Mold temperature is one of the most critical parameters in injection molding that determines the quality, appearance, and dimensions of molded plastic parts. However, its role is often overlooked by many manufacturers.
In this comprehensive guide, as a professional injection molding manufacturer, I’ll explain what exactly mold temperature is, why controlling it properly matters, how it impacts injection molding, and share actionable tips on setting optimal mold temperatures for different plastics.
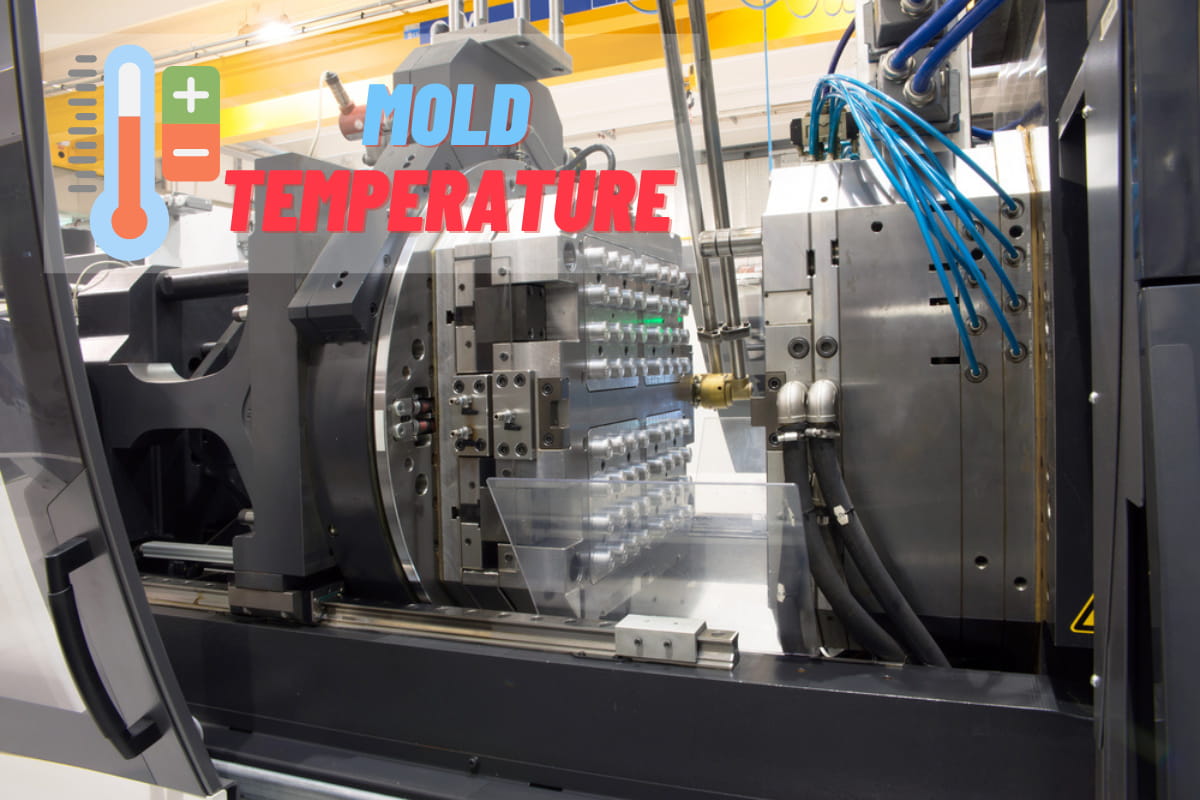
What is Mold Temperature in Injection Molding?
Mold temperature refers to the surface temperature of the mold cavity during the injection molding process.
In simpler words, it’s the temperature of the mold’s inner surface that makes direct contact with the molten plastic material as it gets injected into the mold.
The mold temperature depends on several factors like the:
- Type of plastic (PP, ABS, nylon).
- Wall thickness of the part.
- Complexity of the mold design.
And it needs to be precisely controlled through external heating/cooling to ensure proper filling, cooling, and part ejection.
Now that you know what mold temperature means, let’s look at why maintaining it is crucial.
Why Controlling Mold Temperature is Vital
There are two key reasons why optimizing mold temperature is essential:
1. Determines Final Part Quality
The mold surface temperature directly influences the cooling rate of the molten plastic inside the mold.
- Higher temperature = Slower cooling
- Lower temperature = Faster cooling
Faster cooling can lead to problems like sinks, warpage, and undesirable molecular orientation in the final part.
Slower cooling gives the material enough time to uniformly shrink and crystallize. This results in smoother surfaces, fewer defects, and optimal mechanical properties.
