What is melt temperature in injection molding? As one of the most critical process parameters, getting the melt temperature right is key to producing quality plastic parts efficiently. In this complete guide, as a professional plastic injection molding manufacturer, I’ll explain everything you need to know about melt temperature, including:
- What is melt temperature?
- Why controlling melt temperature matters
- How melt temperature impacts part properties
- Best practices for setting and measuring melt temperature
- The relationship between melt and mold temperatures
By the end, you’ll have a solid grasp of this foundational concept so you can better control your injection molding processes. Let’s get started!
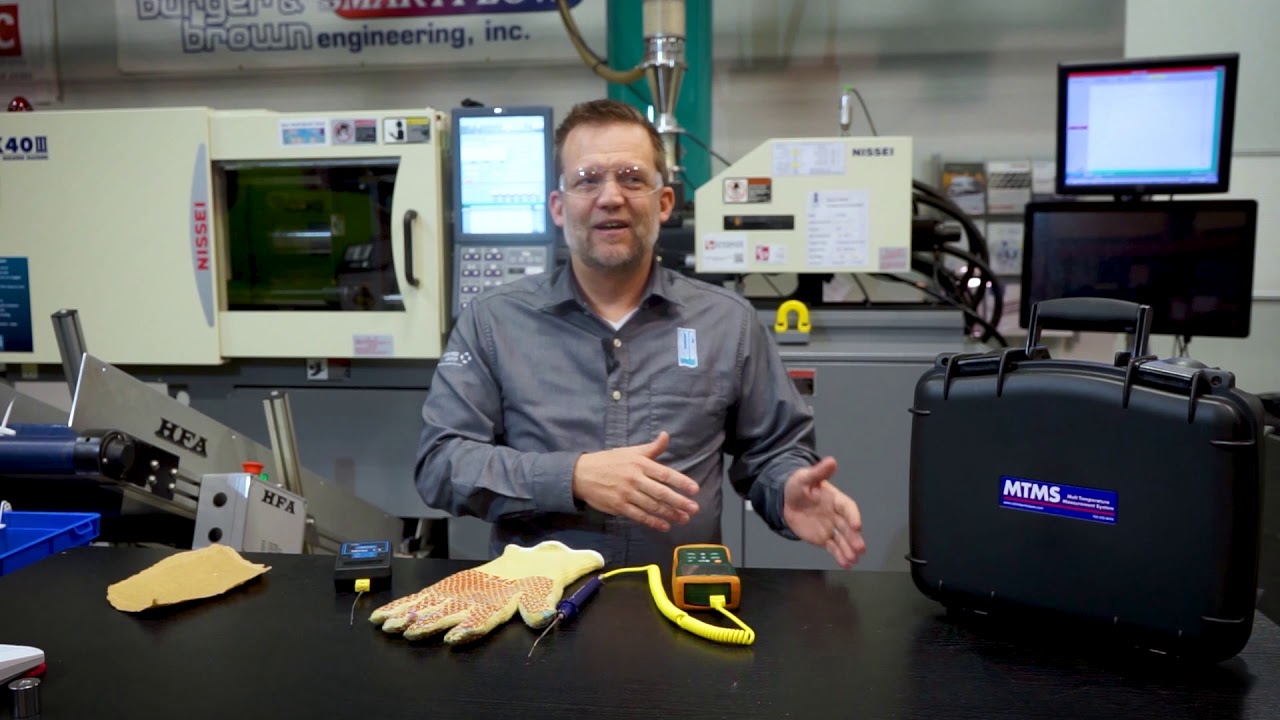
What Is Melt Temperature in Injection Molding?
Melt temperature refers to the actual temperature of the molten plastic as it exits the injection molding machine’s nozzle and enters the mold. This temperature can differ substantially from the barrel set temperatures due to shear heating and other factors.
Getting the melt temperature right is crucial because it influences the viscosity of the plastic, how easily it flows into the mold, and the properties of the finished part. For example, a melt temp that’s too high can degrade the polymer while one that’s too low can impede flow and cause short shots.
Generally speaking, amorphous resins like ABS and PC require higher melt temps while semi-crystalline resins like PP and HDPE flow better at lower temps. But the optimum melt temp depends on the specific grade being run.
Why Is Controlling Melt Temperature So Important?
Melt temperature impacts several critical molding objectives:
Part Quality: An off-spec melt temp can alter the resin’s viscosity and molecular weight, leading to defects, dimensional instability, property variations, and other quality issues.
Efficiency: The wrong melt temp lengthens cycle times, leading to lower output. It can also degrade material properties over time.
Consistency: Fluctuations in melt temp, even small ones, can introduce unacceptable variations between batches.
Clearly, keeping a tight leash on melt temp is imperative for producing quality parts, maximizing productivity, and ensuring process stability.
How Does Melt Temperature Affect Part Properties?
By influencing resin viscosity and other characteristics, melt temp adjustments give processors some control over the properties of finished parts.
Strength & Impact Resistance: Lower melt temps generally yield higher strength and impact resistance. The cooler resin retains more of its molecular weight through the molding process.
Shrinkage: Too high a melt temp causes the plastic to expand more in the mold, increasing shrinkage. Slightly lower melt temps counteract this.
Cycle Time: Reduced viscosity at higher melt temps can cut molding cycles but usually at the expense of properties. There’s a balance to be struck.
Viscosity: The hotter the melt, the lower its viscosity. But dropping viscosity too far risks unstable flow front velocities.
Through judicious melt temp adjustments, manufacturers can tailor parts’ strength, shrinkage, cycle times and other attributes to meet application requirements.
Best Practices For Setting & Measuring Melt Temperature
Though individual resins have recommended melt temp ranges, honing in on the optimal setting takes testing, fine-tuning, and constant vigilance. Here are some tips:
Start low: Begin with the lowest workable melt temp for the material grade. This minimizes thermal degradation while you dial in other parameters. Once the process stabilizes, slowly inch the melt temp upward if needed to reduce viscosity or cycles.
Use updated equipment: Melt temp controllers with thermocouple or RTD sensors embedded in the nozzle for continuous measurement eliminate guesswork and speed optimization.
Measure systematically: Use the same procedure (e.g., purging into an insulated container) each time you check melt temp to ensure consistency. Automated, in-line measurement systems yield the best data.
Keep records: Log all process parameters along with melt temp so you can accurately analyze trends over time. Any changes should have a traceable, quantitative reason behind them.
Monitoring and controlling melt temp takes effort but pays dividends in quality, efficiency, and stability. Following structured procedures and leveraging smart technology makes it easier while also generating valuable process data.
What’s the Relationship Between Melt & Mold Temperatures?
Melt and mold temperatures are inherently interdependent, even if set independently.
The main connections between these two crucial injection molding parameters include:
Shear heating: Frictional heat generated from melt flow through sprue an runners raises mold surface temps. Faster cycles compound this effect.
Cooling efficiency: How readily the melt cools in the mold depends partly on the thermal gradient between the plastic and mold surface. Large deltas aid cooling.
Cushion: A slight variance between hotter melt and cooler mold temps provides a helpful cushion that prevents drops below the material’s minimum viscosity or freezes before the cavity fills.
Property optimization: As with most processing variables, the ideal combination of melt & mold temps maximizes quality & efficiency. Some trial & error is needed to find each material’s “sweet spot”.
So while melt & mold temperatures may seem distinct, it’s important to consider both holistically. The total energy picture matters more than either one individually. Modeling software can provide useful guidance on optimizing this balance.