetric Flow Rate (m3/s)
- R = Radius of Channel (m)
- n = Power Law Index
Let’s break this down quickly:
- Volumetric flow rate is the amount of plastic flowing per second, calculated from shot size and fill time
- Radius comes from your specific tooling dimensions
- The power law index defines how the plastic’s viscosity changes with shear rate
So this gives you shear rate based on how fast material flows through a given circular channel.
Formula for Rectangular Channels
In the case of non-round sections like film gates, slot gates, edge gates, this rectangular version is better:
g = (6 x Q) / (H x W x n)
Where:
- H = Gate or Channel Height
- W = Gate or Channel Width
The variables here work the same way as the round channel equation. This adaptation just fits the geometry better.
Real-World Example
Let’s see how we’d actually use these formulas…
For a polypropylene part with:
- 30 gram shot weight
- 0.8 second fill time
- 3 mm diameter direct sprue gate
- Power law index of 0.3
The volumetric flow rate would be 30 grams / 0.8 seconds = 37.5 cm3/s
Plugging this into our round channel shear rate equation gives:
g = (4 x 37.5 cm3/s) / (π x (0.3 cm)3 x 0.3)
= 10,753 1/s
So our process creates 10,753 1/s of shear rate. We’d compare this value to shear rate guidelines from the resin supplier to make sure it falls in the recommended range.
The Takeaway
Computing and controlling shear rates provides molders incredible benefits for quality, efficiency, and standardization.
While the concept is straightforward, optimizing shear rate still requires material knowledge and analysis. Partnering with your resin supplier to characterize new polymers is the best way to determine ideal processing recommendations.
Once shear rate limits are established for your particular formulation, it becomes much easier to develop robust injection molding processes.