Injection molding is a complex manufacturing process with many intricate details. One term that often gets thrown around is “melt cushion.” But what exactly is a melt cushion? And why does it matter in injection molding? As a professional plastic injection molding manufacturer, I will help you find it out.
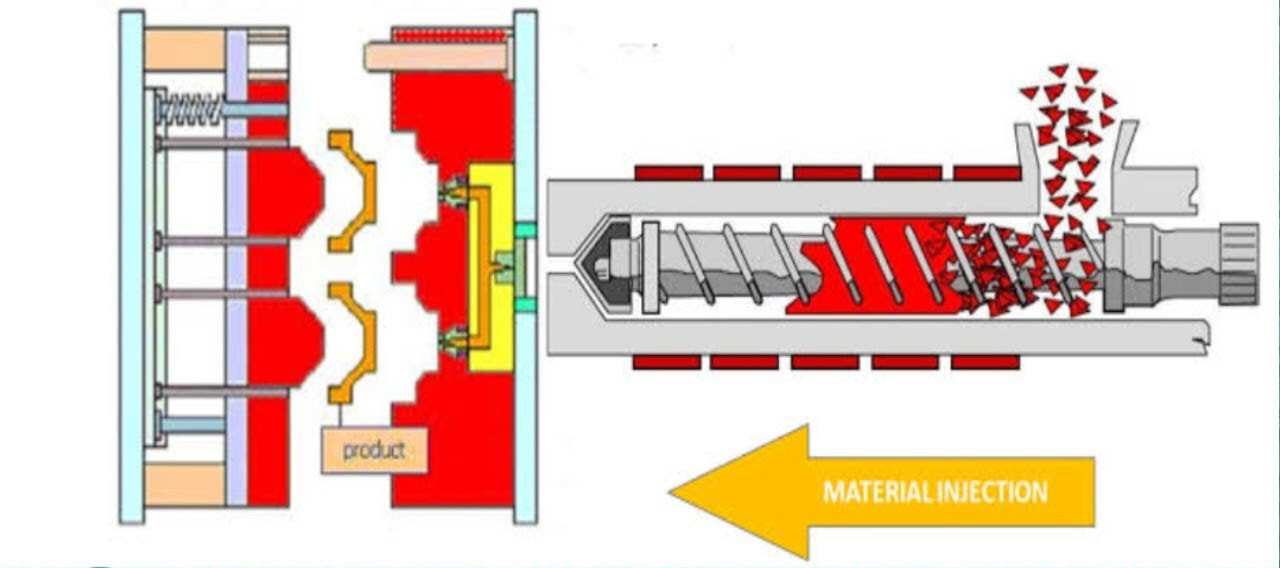
What is Melt Cushion in Injection Molding?
The melt cushion refers to the amount of molten plastic that sits between the screw tip and the mold after the injection process.
To visualize this, during the injection cycle the screw moves forward, pushing molten plastic through the nozzle, sprue, runners and into the mold cavities. At the end of injection, the optimal amount of plastic remains between the very front of the screw and the mold. This is your melt cushion.
Why Have a Melt Cushion?
You need a melt cushion to apply packing pressure.
Packing pressure is critical for making quality parts. It packs the plastic into every crevice of the mold, compensating for shrinkage as the part cools.
Without a melt cushion, the screw has nothing to push against once it bottoms out. You lose the ability to apply packing pressure. This causes all sorts of issues:
- Short shots
- Sinks and voids
- Warpage
- Dimensional inaccuracy
Maintaining a proper melt cushion ensures you can sufficiently pack out the mold.
How Much Melt Cushion Do You Need?
Ideally, you want the smallest melt cushion possible that still allows packing pressure. A rule of thumb is a melt cushion between 0.100-0.250 inches (2.5-6mm).
Why aim for a smaller cushion? Two reasons:
1. Material Degradation
The nozzle area almost always runs hotter than the rest of the barrel. This means the plastic near the nozzle is more likely to thermally degrade.
And due to the fountain flow effect, this nozzle plastic travels into the cavities first.
A large cushion floods your part with degraded nozzle plastic. Tiny impurities and discoloration can cause cosmetic defects. And at higher levels, degraded polymers lead to mechanical failure.
2. Excessive Compression
Plastic is compressible. The larger your cushion, the more packing pressure gets “used up” compressing the melt cushion itself. This steals pressure that should go into the mold.
For tricky materials like PVC, excessive compression makes controlling cavity pressure consistency almost impossible. Keeping melt cushion tight minimizes variability shot-to-shot.
Signs of Insufficient Melt Cushion
If your injection molding process lacks proper cushion, you’re likely to notice:
- Short shots
- Voids
- Sinks
- Warpage
- Dimensions out of spec
- Cosmetic issues like flow lines, jetting
These part defects point to improper packing and holding pressure. And improper pressure usually stems from inadequate melt cushion.
Thankfully, monitoring cushion is quite simple on most molding machines. Pay close attention for any drift or deviation. Tighten up your tolerance band if you notice creeping inconsistency over multiple cycles.
While monitoring cushion won’t solve all injection molding problems, it’s one of the easiest ways to start narrowing things down. And addressing cushion issues early keeps tiny problems from cascading into major defects.
What about you? What kind of issues have you seen from insufficient melt cushion? Let me know in the comments!