Overmolding is a popular injection molding process that combines multiple materials into a single part. This advanced manufacturing technique produces custom components with enhanced durability, functionality and aesthetics.
In this comprehensive guide, as a professional plastic injection molding manufacturer, we’ll cover everything you need to know about overmolding, including:
- What is overmolding and how does it work?
- The benefits of overmolding
- Overmolding techniques
- Overmolding applications
- Overmolding materials
- Overmolding design considerations
- Prototyping overmolded parts
After reading, you’ll understand the overmolding process from start to finish and be able to determine if it’s suitable for your product. Let’s get started!
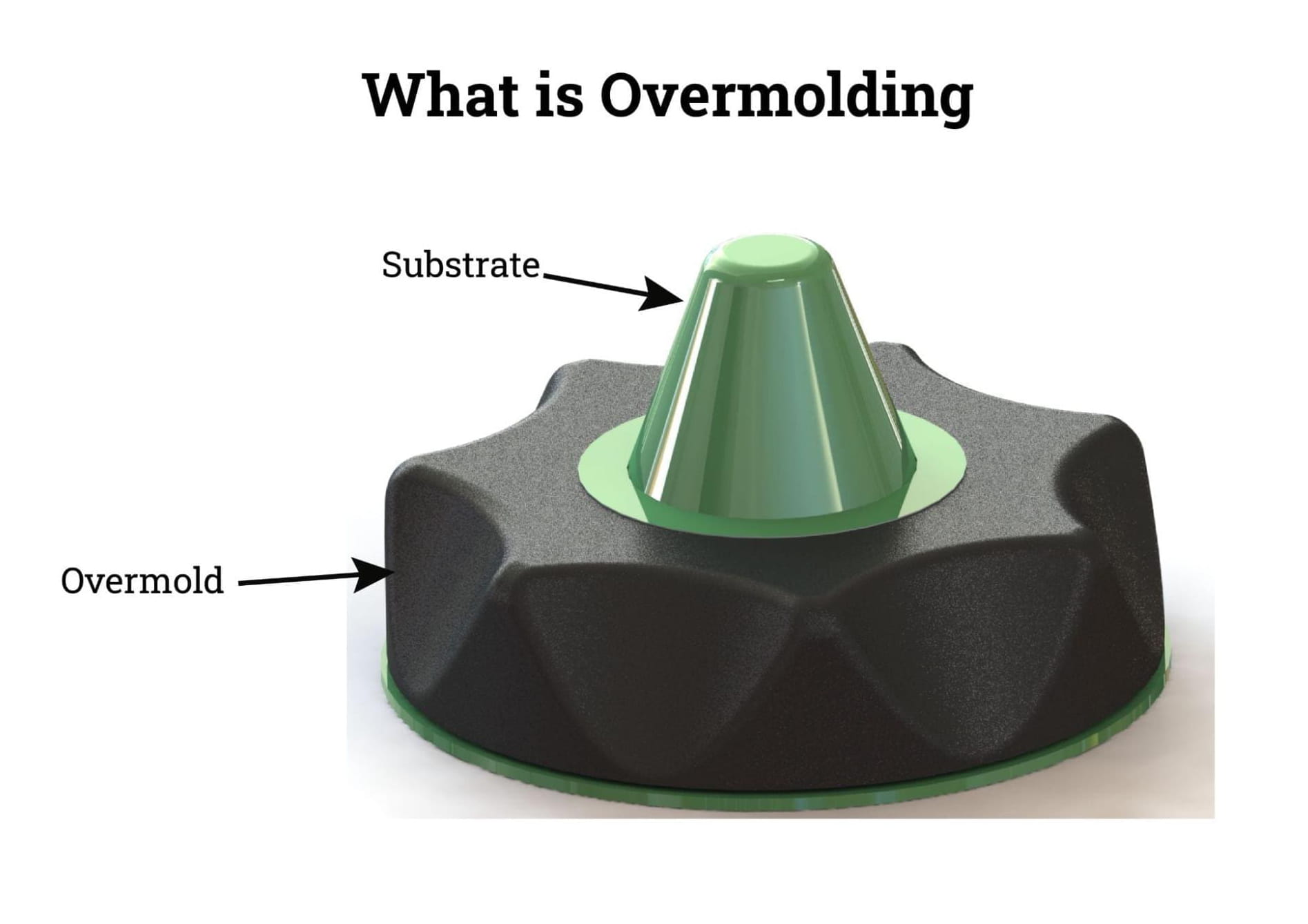
What Is Overmolding?
