Jetting is a common defect that can occur during the injection molding process, resulting in undesirable ripples, waves, or streaks on the surface of plastic parts. In this complete guide, as a professional plastic injection molding manufacturer, we’ll cover everything you need to know about jetting in injection molding, including what causes it, how to prevent it, and troubleshooting solutions.
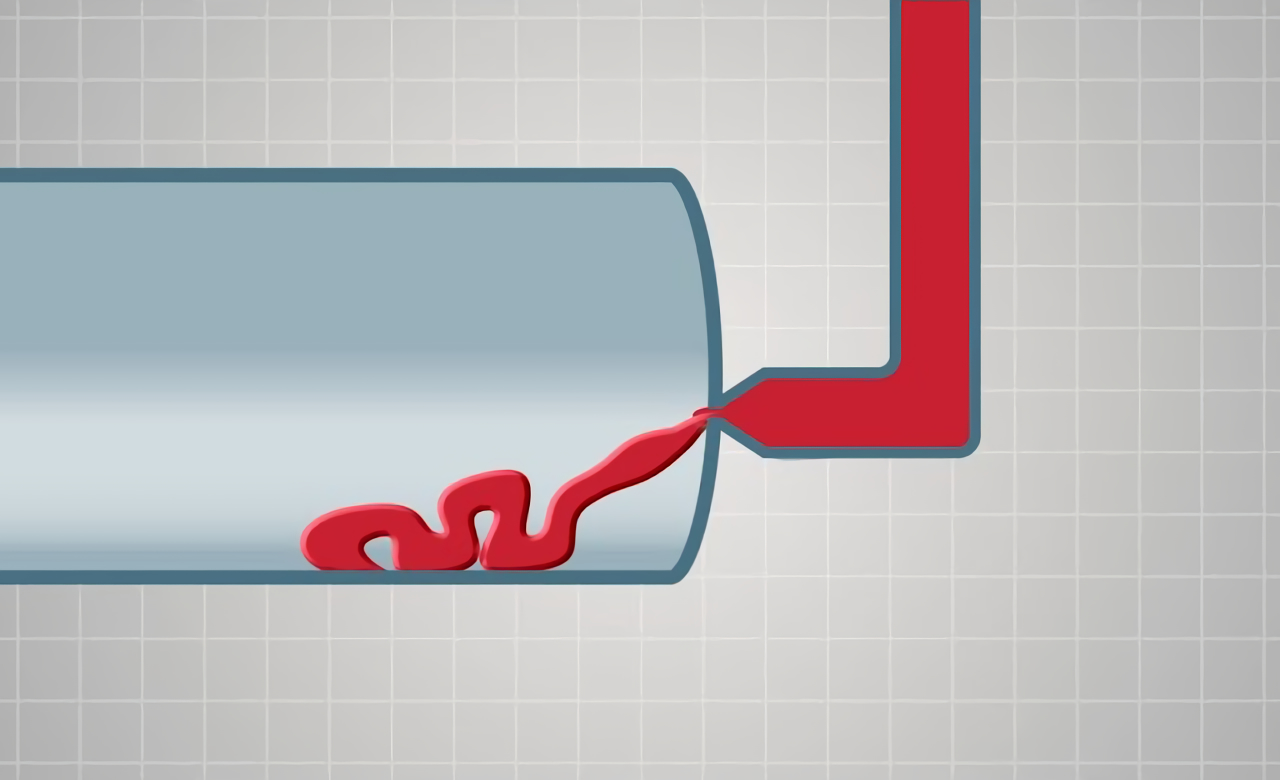
What is Jetting in Injection Molding?
The jetting in injection molding is a turbulence phenomenon that occurs when the initial stream of molten plastic enters the mold cavity at a high velocity without immediately adhering to the mold walls. This causes the material to “jet” into the open space, creating visible ripples or streaks on the component surface that resemble snake-like or worm-track patterns.
