Plastic injection molding is one of the most versatile and cost-effective manufacturing processes available today. It allows for the mass production of everything from toys and household items to medical devices and auto parts.
However, despite its prevalence across countless industries, plastic injection molding comes with some notable downsides and limitations that engineers and product designers need to take into account. As a professional plastic injection molding manufacturer, I will list them in this article.
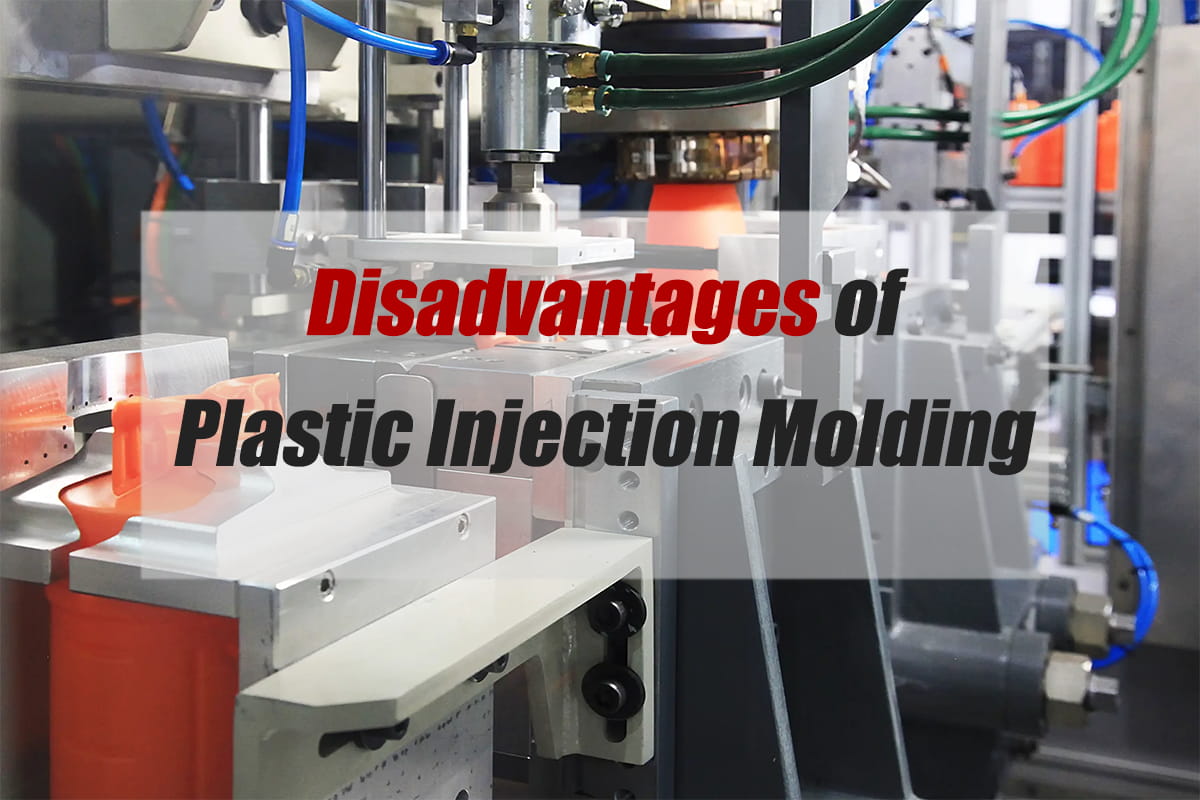
What are the Disadvantages of Plastic Injection Molding?
High Initial Investment Costs
One of the most significant disadvantages of injection molding is the high initial investment required. Before a single part can be produced, extensive upfront costs are necessary for the injection mold tooling itself.
The cost of molds for standard plastic products typically ranges from $1,000 to $5,000. However, for larger molds built to export-quality standards, prices routinely exceed $50,000 and can even soar to several hundred thousand dollars.
Beyond the injection molds themselves, there are costs associated with mold design, extensive testing and prototyping, production planning, fixturing, and quality assurance measures as well.
When accounting for all these upfront costs, injection molding only becomes economically viable at production volumes exceeding 100 to 150 pieces. For very small production runs measured in dozens or hundreds of units, additive manufacturing technologies like 3D printing or CNC machining are generally more cost-effective.
Long Lead Times
In addition to high initial investment costs, long lead times present another downside to injection molding plastic components. From start to finish, expect the entire process to span 10 to 12 weeks at a minimum.
