In injection molding, the runner is a crucial component that guides molten plastic from the injection nozzle to the mold cavities. As a professional plastic injection molding manufacturer, I am writing this comprehensive guide to cover everything you need to know about runners, including types, design considerations, how they affect part quality, and more.
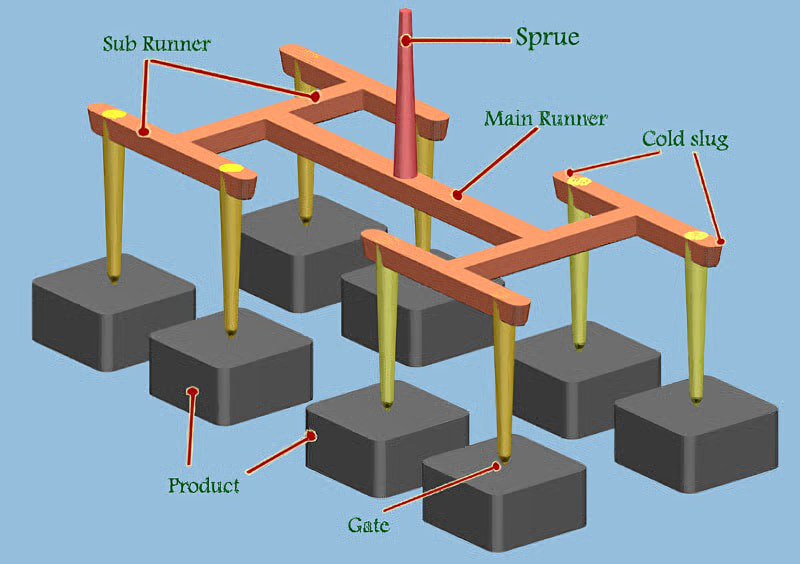
What is a Runner in Injection Molding?
A runner is a channel cut into the mold that transfers molten plastic from the injection nozzle to the cavities during the injection molding process. It serves as a passageway that allows the plastic to evenly flow into the cavities.
Well-designed runners are essential for producing high quality, consistent parts. The size, shape, and position of runners directly impacts how fast cavities fill, material waste, part quality, and cycle times.
Runner System Components
The complete runner system is made up of a few key components:
Sprue – The first segment the molten plastic enters through the injection nozzle. The sprue feeds material into the runners.
Runners – Channels of various lengths and diameters that distribute material to mold gates.
Gates – The final constricted transition points from runners into part cavities. Gates regulate flow into the cavities.
Together, these elements work cohesively to deliver an even flow front of plastic into all cavities simultaneously. The end goal is to produce fully filled parts free of defects in the shortest cycle times possible.
Cold Runner vs Hot Runner Systems
There are two main types of injection molding runner systems – cold runners and hot runners:
Cold Runners
Cold runners solidify inside the mold along with the molded parts. The sprue, runners, and parts all remain connected as one solid piece upon ejection. Material filled cold runners represent waste that needs to be removed and reprocessed or discarded.
Cold runners allow for simpler molds, lower tooling costs, design flexibility, and accommodate a variety of resins. However, they generate more waste and have longer cycle times compared to hot runners.
Hot Runners
Hot runners use heated manifolds and nozzles to keep plastic molten as it flows into cavities. Upon ejection, solidified parts are ejected without sprues or runners attached. This reduces waste and speeds up cycle times.
Hot runner molds are more complex and costly to produce than cold runners. Although long term, waste reduction can provide substantial cost savings in high volume production scenarios.
Why Proper Runner Design is Key
The performance of any injection mold is highly dependent on the runner system design. Here’s why optimizing your runner layout is so important:
Fill Time & Pressure
Properly sized runners fill cavities faster by enabling flow with less pressure loss. Thin, long runners can prematurely freeze causing short shots.
Part Quality
A balanced runner design delivers an even melt flow front to all cavities. This consistency produces uniform properties and appearance in every part. Unbalanced systems lead to variances between cavities causing quality issues.
Cycle Efficiency
Excessive runners mean increased solidification and cooling times, slowing down cycles. An optimized layout minimizes runner volume to rapidly cool and eject parts.
