Plastic injection molding is one of the most common and versatile manufacturing processes used today. From toys and household goods to medical devices and car parts, injection molded plastic components are everywhere.
Given how ubiquitous and useful injection molding is for plastics, it’s natural to wonder – is there an equivalent process for metal parts? As it turns out, there is one metal casting process that works very similarly to plastic injection molding: die casting.
In this post, as a professional plastic injection molding manufacturer, we’ll take an in-depth look at how die casting stacks up against injection molding to see why it can be considered the metal version of this popular manufacturing technique.
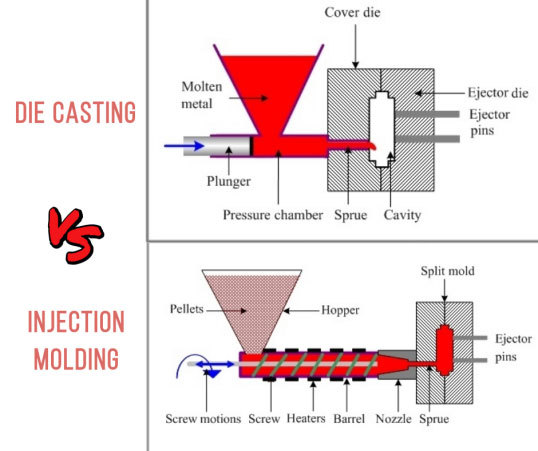
Which Metal Casting Process is Most Like Plastic Injection Molding?
The metal casting process that works most similarly to plastic injection molding is die casting. Die casting injects molten metal alloy into steel molds under high pressure, allowing complex, high tolerance metal parts to be mass produced. This mirrors several key stages and capabilities of the injection molding process, qualifying die casting as the closest metal equivalent.
How Plastic Injection Molding Works
Before we can properly compare it to die casting, let’s quickly review how conventional injection molding works. Here is the standard injection molding process:
The plastic raw material is melted inside the injection molding machine barrel. Common plastics used include ABS, PVC, nylon, HDPE, and polycarbonate. The plastic is melted by heat and pressure from a rotating screw.
The now liquid plastic gets injected into a steel mold. The mold is clamped shut and has been lubricated and cooled by water lines. The plastic fills the cavity, taking the shape of the mold.
The molded part cools inside the mold until rigid enough to be ejected. Cooling times depend on the plastic used and wall thickness but typically range from 20 seconds to 2 minutes.
The mold opens, and the completed plastic part gets ejected. Some minor trimming of the parts is required to remove excess plastic and mold lines.
This quick 4 stage process allows intricate plastic parts to be mass produced with precision, efficiency, and repeatability. But is there a metal equivalent?
How Die Casting Compares to Injection Molding
Die casting is a manufacturing process where a molten metal gets injected under high pressure into a steel mold, called a die. The most commonly die cast metals are non-ferrous alloys of zinc, aluminum, magnesium, and copper.
This may already sound very similar to plastic injection molding, but let’s look closer at each key stage:
Mold Preparation
This step is nearly identical between the two processes. The metal dies or steel injection molds get sprayed with a lubricant and then clamped shut. This aids with temperature control and part ejection.
Filling the Mold
Here is where we start to see the similarities shine through. With die casting, a molten metal gets injected into the die mold through a gooseneck. The pressure, temperature, and speed are carefully controlled to fill the die cavity.
Just like injection molding, thin, complex, high tolerance metal parts can be created via the high pressure die casting process.
Cooling and Solidification
After the mold fills, the molten metal starts to rapidly cool and solidify, taking the shape of the metal die. Cooling times depend on the alloy used and wall thickness but are typically faster than plastic injection molding.
Part Ejection
Finally, the die separates, and the solidified metal part gets ejected. Some minor trimming is also performed to remove excess metal and flash.
As you can see from this comparison, die casting works remarkably similar to plastic injection molding, just with molten metal instead of plastic. This qualifies it as the most equivalent metal fabrication process.
Unique Benefits of Die Casting
Beyond just process similarities, die casting provides some unique advantages, much like injection molding does for plastics:
- Ability to produce complex, high tolerance metal parts at mass scale
- Very fast production cycle times
- Low per unit cost at higher volumes
- Wide material selection of castable alloys
- High degree of automation possible
These beneficial characteristics have made die casting the process of choice for metal part production across many industries, including automotive, aerospace, electronics, and consumer products.
Die casting is able to create durable metal components with tighter dimensional accuracies versus other metal fabrication techniques. This allows small but intricate metal parts to be manufactured at scale, much like injection molding does with plastics.
Key Differences Between Die Casting and Injection Molding
While the die casting process shares many commonalities with plastic injection molding, there are some notable differences as well:
Materials Used: The core difference is that injection molding uses plastic polymers, while die casting works exclusively with molten metal alloys. Each process is tailored for its respective material type.
Mold Cost: Due to high temperatures and pressures, die casting molds are more complex and expensive than plastic injection molds. However, they also tend to last for over 1 million shots.
Post-Processing: Die cast parts require little finishing since they eject with smooth surfaces. Injection molded plastics usually need some degating, texturing, or decorating secondary operations.
Lead Time: Die casting generally has faster cycle times than injection molding, especially for small, thin-walled parts. But plastic injection prototyping is easier with lower-cost aluminum molds.
So in summary, the two main differences come down to materials used and mold complexity/cost. The actual formation process is otherwise quite similar.
Which Process is Right For Your Application?
We’ve covered a lot of ground comparing die casting with plastic injection molding. Let’s recap the key learnings:
- Die casting works similarly to injection molding but with molten metal instead of plastic polymers
- Both can produce complex, high tolerance parts at mass production volumes
- Die casting offers unique benefits like strength, heat resistance and faster cycles
- Plastic injection molding provides lower costs and material flexibility
So which one makes sense for your specific product or application?
Here are some guidelines:
Plastic Injection Molding tends to work better if you need:
- Low per unit costs, especially in very high volumes
- Lightweight parts with corrosion resistance
- Low startup and prototyping costs
- Creative freedom with colors, textures, and materials
Die Casting tends to work better if you require:
- High-strength and heat/abrasion-resistant metal parts
- Intricate components with very tight tolerances
- Smoother surfaces that don’t need post-processing
- Fast production cycle times
For some applications, both or even a combination might make sense. But assessing your specific requirements and priorities will provide direction on selecting the best process.
The versatility of plastic injection molding has made it the manufacturing method of choice for mass production of plastic parts across endless industries. And die casting delivers that same capability, efficiency, and precision but for affordable metal components.
So if you’ve ever wondered about or had need for a metal fabrication process offering injection molding-like benefits, then look no further than die casting – the closest thing to a metal version of this ubiquitous production technique.