Overmolding, sometimes called two-shot molding or 2k molding, combines two materials into one injection molded part using a single tool. It produces custom plastic parts with a rigid plastic substrate and a pliable exterior layer, typically made of TPE (thermoplastic elastomers) or silicone.
The overmolding process has two stages:
- The primary shot forms the main body of the part, called the substrate. The material used is usually a rigid plastic like ABS, PC, nylon, or PBT.
- The secondary shot creates the exterior layer that’s molded over and bonded to the substrate. This is commonly TPE or silicone which gives a soft, tactile finish.
So in summary, overmolding allows manufacturers to produce multi-material components in a streamlined, automated process. This eliminates the need for secondary assembly and finishing operations.
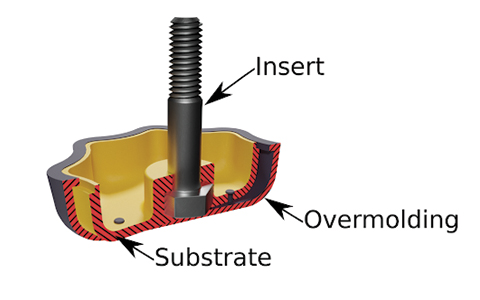
Now let’s look at why overmolding is so popular.
Key Benefits Of Overmolding
There are several reasons companies choose to overmold parts rather than manufacture them separately:
Improved product performance – Combining materials produces components with enhanced physical properties and environmental resistance. Overmolded grips improve comfort and safety. Soft seals prevent water ingress. The uses are wide-ranging across industries.
Increased production efficiency – Overmolding consolidates plastic part production and finishing into a single automated process. No gluing or assembly of different components required.
Cost savings – The ability to streamline manufacturing lowers per-unit costs. And reduced assembly lowers labor expenses.
Greater creative freedom – Using multiple durometers and colors of material in one product provides more aesthestic options. Branding can also be integrated into the part.
Shorter time-to-market – Getting functional prototypes made quickly allows products to launch faster. And overmolded parts enable accelerated large-scale production.
Now we’ve covered the basics of overmolding, let’s look at the most common techniques used.
Overmolding Techniques
There are two primary overmolding methods used in manufacturing:
Two-Shot Injection Molding
As the name suggests, two-shot molding uses specialized injection molding machines with two barrels and injection units. This allows two different plastic materials to be processed using one mold.
First, the primary material (substrate) is injected and partially cured. Next, the mold rotates 180-degrees and the secondary material (overmold) is injected directly onto the substrate.
Using one mold makes this process suitable for larger production runs – typically over 10,000+ parts. It produces components with excellent bond strength between the two materials.
However, two-shot tooling is complex. Changing or adding shut-offs to seal different areas can be an expensive and time-consuming mold modification.
Insert Molding
With insert molding, the substrate is molded using a standard injection press. After ejection, the parts are transferred to a secondary station where the overmold material gets injected. This uses a separate mold tool with larger cavity dimensions to create space for the exterior layer.
Using two simpler molds makes insert molding ideal for prototyping and lower volume production typically under 10,000 parts.
The only downside is that handlings the cooled substrate can reduce bond strength. Careful material selection and molding process controls are required to maximize adhesion.
Now we understand the two main overmolding processes, let’s see some of the many product applications.
Popular Overmolding Applications
Overmolded components feature across numerous industries as manufacturers seek improved part integration.
Some of the most common applications include:
Sporting equipment – Overmolded grips on golf clubs, tennis rackets and bicycle handlebars enhance user comfort and safety. The tactile exterior layer provides a positive grip, especially with sweaty hands.
Power tools – A similar story here. Power drills and electric screwdrivers perform better and minimize hand slippage thanks to overmolded casings and handles.
Kitchenware – Food preparation knives, spatulas and whisks all utilize TPE or silicone overmolds. As do vacuum handles, tongs and jar openers. The soft-touch layer makes gripping easier with wet hands.
Medical devices – Overmolding excels for handheld surgical instruments like forceps and clamps. The ergonomic shapes maximize control while soft exteriors prevent tissue damage.
Consumer electronics – Smartphones, games controllers, and computer peripherals often feature overmolded housing and buttons. This impervious soft-touch exterior protects internal components from liquid damage.
