Plastic injection molding is a complex manufacturing process with many variables. To produce high-quality parts, you need an accurate mold capable of churning out consistent pieces time and again. This is where flow analysis comes in.
Mold flow analysis simulates how molten plastic flows into the mold during the injection process. This predictive analysis uncovers potential defects and opportunities for optimization—before cutting any steel.
As a result, you can perfect the mold design, choose the ideal resin, optimize the runner system, and balance fill rates across cavities. This leads to faster cycle times, lower scrap rates, and a smooth ramp to full-scale production. As a professional plastic injection molding manufacturer, I will discuss everything about flow analysis for plastic injection molding in this post.
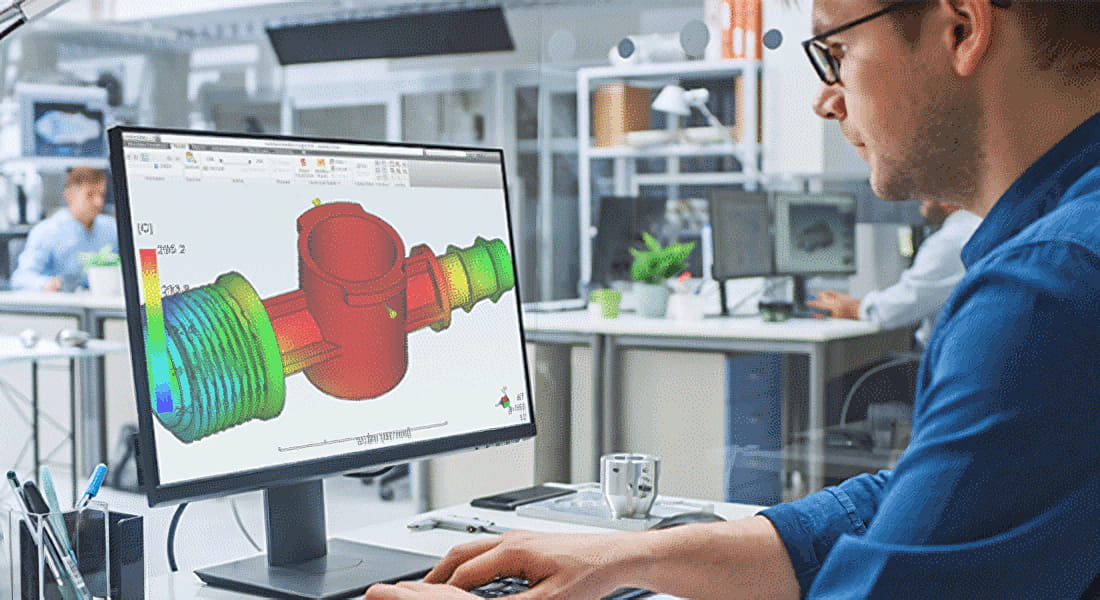
How Does Mold Flow Analysis Work?
Mold flow analysis software imports your CAD model and digitally replicates the injection molding process. Specialized FEA solvers simulate the flow of resin into the cooling mold, mapping variables like pressure, temperature, shear rate, fiber orientation, and more over space and time.
The software outputs color-coded visualizations highlighting potential issues like weld lines, air traps, hesitation, and short shots. By identifying problems ahead of time, engineers can tweak the design, material selection, process parameters, and tooling before ever machining a plate.
Here’s a general overview of benefits from simulation:
Optimize Part Design
FEED simulations accurately predict common defects like warpage, sink marks, and surface defects. By modifying problematic geometries early on, you can optimize the design for molded performance.
Analysis also checks wall thickness variations, detects overly aggressive draft angles, and validates insert details like threaded holes, text, and embosses. This reduces tool wear and post-molding operations.
Select The Best Material
With a database of 6000+ materials, analysis helps select the optimal resin and grade based on performance requirements and moldability. Trade-offs between ease of flow, shrinkage, and mechanical properties become clear.
You also gain visibility into glass fiber orientation for reinforced polymers. Orientation directly impacts strength and can be tuned with flow leaders and geometry tweaks.
Balance Filling Across Cavities
The filling simulation shows the precise flow front location at set time increments, identifying when each cavity fills. Results reveal hesitation, weld lines, and air traps for elimination.
Balancing runner systems and control layouts ensures simultaneous filling. This prevents overpacking and minimizes clamp force requirements.
Optimize Cooling Channels
Analysis provides temperature plots over the molding cycle, quantifying surface and internal heat buildup. Engineers then optimize cooling line placement and material to prevent hot spots and limit cycle times.
Validate Process Settings
Finally, analysis dial in optimal fill time, injection pressure, melt temperature and packing profiles. Automated Design of Experiments (DOE) features streamline optimization.
Top 6 Benefits Of Mold Flow Simulation
Beyond a general overview, here are six tangible benefits from making mold flow analysis a standard part of your injection molding process:
1. Cut Manufacturing Iterations
Physical prototypes carry significant cost and lead time. By simulating the molding process digitally, you circumvent rounds of trial-and-error tool tweaks down the line.
This reduces total development time by weeks or months. Flow analysis minimizes manufacturing cycles to get high-yielding, robust tools right the first time.
2. Slash Time To Market
Getting products to market faster provides a clear competitive advantage. Accelerating release schedules hinges on an efficient plastic part development process.
Mold flow analysis collapses the design → build → test cycle to ship reliable tools faster. Removing the guesswork prevents a prolonged cycle of build, mold, test parts, identify issues, repeat. This cascade effect lets you dramatically cut time to market.
3. Lower Production Costs
Scrap and rework kill profit margins. Tweaking tools and processes to reduce defects provides major cost savings per part, multiplying over volume production.
Flow analysis prevents many common and costly injection molding defects like short shots, flash, sink marks, and warpage. This leads to higher process capability and lower manufacturing costs.
4. Ensure High Yields
An injection mold that fails to consistently fill causes major headaches. If only a portion of the cavities fill on each cycle, you waste material, energy, and time purging bad parts.
Upfront analysis evens out fill rates across the tool, ensuring full cavities and maximizing production yield.
5. Gain Design Insights
Digital simulation provides unique visibility into the molding process impossible to access through experimentation alone. Watching flow fronts fill the cavities, tracking material temperature changes, and visualizing fiber orientation delivers valuable design insights.
Engineers use these enhanced insights to optimize drafting, gating, layouts, and material performance.
6. Evaluate Design Trade-Offs
Every design decision involves trade-offs. Changing the resin, tweaking a wall thickness, or modifying geometry entails multiple performance repercussions.
Simulation provides the data to evaluate associated trade-offs when altering the mold design, processing conditions, or material selection.
When Should You Run Mold Flow Analysis?
While possible to injection mold parts without upfront analysis, integrating simulation early in the development process is advised for:
- Multi-cavity molds
- Complex geometries
- Tight tolerance specifications
- New resin use
Basically, you want to simulate any project with high costs or uncertainty. Identifying potential defects ahead of time using mold flow analysis mitigates risk and saves significant time and money.
Takeaway
Mold flow analysis provides unique visibility into the injection molding process. Advanced simulation accurately predicts how resin will flow into complex molds, uncovering defects early and presenting opportunities to optimize.
This leads to reduced scrap, lower clamp requirements, balanced filling, robust tool design, and ultimately faster time to market. Rather than cutting steel and hoping for the best, simulation provides the data to engineer quality.
By integrating analysis upfront and validating part manufacturability digitally, you streamline development, slash costs, and accelerate release of robust injection molded products.