2. Impacts Cycle Time & Productivity
The majority of the injection molding cycle time is taken up by cooling – allowing the molten plastic to solidify.
Higher mold temperatures lengthen the cooling phase, increasing cycle times.
Lower mold temperatures speed up solidification, reducing cycle times significantly.
Since productivity is inversely related to cycle time, optimizing mold temperature is key to improving output per hour.
Now that you understand why managing mold temperature matters, let’s see its effects on the injection molding process and products.
How Mold Temperature Impacts Injection Molding
Properly setting and controlling the mold temperature affects injection molding in three main ways:
1. Influences Appearance & Surface Finish
Mold surface temperature determines the rate at which the hot plastic material adjacent to the cavity walls solidifies.
- At higher temperatures – Slower solidification allows time for better replication of the mold surface. This results in glossier, aesthetically superior surfaces.
- At lower temperatures – Faster solidification restricts material flow, causing poor surface finish, ejection marks, and visible weld lines.
However, excessively high temperatures can also cause problems like flashing, burning, and sticking to the mold.
So you need to find the “sweet spot” temperature for optimal surface quality.
2. Determines Shrinkage, Warpage & Part Dimensions
The mold temperature governs the cooling rate and crystallization pattern of the plastic material inside the mold. This directly impacts the final shrinkage and dimensions.
- At higher temperatures slower cooling allows more uniform shrinkage. But increased overall shrinkage causes smaller part dimensions.
- At lower temperatures faster cooling “freezes” molecules quicker, reducing shrinkage. But uneven cooling causes warpage and dimensional deviations.
So again, an optimal mold temperature needs to be found to minimize shrinkage and warpage.
3. Affects Mechanical Strength & Other Properties
The mold temperature influences crystallization behavior, molecular orientation, residual stresses, and weld line strength.
- At higher temperatures the improved morphology leads to better ductility, impact strength, and chemical resistance.
- At lower temperatures increased residual stresses and molecular orientation reduces mechanical performance.
In semi-crystalline plastics like polyethylene, optimal mold temperatures result in just the right level of crystallinity for balanced properties.
Now that you know about the effects let’s move on to actually selecting suitable mold temperatures.
Recommended Mold Temperatures for Different Plastics
The ideal mold temperature window varies widely depending on the plastic material.
Here are the recommended mold temperatures for some commonly used plastics:
Plastic | Mold Temperature Range |
---|---|
ABS | 40-90°C |
Polypropylene (PP) | 15-60°C |
Nylon 6 (PA6) | 80-120°C |
Polycarbonate (PC) | 90-150°C |
Acrylic (PMMA) | 35-70°C |
PVC | 10-50°C |
Polyethylene (PE) | 10-50°C |
Polyurethane (PU) | 40-60°C |
These values serve as a good starting point. Further fine-tuning is required to determine the exact optimal temperature.
Now let’s look at some key tips on how to zero-in on the perfect mold temperature.
Tips for Setting Optimal Mold Temperatures
Determining the right mold temperature for a given plastic material and injection molded part requires testing and analysis.
Here are 5 tips to help narrow down the ideal temperature window:
1. Start With Material Supplier’s Recommendation
Most resin manufacturers provide a generic recommended mold temperature range in the product datasheet.
Always begin testing from the lowest value suggested by them.
2. Consider Wall Thickness & Geometry
Thicker walls need relatively lower temperatures to avoid sink marks and deformation caused by residual heat.
Conversely, thinner sections require higher temperatures for proper filling and replication.
3. Monitor Pressure-Velocity Changeover
Observe the point during filling where velocity drops and pressure increases drastically, signaling solidification onset.
Adjust temperature so the changeover occurs when around 90% of the cavity is filled.
4. Use Thermocouples for Cavity Temperature Measurement
Thermocouples give the exact real-time mold surface temperature during the process, allowing accurate fine-tuning.
Without them, you would have to rely on guesswork and trial-and-error.
5. Perform DOEs to Identify Optimal Setting
While thermocouples help, the optimum mold temperature can only be determined conclusively by doing careful molding trials using Design of Experiments (DOEs).
This allows identifying the perfect combination of parameters yielding best quality at maximum productivity.
The Takeaway
Determining and controlling the mold temperature is vital for producing defect-free, dimensionally accurate plastic parts consistently at the lowest cycle time.
While the guidelines and values suggested here serve as a starting point, extensive analysis and testing are imperative to uncover the ideal temperature.
The small upfront investment is well worth it, saving you countless hours of headaches and rejections resulting from incorrectly set temperatures.
Now over to you – what role does mold temperature play in your injection molding process? Let me know in the comments!