And those are just a few examples of overmolding applications across different products.
Next, let’s discuss suitable materials for overmolding.
Overmolding Material Options
Selecting compatible materials for overmolding is essential to produce durable components. The materials must bond together effectively without separating over time.
Here’s an overview of common options:
Rigid Substrate Materials
The base material for overmolding needs high heat tolerance and dimensional stability. Typical rigid plastics used include:
- PC/ABS – Great strength-to-weight balance
- ABS – Affordable and versatile
- PC – Superior impact and heat resistance
- Nylon (PA) – Excellent chemical resistance
- PBT – Durable with low moisture absorption
- LCP – High stiffness and heat resistance
These ensure the substrate withstands the secondary molding process without deforming.
Overmold Materials
The overmold layer provides the ergonomic exterior and pleasurable aesthetics.
Thermoplastic elastomers (TPE) offer an excellent balance of flexibility, durability and cost-effectiveness. Silicones give superior heat resistance and compression set. Overmold materials include:
- TPE – Affordable with diverse grades
- TPU – Outstanding abrasion and tear resistance
- TPV – Combines TPE with higher rigidity
- Silicone – Extreme temperature tolerance
- LSR (Liquid Silicone Rubber) – Softer but less overmold-friendly
Choosing compatible substrate/overmold pairings ensures proper bonding during molding. Material suppliers can advise about adhesion performance between specific plastic grades.
Now let’s examine vital overmolding design factors.
Critical Overmolding Design Considerations
Several part design aspects directly impact overmolding outcomes regarding quality, scrap rates and overall manufacturability.
Here are the most crucial considerations:
Draft Angles
Sufficient draft on vertical surfaces enables trouble-free ejection after molding flexible overmold materials. Typical draft requirements are:
- Substrate – Standard 1° draft
- Overmold – Minimum 3° draft
Generous draft also facilitates faster cycle times and lower injection pressures.
Wall Thickness
Uneven wall stock can lead to sink marks, voids, and weak points around an overmolded component. Consistent wall thickness enables proper cooling and optimized material flow.
Recommended overmolding wall thickness:
- Substrate – 2 mm to 4 mm range
- Overmold – Minimum 1.5 mm
Thicker overmold walls do allow greater material flexibility in localized areas.
Shut-Offs
Shut-offs (or witness marks) create a hard stop and seal flow between materials. This prevents overflow flash artefacts around the finished parts.
Crisp, cosmetically appealing shut-offs require a 0.5 mm to 1 mm substrate lip height to lock the flowing plastic.
Gate Location
Gate position influences cycle efficiency and bond strength. Central gates balance flow fronts while direct gates maximize adhesion.
Gate style also affects appearance:
- Edge gates – Good for hiding gate blush
- Submarine (tunnel) gates – Prevent jetting
- Film gates – Thin gates reduce vestige marks
Gates should never obstruct overmold coverage areas.
By considering these vital factors early in the design phase, engineers can optimize parts for manufacturability and performance.
Now we understand key overmolding principles, let’s see how prototyping enables accelerate project success.
Prototyping Overmolded Parts
Validating part design, ergonomics and manufacturability early using prototypes is invaluable before committing to production tooling.
Overmolded prototypes help confirm:
- Design functionality
- Material suitability
- Production methods
- Cycle efficiencies
Rapid tooling techniques like 3D printing molds is ideal for low volume overmolding prototypes. Quick tool turnaround coupled with realistic parts enables comprehensive concept verification.
During prototyping, overmolding experts also analyze critical success factors:
- Injection pressures
- Material viscosity
- Mold temperature
- Bonding performance
Refined process parameters help ensure a smooth production ramp-up.
So in summary, overmolded prototypes accelerate perfecting part designs while minimizing project risk and decisions errors.
Overmolding Delivers Multi-Material Component Integration
We’ve covered all the key overmolding basics:
- What overmolding is
- The benefits overmolding provides
- Popular applications
- Overmolding techniques
- Material selections
- Vital design considerations
- Prototype best practices
While initially complex, mastering overmolding processes gives product designers extensive creative possibilities. Pairing complementary materials into integrated components creates next-generation products with enhanced user experiences.
So if you’re exploring overmolding for the first time or refreshing existing projects, leverage specialist engineering support. BaiweMolding offers on-demand manufacturing guidance to transform product visions into reality.