Here is a rough breakdown of the injection molding timeline:
- 2-4 Weeks: Design and Engineering
- 4-6 Weeks: Mold Manufacturing
- 2-4 Weeks: Samples, Testing, Modifications
- 2+ Weeks: Production, Assembly, Shipping
As this timeline illustrates, production doesn’t start overnight with injection molding. In particular, depending on part complexity, mold tooling lead times routinely exceed one month.
For engineers and project managers operating on tight deadlines, these long lead times require careful planning and coordination if launch dates are to be met. Alternatively, interim solutions like 3D printing production-grade prototypes can help verify designs while injection molds are still being tooled.
Quality Control Challenges
Despite its precision and consistency, injection molding production is still prone to quality issues if not executed properly. Defects like short shots, flash, warpage, and mold lines can quickly render complex components unusable without remedial actions.
Most defects originate from suboptimal mold design or inadequate process controls on key parameters like temperature, pressure, clamp force, and injection speed. As more variables and tolerances stack up, maintaining consistency poses an increasing challenge.
For instance, tiny changes in plastic resin moisture content and mold temperature can significantly alter viscosity and flow rates, causing subtle – but unacceptable – variation between shots.
Establishing robust quality control measures is therefore essential, especially when partnering with a new injection molding partner. Comprehensive inspection checklists and layered approval processes help minimize risk.
Design Limitations
To benefit from injection molding on a mass production scale, plastic parts need to be designed with the process limitations in mind. However, for engineers more accustomed to machined metal components, adapting to the nuances of injection molded plastics can be less intuitive.
Ideally, wall thicknesses should be kept uniform to ensure even solidification as the molten plastic inside the mold loses heat. Variations in thickness can create stresses that manifest as cracks or warpages.
Undercuts and other geometries that prevent clean demolding also need to be avoided. Likewise, incorporating draft angles facilitates part ejection after the injection molded shot has cured inside the two-plate mold tool.
While lifters and sliders can alleviate some design constraints around undercuts, they add costs and reliability considerations into the mix. The need for side actions also limits the speed at which consecutive injection molding cycles can occur.
Material Performance Restrictions
Today’s modified resins and polymer alloys enable plastic injection molding to compete with – or even surpass – metals in certain applications requiring flexibility, corrosion resistance, electrical insulation, or precision.
However, injection molded plastics continue to lag behind aluminum and steel parts in key areas like ultimate tensile strength, sheer strength, rigidity, and wear resistance. These material limitations restrict their use in certain structural, load-bearing, and high durability applications.
On average, the maximum heat resistance for conventional injection mold grade plastics hovers between 180-220 °C, although specialty resins like PEEK and PPS can handle over 300 °C. Still, metals outclass plastics by wide margins for high temperature applications.
While metal components easily tolerate autoclaving, steam sterilization, or other aggressive sterilization modalities, such exposure risks warping or otherwise degrading plastic parts. Consequently, medical device engineers must vet the biocompatibility of each resin carefully.
Recycling Difficulties
Ideally, as sustainability becomes an urgent priority worldwide, manufacturers should be able to recover, sort, and reuse plastic resin after its useful life. However, recycling plastic faces substantial technical and economic barriers despite intense research and development efforts.
Broadly speaking, four factors complicate plastic recycling today, especially for mixed plastics:
- Separation and sorting
- Decontamination
- Identification
- Reprocessing
As an initial step, separating and sorting plastics by resin types is essential for recycling but tremendously labor-intensive since it currently requires manual effort.
Likewise, paints, metal inserts, labels, and adhesives prevent straightforward recycling and necessitate extensive decontamination to extract base plastic material.
In other cases, obscure resin codes make definitive material identification impossible. Even when resin chemistry can be established, differences in polymer chain lengths, copolymer blends, and material age can still affect properties and confound processing.
Economically speaking, the high labor component for sorting waste plastics cannot be justified except for high purity, high volume resin streams. But infrastructure investments in chemical recycling could someday improve viability through increased process automation.
Conclusion
Without a doubt, plastic injection molding will continue dominating global manufacturing thanks to its cost-effectiveness, versatility, and precision. However, engineers evaluating the process must temper expectations by considering its limitations and challenges as well.
In particular, high initial and tooling costs mandate large production volumes exceeding 100,000+ units to ensure a compelling return on investment. For lower quantities, additive manufacturing methods like 3D printing make more economic sense.
While plastics possess impressive flexibility, chemical resistance, and electrical insulation properties suitable for intricate components, their mechanical performance falls short of machined aluminum or steel parts in critical load-bearing automotive and aerospace applications.
Lastly, despite exhibiting exemplary resource efficiency in production, widespread plastic recycling remains an elusive goal hindered by economic and technical obstacles.
Overall, a realistic appraisal of these plastic injection molding disadvantages facilitates technology selection and informs design tradeoffs when planning a new product launch.