Material Savings
Shorter, smaller diameter runners reduce wasted sprue and runner plastic. This leads to significant cost savings, especially in cold runner applications.
Key Runner Design Guidelines
Here are crucial tips for engineering an effective runner system layout:
Sizing
1. Diameters – Should be sized appropriately based on factors like part wall thickness, flow length, melt properties, and injection speed/pressure. Typical diameters range from 2mm to 10mm.
2. Lengths – Minimize all runner segments – keep runs from sprue to gates as short as possible. Long flow lengths sap pressure and promote early freezing.
Balancing
3. Equal Flow Paths – Ensure routes to each cavity are the same length to provide balanced conditions. Utilizeflow simulations to validate performance.
4. Strategic Gates – Increase gate counts/locations to provide more direct cavity access and minimize runner volume.
Configuration
5. Simplicity – Use the least complex system that satisfies performance targets. Simpler is better. Evaluate need for any secondary runners or sub-gates.
6. Streamlined Layout – Gently curve runners to follow contours rather than sharply turning at angles. Eliminate dead zones where material can stagnate.
Properly addressing these design elements sets up any runner system for reliable success, maximizing quality and efficiency.
How Runners Impact Injection Molded Part Quality
Flaws in the runner layout often manifest as visible part defects or performance issues. Here’s how:
Unbalanced Filling – When flow paths contain drastic differences in pressure losses, cavities fill at different rates. Slower filling allows material to cool unevenly within the mold, creating visible weld lines, sink marks, voids or warpage.
Premature Freezing – Inadequate runner sizing relative to flow lengths chokes off pressure, allowing melt to freeze before completely filling. Results in short shot parts with incomplete details.
Shearing – Excessive angular transitions or constrictions degrade polymers through overshear heating and cooling. Leads to localized material property changes.
Each of these common defects point back to underlying shortcomings in the runner design.
Runner Design Optimization & Analysis
Creating an optimal runner system is a complex undertaking requiring experience and specialized simulation tools. Here is a general overview of the modern design approach:
1. Conceptual Layout – Initial runner configuration is roughly sketched out based on part geometry, material selection, processing properties, and experience.
2. Moldflow Analysis – Detailed simulation studies evaluate proposed layouts under real world conditions. Makes accurate performance predictions. Allows exploration of multiple “what-if” ideas quickly to hone strategy.
3. Final Validation – Optimal designs derived from analysis are ultimately proven empirical by actual mold sampling. Provides opportunity to tweak settings prior to full scale mold fabrication.
Leveraging analysis methods to inform designs prevents costly corrections down the road should suboptimal choices make it into steel. The upfront time investment pays back substantially over a mold’s lifespan.
Injection Molding Runner FAQs
Here are answers to some frequently asked questions about injection molding runners:
What is the best runner diameter?
Typical diameters range from 2mm up to 10mm depending on factors like flow length, material viscosity, and injection speed. Broader runners may allow faster fill rates but solidify slower, increasing cycle times.
Where should gates into cavities be located?
Gates should feed into thicker wall sections of parts at minimal visible exterior locations. This enables fastest fills and easiest degating while minimizing visible blemishes.
How should runners branch off to multiple cavities?
A main runner should split into evenly spaced branches leading directly to each cavity gate at the same lengths. This ensures simultaneous balanced fill conditions across all cavities.
What is the benefit of a hot runner vs cold runner?
Hot runners eliminate waste while enabling faster cycles. But cold runners cost less initially and work with more materials. Determine tradeoffs based on application-specific priorities or constraints.
How long should an injection molding runner be?
As short as possible. In general, keep runs below 2ft in length if application allows. Any longer risks excessive cooling and pressure losses degrading end part quality.
How do I create the most cost effective runner system?
Focus on minimizing dimensions to use least amount of material while still sufficiently filling parts. Strategic gate placement also minimizes degating labor. Avoid overly complex geometries when simpler route produces same results. Use analysis tools to find optimal trade-offs.
Conclusion
Optimizing runners is crucial for achieving manufacturing success in injection molding across any industry. Although invisible to end users, these “behind the scenes” components truly stage everything needed for reliable, efficient production of high quality plastic parts from each and every mold.