Selecting the optimal plastic material is one of the most critical decisions in injection molding. The material greatly impacts the molding process, cost, product performance, and application suitability. With over 85,000 grades of polymers available, navigating the options can be overwhelming.
As a professional plastic injection molding manufacturer, I often get asked, “How do I choose the right plastic material for my product?” Here’s my in-depth guide for selection criteria, popular resins, evaluating properties, and avoiding common mistakes.
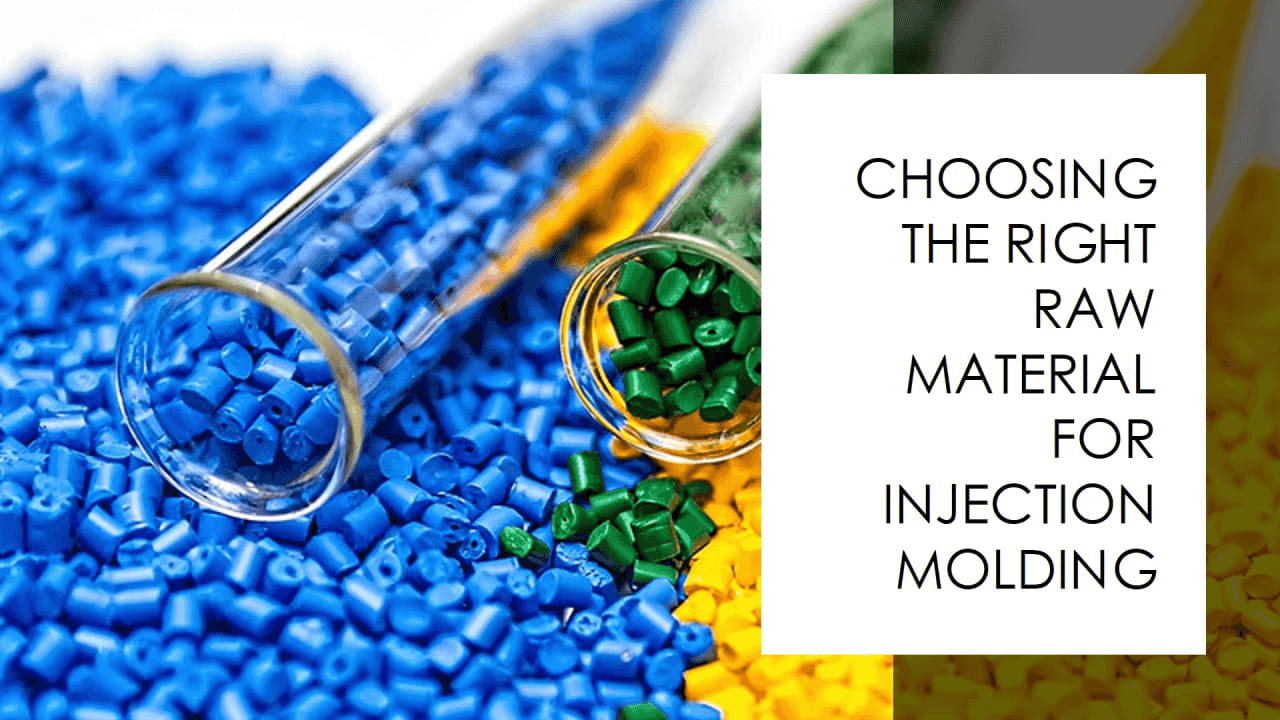
Why Material Selection Matters in Injection Molding
The plastic material influences nearly every facet of injection molding, including:
End Product Functionality
The resin affects strength, durability, aesthetics, weight, and other product traits. Using the wrong material can severely impact functionality or cause complete failure. You must match the polymer’s natural properties to your product’s requirements.
For example, a flexible material won’t work for load-bearing automotive parts needing rigidity. And a plastic with poor heat resistance isn’t suitable for electrical enclosures with internal heat sources.
Manufacturability
Different plastics have varying melt flow rates, viscosities, melting points, and cooling characteristics. This significantly impacts mold filling, ease of processing, cycle times, dimensional accuracy, and part quality.
Complex geometries often require high-flow materials that easily fill intricate cavities. Engineering thermoplastics like PEEK have higher processing demands compared to commodity resins.
The optimal material balances performance with process-ability at the lowest feasible cost. Poor material choice will translate into production issues down the line.
How to Choose the Right Plastic Material for Injection Molding
Step 1: Define End-Product Requirements
I always start the material selection process by clearly defining customer needs and critical product specifications. This prevents getting swayed by irrelevant material properties later on.
Start by asking questions like:
- What’s the part function and operating environment?
- What mechanical, thermal, chemical, or electrical loads will it undergo?
- What regulations apply (FDA, UL, RoHS, etc.)?
- Does it need strength, rigidity, impact resistance?
- What cosmetic properties are required?
- Does it need an exact color match? Textured finish? Paintability?
- What’s the target lifecycle and warranty period?
