Injection molding plastic parts with extremely thin walls can be very challenging. But with careful planning and the right techniques, it is possible to injection mold plastic with walls thinner than 1mm.
In this complete guide, as a professional plastic injection molding manufacturer, I will share everything you need to know about thin wall injection molding, including:
- What is considered “thin wall” in injection molding?
- How thin can you injection mold plastic?
- What is the minimum injection molding wall thickness for different plastics?
- Design considerations and best practices
- Pro tips for getting the thinnest possible walls
So if you want to push the limits of injection molding part wall thickness, you’ll find this guide invaluable.
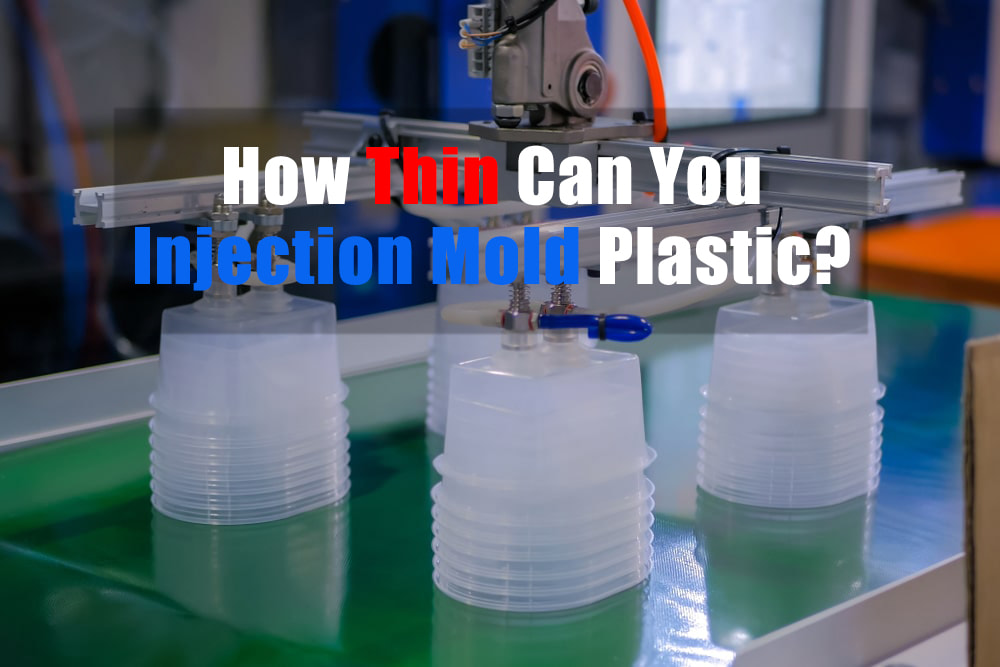
What is Considered “Thin Wall” Injection Molding?
Generally speaking, thin wall injection molding refers to manufacturing plastic parts with walls significantly thinner than traditional injection molded components.
But there is no universally accepted threshold for what qualifies as “thin wall”. Some consider parts with walls as thick as 2mm (0.08 inches) to fall into the thin wall category.
However, more typically, thin wall injection molding involves walls less than 1mm (0.04 inches) thick. And parts under 0.5mm are considered “ultra” thin wall.
So in summary:
- 2mm: Standard wall thickness
- 1 – 2mm: Thin wall
- < 1mm: Ultra thin wall
Now let’s look at the minimum wall thickness you can achieve with different plastic resins.
How Thin Can You Injection Mold Plastic?
The minimum thickness for injection molded plastic parts depends on the material, part requirements, and other factors. In general, the minimum wall thickness for thermoplastic parts is between 0.6–0.9 mm, and the recommended range is 1–4 mm. However, the minimum thickness can vary depending on the material.
Minimum Injection Molding Wall Thickness by Plastic
The minimum injection molding wall thickness depends heavily on the plastic you use.
High flow polymers like polypropylene and ABS lend themselves well to thin walls thanks to excellent melt flow properties.
But materials like PEEK and polycarbonate can be more temperamental.
Here’s a breakdown of minimum wall thickness by plastic:
Polypropylene (PP)
- Minimum wall thickness: 0.5mm
- Recommended wall thickness: 1 – 1.5mm
Thanks to its outstanding flow characteristics, polypropylene injection molding can achieve incredibly thin walls down to 0.5mm.
Just keep in mind that PP has low stiffness. So you need uniform wall thickness and proper rib placement to prevent warping or sinking.
Acrylonitrile Butadiene Styrene (ABS)
- Minimum wall thickness: 0.7mm
- Recommended wall thickness: 1 – 1.5mm
ABS flows very well too, allowing thin wall injection molding down to about 0.7mm. It also offers good strength and is easy to produce.
Nylon
- Minimum wall thickness: 0.7mm
- Recommended wall thickness: 1 – 1.5mm
Nylon resins enable thin wall injection molding of small, complex geometries. But you need proper cooling and venting to prevent defects.