Jetting stems from the material flowing too quickly from a restricted gate, nozzle, runner, etc. into a larger cavity space. As the fast-moving polymer fails to uniformly fill the cavity, the turbulent flow creates visible surface defects on the molded parts in the form of squiggly lines or waves.
The jetted plastic also starts to cool and harden before the rest of the cavity fills. So the rippled pattern remains even after the part solidifies, creating an uneven finish, ghost lines, or visible distortions on the final molded components.
What Causes Jetting in Injection Molding
There are several potential factors that can contribute to jetting defects occurring during the injection molding process:
1. High Injection or Ram Speed
Excessive injection speed or ram velocity is often the main culprit behind jetting issues. Too much velocity through narrow gates or orifices causes the shearing and spraying behavior.
2. Improper Gate Design
Small gate thickness relative to part wall thickness fails to provide adequate back pressure. Large gates poorly placed allow unconstrained plastic flow. Both scenarios risk jetting.
3. Low Viscosity Material
Thin, free-flowing material is more prone to spraying behavior than higher viscosity polymers when flowing into the cavity.
4. Low Cavity Pressure
Inadequate cavity pressure allows the leading edge of the material flow to pull away from the edges rather than packing out the part shape.
5. Premature Freezing
Cooler tooling temperatures can cause the melt flow to solidify too early, preventing the material from completely filling the cavity.
How to Prevent Jetting in Injection Molded Parts
Here are several methods for preventing jetting defects in injection molded components:
- Optimize gate design – use fan gates, submarine gates
- Strategic gate placement – adjacent to cavity walls
- Multi-stage injection speed control
- Lower overall injection velocity
- Increase holding pressure settings
- Higher mold & melt temperatures
- Utilize higher viscosity material grade
Troubleshooting Jetting in Plastic Parts
To troubleshoot existing jetting issues in injection molded parts:
- Inspect molded components for surface defects
- Review process data – injection speeds, pressures, temps
- Tweak gate size, position, geometry
- Adjust cooling times, mold & melt temp
- Try lower injection speeds
- Switch to higher viscosity resin grade
- Upgrade gate inserts, venting
- Simulation software to visualize flow
Proactive process monitoring, optimized tooling design, and vigilant parameter tweaking are key to preventing and rectifying jetting defects during injection molding operations. But when issues do creep up, following structured troubleshooting methods helps get parts back on spec quickly.
Things to Keep in Mind About Jetting
A few additional pointers regarding jetting defects in injection molded plastic components:
Jetting compromises part quality: While sometimes only a surface blemish, jetting can also undermine strength, function
Multiple root causes: No single factor definitively causes jetting; usually a confluence of processing conditions
Appears consistently: Jet lines typically appear in the same areas of consistently molded components
Simulation software helps: Analyzing theoretical material flow via scientific molding technology prevents real-world defects
Mold details matter: Vent location/depth, draft angles, surface finish—small tooling details influence jetting probability
Process refinements required: Tightened parameter windows needed to mitigate jetting; requires time, skill, diligence
Material selections wrong/right: Occasionally switching to a different resin grade radically reduces jetting tendency
Summing Up Jetting in Injection Molding
The fluid dynamics of the injection molding process, while incredibly fast and highly pressurized, are extremely sensitive. Factors such as filling imbalance, velocity differential, viscosity ratios that seem minor can ripple into significant end-use part defects like jetting.
But by taking the time to learn what is jetting in injection molding, processing engineers can tweak gate configurations, injection profiles, material rheologies and tool surface finishes to promote smoother, laminar flowfronts into cavities. Then maintaining tighter process controls keeps the operation reliably pumping out defect-free plastic parts.
Eliminating visible yet often subtle jetting defects presents considerable challenges for even seasoned injection molding experts. Thankfully following scientific molding principles through both processing refinements and component testing helps plastics manufacturers uphold their quality targets while achieving cost and efficiency advantages from injection molding in the long run.
The jetting in injection molding is an obstacle that molders and part designers can overcome through collaboration, troubleshooting teamwork and continuous improvement testing.