Document the end-product requirements into a specification sheet. Critical needs become your primary decision drivers for screening candidate materials while “nice-to-haves” serve as potential tiebreakers between equal contenders.
Step 2: Research Candidate Resins
With your product requirements defined, start researching thermoplastic resins matching your criteria.
Popular Materials for Injection Molding
Here are the most common mainstream options:
1. ABS: scratch-resistant thermoplastic with high impact strength and dimensional stability. UV-sensitive. Used in automotive trim, household appliances, toys.
2. Acrylic: Optically clear, glass-like polymer. Scratch/shatter resistant alternative to glass or polycarbonate. Used in lighting, displays, lenses.
3. Nylon: durable engineering thermoplastic with high strength-to-weight ratio and natural lubricity. Resists fuels, grease, chemicals. Used in gears, bushings, bearings.
4. Polycarbonate: Extremely impact-resistant but not scratch-resistant. Clear grades used for bulletproof glass. Leveraged across safety equipment, signage, optics.
5. Polyethylene (PE): moisture-resistant commodity resin available in various densities. LDPE and HDPE used for bottles, containers, pipes, housewares, toys.
6. Polypropylene (PP): resistant to acids/bases. Versatile, economical material for packaging, appliances, automotive parts, ropes, clothing.
Specialty Resins
For extreme conditions, investigate high-performance materials like:
- Ultem (PEI): exceptional heat/chemical resistance
- Torlon (PAI): resistance to 600°F temps & acids
- PEEK (Polyetheretherketone): for aggressive chemical environments
Google search trends for “what plastic to use” to uncover other niche resins relevant to your product. Then assess how their natural properties align with your requirements.
Step 3: Evaluate Key Material Properties
With a shortlist of candidate plastics, scrutinize their properties in detail:
Mechanical Properties
- Hardness describes a plastic’s resistance to indentation. Hard materials don’t scratch/deform easily. Assess hardness via Shore or Rockwell scales.
- Strength defines how much load a plastic withstands before permanent deformation. Key measures: tensile, flexural, compressive strengths.
- Stiffness is resistance to elastic deformation under load. Use flexural modulus. Stiffer ≠ Harder.
- Toughness represents total impact energy absorbed before failure. Assess via Izod/Charpy impact tests.
Thermal Properties
- Brittleness Temperature: Low ductility point where material transitions from tough to brittle.
- Glass Transition Temperature (Tg): Softening point of amorphous plastics signaling flexural modulus changes
- Melting Temperature (Tm): Temperature for melt phase transition in semi-crystalline plastics
- Heat Deflection Temperature: Maximum service temp before severe deformation risk
Electrical Properties
- Dielectric Strength: how well a plastic resists electrical breakdown under high-voltage spikes
- Dielectric Constant: Material’s inherent capacitance and energy storage ability
- Dissipation Factor: How efficiently a material dissipates stored charge
- Volume Resistivity: Electrical leakage through thickness of material
Compare datasheets to confirm the plastic meets all critical performance thresholds across expected temperature ranges.
Step 4: Evaluate Cost, Processability & Sustainability
With technically viable materials selected, assess economic and qualitative factors:
Raw Material Cost: How much does the base resin cost per pound? Will market fluctuations affect pricing sustainability?
Manufacturability: Will the plastic easily fill intricate geometries? Does it require drying beforehand? What molding pressures are needed? How long are cycle times?
Sustainability: Determine end-of-life recyclability, reuse potential, and biodegradability ratings.
Review the best polymers holistically weighing all decision criteria. An expensive yet easily moldable and eco-friendly resin can still be financially prudent long term versus a cheaper alternative.
Common Mistakes & Things to Avoid
While choosing plastics for injection molding, steer clear of these mishaps:
- Selecting solely based on cost, disregarding technical viability
- Inadequate vetting for regulatory compliance (RoHS, REACH, etc.)
- Choosing opaque resins for transparent optical parts
- Assuming all flexible resins have high impact strength
- Disregarding annealing, drying, or mold release requirements
- Insufficient testing across full operating temperature spans
By carefully evaluating critical parameters and avoiding these errors, you’ll select a material delivering reliable performance across your product’s expected lifecycle.
Still Unsure? Work With a Specialist
This guide covers the essential factors for picking an optimal thermoplastic resin for injection molding. But with thousands of material grades available, the options can still be confusing.
If you’re struggling to settle on a plastic, consider partnering with an experienced injection molder or resin distributor early in the product development phase. Their deep material expertise can suggest the ideal thermoplastic matching your specifications along with viable alternatives.
With a thorough selection process evaluating mechanical properties, thermal characteristics, cost, manufacturability and sustainability, you’ll choose a resin ensuring injection molding success and product longevity.
In Summary
Finding the optimal plastic for your injection molded parts is critical yet challenging. This guide outlined proven methods for screening materials efficiently.
By clearly defining product requirements upfront and weighing key performance characteristics, manufacturability, and sustainability, you’ll select an ideal material for molding and long-term reliability. Consider consulting a specialist if still undecided – the right plastic ensures your product withstands its intended operating conditions over the full lifecycle.