Glass filled nylon can be very temperamental. So you’ll probably need to stay above 1mm with glass fiber content above 20-30%.
Polycarbonate (PC)
- Minimum wall thickness: 0.7mm
- Recommended wall thickness: 1 – 2mm
Thanks to its high viscosity, polycarbonate can be difficult to injection mold with thin walls under 1mm. But with a robust mold and proper process control, 0.7mm is achievable.
Polystyrene (PS)
- Minimum wall thickness: 0.7mm
- Recommended wall thickness: 1 – 2mm
General purpose PS grades allow thin wall molding down to about 0.7mm. But you may need to use high fluidity PS developed specifically for thin walls to go under 1mm.
Polyether Ether Ketone (PEEK)
- Minimum wall thickness: 1mm
- Recommended wall thickness: 1.5 – 4mm
PEEK’s extremely high melt viscosity makes it essentially impossible to injection mold with walls under 1mm. Parts over 2mm also tend to warp and sink. So ideal PEEK wall thickness is 1.5 – 2mm.
Liquid Crystal Polymer (LCP)
- Minimum wall thickness: 0.3mm
- Recommended wall thickness: 0.5 – 1.5mm
Thanks to outstanding flow properties, LCP is arguably the best plastic for thin wall injection molding. It can easily achieve sub 0.5mm walls with proper mold temperature control.
Polyethylene (PE)
- Minimum wall thickness: 0.8mm
- Recommended wall thickness: 1 – 1.5mm
The relatively high viscosity of polyethylene makes it difficult to injection mold walls under 0.8mm consistently. But thanks to excellent chemical resistance, PE sees widespread use in thin walled syringes, pipettes, and microtubes.
Design Considerations for Thin Wall Injection Molding
When designing parts for thin wall injection molding, you need to account for the unique manufacturing considerations.
Here are some key design guidelines:
Maintain Consistent Wall Thickness
Your number one priority should be to keep wall thickness as consistent as possible throughout the component.
Sudden changes in wall thickness lead to uneven cooling. Which causes cosmetic defects like sink marks, voids, and warpage.
It also creates internal stresses in the material, which can cause cracking or breakage in finished parts.
So you want gradual transitions between thinner and thicker sections.
The recommended tolerance is around 25%. So if one section has a 2mm wall, adjacent sections should keep thickness between 1.5mm and 2.5mm.
Add Ribs for Structural Support
One technique to allow thinner walls without sacrificing strength is adding ribs.
Ribs enable you eliminate thick sections while providing essential support to prevent warping or sinking.
Good rule of thumb is to keep rib height less than 50-60% of the wall thickness they intersect.
Gate Placement is Critical
Gate placement plays an integral role in thin wall molding to minimize cosmetic defects.
Poor gate positioning often creates weak weld lines where the plastic fronts meet after ejection. Which leads to cracks and structural defects.
So you want to orient gates to promote uniform filling without creating weld lines.
Edge gates and hot runner systems help reduce gate marks on visible surfaces. But they can still create knit lines in complex geometries.
Include Draft Angles
Draft angles allow you to cleanly eject parts from injection molds without damaging fine features or thin walls.
General recommendation is at least 0.5 degrees of draft per side. But you may need up to 5 degrees for detailed textures.
Keep draft angles consistent across the entire part geometry to minimize residual stress that causes curling or distortion.
Pro Tips for Maximizing Thin Wall Capabilities
If you want to push the limits of wall thickness when injection molding, here are some pro tips:
Select an Experienced Manufacturer
Thin wall molding requires incredible precision and tight process control. So partnering with an experienced manufacturer is non-negotiable.
Ask potential vendors about their experience with thin wall parts in the past. Having successfully produced components with walls close to your target thickness in the resin you plan to use is a must.
Get Mold Flow Simulation
While physical prototypes are always recommended, mold flow simulation gives you tremendous early insights into fill time, weld lines, air traps, and sink mark risks.
Adjusting the CAD model early based on simulation findings enables faster design finalization without costly physical sampling.
Use High Fluidity Resins
Injection molding resins specifically engineered for thin wall applications can make a huge impact.
For example, high fluidity polypropylene offers 2-4X easier flow than standard grades. Allowing you to fill intricate geometries and achieve thinner walls.
You can also reduce wall thickness by increasing injection pressure. But high fluidity resins get you better results without compromising part quality or cycle time efficiency.
Tweak Process Temperatures
Boosting mold and melt temperatures enhances resin flow for challenging thin wall designs. But you need to strike the perfect balance between viscosity and cooling time.
Starting 5-10°C above the resin recommendation and fine tuning from there is a good starting point. Just watch out for long term thermal degradation above 340-350°C for most plastics.
Wrapping Up
I hope this guide gave you a solid overview of the capabilities – and limitations – around injection molding thin plastic walls.
While thin wall molding presents unique obstacles, choosing the right manufacturing partner and resin while optimizing your design can allow walls under 0.5mm and even 0.3mm in some cases.