Injection molding involves heating plastic to a molten state and injecting it into a mold cavity under high pressure. The plastic then cools and solidifies into the desired shape. However, excessive heat during this process can cause the plastic to become brittle. So will plastic be brittle when too hot in injection molding? As a professional plastic injection molding manufacturer, I will help you find it out.
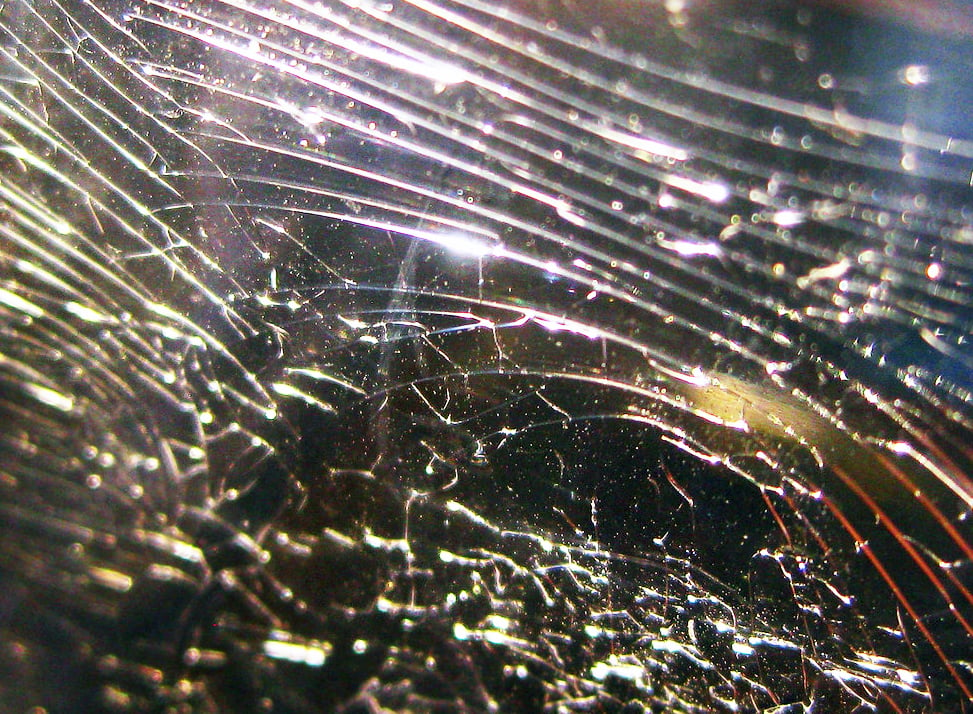
Will Plastic Be Brittle When Too Hot in Injection Molding?
Yes, plastic can become brittle if it’s too hot during injection molding. When plastic is heated to very high temperatures in the injection unit barrel, the polymer chains that make up the plastic material can break down. This process is known as thermal degradation.
As the molecular chains break apart, they become shorter. The end result is plastic that has a lower molecular weight. This lower molecular weight plastic solidifies into parts that are more brittle and prone to cracking under stress.
How Hot is Too Hot for Plastic in Injection Molding?
Every plastic material has an optimal melt temperature range for injection molding. Exceeding this range increases the likelihood of thermal degradation and eventual brittleness.
Most commodity resins like polypropylene, polyethylene, polystyrene and ABS plastics have a maximum melt temperature threshold around 230-250°C or 446-482°F. After this point, thermal decomposition accelerates rapidly.
Engineering resins like nylon, acetal, polycarbonate and some bioplastics often have higher melt temperature limits before the onset of material degradation. However, excessive barrel temperatures will still cause eventual thermal breakdown in these materials too.
Signs of Thermal Degradation in Plastic Parts
Here are some telltale signs that plastic parts may be becoming excessively brittle due to overheating during injection molding:
- Cracks or crazing forming on surface of parts
- Increased color variation
- Parts breaking when handled or during assembly
- Flaking plastic debris inside the injection molding machine
- Foul odor emanating from the plastic
In severe cases, the material can become so brittle that parts will crack immediately when ejected from the mold. Plastic that is thermally degraded to this extent will be unusable.
How to Prevent Plastic Part Brittleness
Here are some tips for avoiding excessively high temperatures that can cause material degradation and brittle plastic parts in injection molding:
- Carefully follow plastic supplier recommendations for optimal melt/mold temperatures
- Use barrel temperature controllers and gauges to precisely manage heat input
- Install shutoff safety devices to prevent dangerous overheating
- Upgrade to all-electric injection molding machines for more temperature precision
- Use general purpose screw design first before specializing for higher outputs
- Avoid restricted gates and runners that can overheat the plastic
- Upgrade to a larger machine to minimize risky long residence times
- Closely inspect plastic resin supply for signs of degradation
Factors that Cause Brittle Plastic Parts
While overly high temperatures are the main culprit, several other variables during injection molding can also result in brittle parts:
Excessive Shear Heating
Similar to excessive barrel heat, too much shear heating inside the injection cylinder can potentially degrade the plastic. Using very fast screw speeds or excessive back pressure creates mechanical heat from the intense shearing forces.
Prolonged Exposure Time
The longer plastic remains in a molten state inside the injection barrel, the more likely some thermal degradation will occur. This residence time needs to be minimized. Potential fixes include increasing injection speed, reducing shot size or selecting a smaller machine.
Reusing Degraded Regrind Material
Regrinding sprues and runners to reuse as raw material saves on costs. However, this regrind contains plastic that has already experienced some thermal stress. After several passes through the injection molder, the recycled plastic can have severely reduced strength and ductility.
Inadequate Drying
Many plastics are hygroscopic, meaning they absorb ambient moisture. Water vapor causes hydrolysis degradation when exposed to high heat in the barrel, resulting in brittle parts. Follow material supplier guidelines for proper drying methods and parameters.
Contamination from Other Materials
If previously molded engineering resins remain inside the barrel, they can leach out and contaminate lower temperature commodity resins like PP and HDPE during subsequent runs. Traces of higher temperature plastics can degrade the cheaper resins.
Color and Filler Concentration
While additives like colorants and fillers enhance aesthetics and properties, high loading levels increase melt viscosity. This demands more shear heating to fully plasticize the material, increasing the potential for thermal degradation.
Preventing Brittle Parts Through Robust Process Monitoring
Brittle parts indicate that something went awry during the injection molding process. Often small changes accumulate overruns to push the plastic over its thermal degradation limit. Robust monitoring and control allows processors to detect issues before complete failures occur:
- Track melt/mold temperature with data loggers
- Benchmark cycle analysis with scientific molding
- Monitor shear heating with dual zone barrel controllers
- Inspect molded parts frequently for visual cues
- Implement formal preventative maintenance schedules
- Monitor machine function for any deviations
- Analyze rejected part root causes for corrections
Careful and consistent injection molding processes keep temperatures and shear heating within defined parameters for each plastic resin. This minimizes the potential for the excessive heat exposure that can lead to brittle parts over time.
So in summary, plastic will become brittle when exposed to overly high temperatures during injection molding. Thermal monitoring, precise process control and vigilant machine maintenance are key to preventing brittle plastic parts.
In Summary
Plastic can become brittle when overheated during the injection molding process. Maintaining optimal temperatures as specified by the material manufacturer is crucial to prevent material degradation that leads to eventual brittleness and cracking. Precise process monitoring and control allows processors to identify issues quickly before defective parts are produced. With proper protocols in place, brittle parts can be avoided despite the high heat required for injection molding.