Injection molds are commonly made from metal, usually steel or aluminum. The material choice depends on factors like cost, quality, production run length and part complexity. As a professional plastic injection molding manufacturer, I will lead you in taking a closer look at the most popular mold materials used in injection molding.
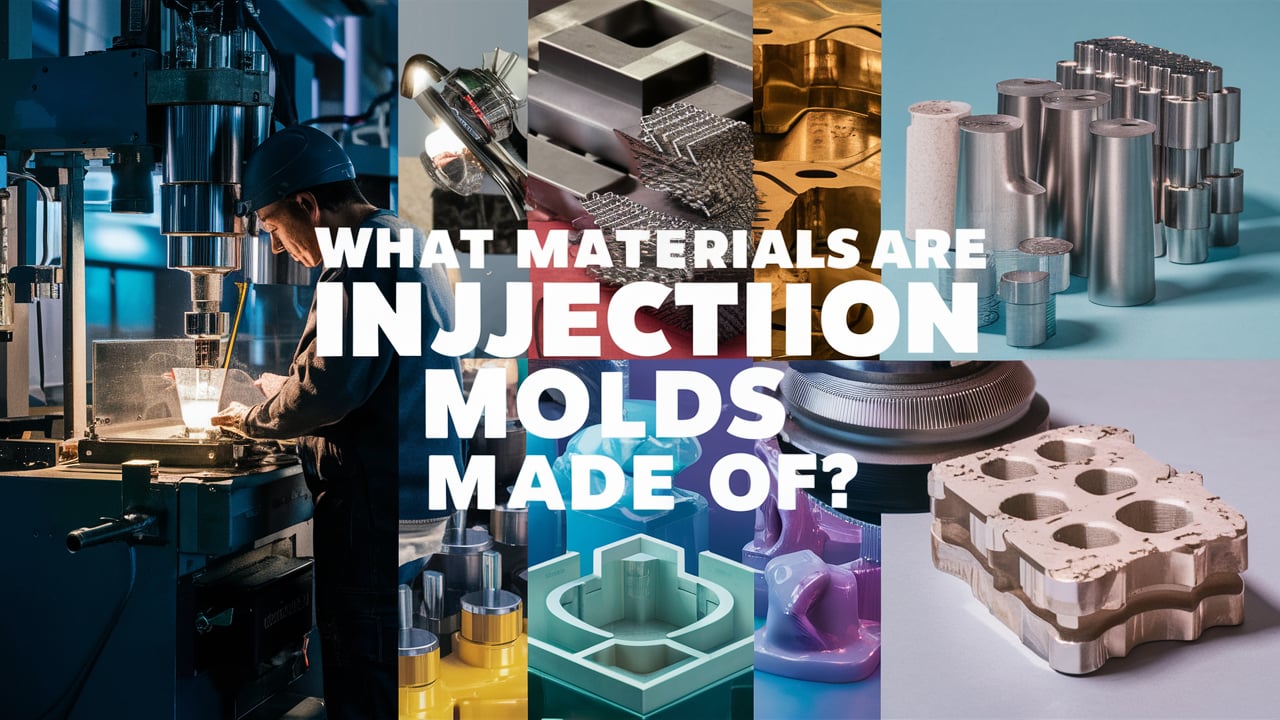
Why Material Selection Matters
Choosing the right material is critical for injection molds. The mold must withstand high temperatures, pressures and abrasive wear during repeated injection molding cycles. Using the wrong material can lead to mold damage or failure, resulting in production delays and costs.
The mold material also influences part quality. A precision steel mold will produce higher quality parts with tighter tolerances compared to a prototype aluminum mold. The material even impacts cost – an aluminum mold costs far less than pre-hardened steel, but won’t last nearly as long.
Clearly, the mold material choice carries weighty tradeoffs between quality, durability and cost.
What Materials Are Injection Molds Made Of?
Injection molds are commonly made from metal, usually steel or aluminum. The material choice depends on factors like cost, quality, production run length and part complexity. Let’s take a closer look at the most popular mold materials used in injection molding.
Most Common Injection Mold Materials
The majority of production injection molds are made from metal, usually steel or aluminum alloys. Here’s a run-down of the most popular mold materials.
1. Pre-Hardened P20 Steel
P20 steel is considered the “workhorse” mold steel thanks to its combination of machinability, durability and cost-effectiveness. It’s commonly used for molds with smaller cavities, or short production runs below 500,000 cycles.
The main downside is that P20 won’t withstand ultra high-volume production. For longer runs, hardened tool steels are preferred.
2. Hardened Tool Steels
H13 and S7 tool steels offer exceptional durability for long production runs exceeding 500,000 cycles. The hardness rating ranges between Rockwell 50-55 for H13 steel and Rockwell 55-60 for S7 steel.
These tool steels are heat treated to achieve maximum hardness and wear resistance. This comes at a cost premium over P20 steel but ensures longevity over millions of molding cycles.
3. Aluminum & Beryllium Alloys
For prototype and low-volume molds, aluminum alloys like 7000 series offer cost savings over steel with decent durability. Beryllium copper alloys are also used, combining wear resistance with rapid heat transfer for fast cycle times.
The main downside is shorter overall mold life compared to steel, making aluminum unsuitable for high-volume production.
Exotic Metal Materials for Injection Molds
While steel and aluminum make up 90% of injection molds, new exotic alloys are emerging for extreme performance needs:
Beryllium Copper Alloy – Combines ultra high thermal conductivity with good wear resistance. Allows very fast cycle times. Used for extremely high-volume, cost-sensitive plastic parts that require sub 60-second cycles.
Aluminum-Beryllium Alloy – An advanced aluminum alloy with beryllium additive for 5x higher rigidity versus 7075 aluminum. Machines easily while allowing thinner, high precision mold cores. Used for complex geometries needing extreme rigidity.
Maraging Steel – An ultra-high strength steel that achieves double the hardness rating of S7 tool steel (Rockwell 60+), with excellent dimension stability and polishability. Used for complex geometries with zero tolerance that require extreme precision and durability over millions of cycles.
Inconel Alloy – A superalloy with extreme heat and corrosion resistance. Withstands over 1000°C for molding high temperature resins like PEEK, without corrosion. Much costlier than tool steel but offers unmatched performance capabilities.
Factors That Influence Material Selection
Many variables influence the best material choice when tooling an injection mold, including:
Part Geometry & Tolerances – Precision molds require harder, wear-resistant materials like tool steel. More basic geometries allow softer metals like aluminum.
Production Volumes – Steel molds handle ultra high-volume production above 500,000 cycles. For short runs below 100,000 parts, aluminum molds save on costs.
Cycle Times – Beryllium copper or aluminum alloys maximize heat transfer for fast cycles under 60 seconds. Steel molds cycle slower but offer longer overall tool life.
Part Performance Needs – Advanced resins like PEEK require steel molds to achieve high precision and performance parts. Basic resins like PP are more forgiving for aluminum molds.
Costs – The mold material significantly influences overall costs. Aluminum and beryllium molds cost far less upfront but wear faster than steel. This must be traded off against production run volumes and lifespan requirements.
Key Takeaways on Injection Mold Materials
The material choice carries major tradeoffs between part quality, tooling costs and durability. Hardened tool steels offer exceptional performance and lifespans above 5 million shots, at a premium cost. Aluminum molds provide a cheaper option for prototypes and short runs up to 100,000 parts.
New beryllium alloys and maraging steels push mold capabilities further for precision geometries needing ultra high cycles. While exotic alloys enable extreme mold performance, pre-hardened P20 steel covers nearly 90% of injection molding applications with a proven balance of quality, durability and cost-effectiveness.