Gas assist injection molding is an innovative manufacturing process that produces hollow plastic parts. This technique combines traditional injection molding with pressurized inert gas to improve part quality, strength, surface finish and more.
I’ve been getting a lot of questions lately about gas assist injection molding and how it works. As a professional plastic injection molding manufacturer, I wanted to provide a detailed explainer on this emerging technology.
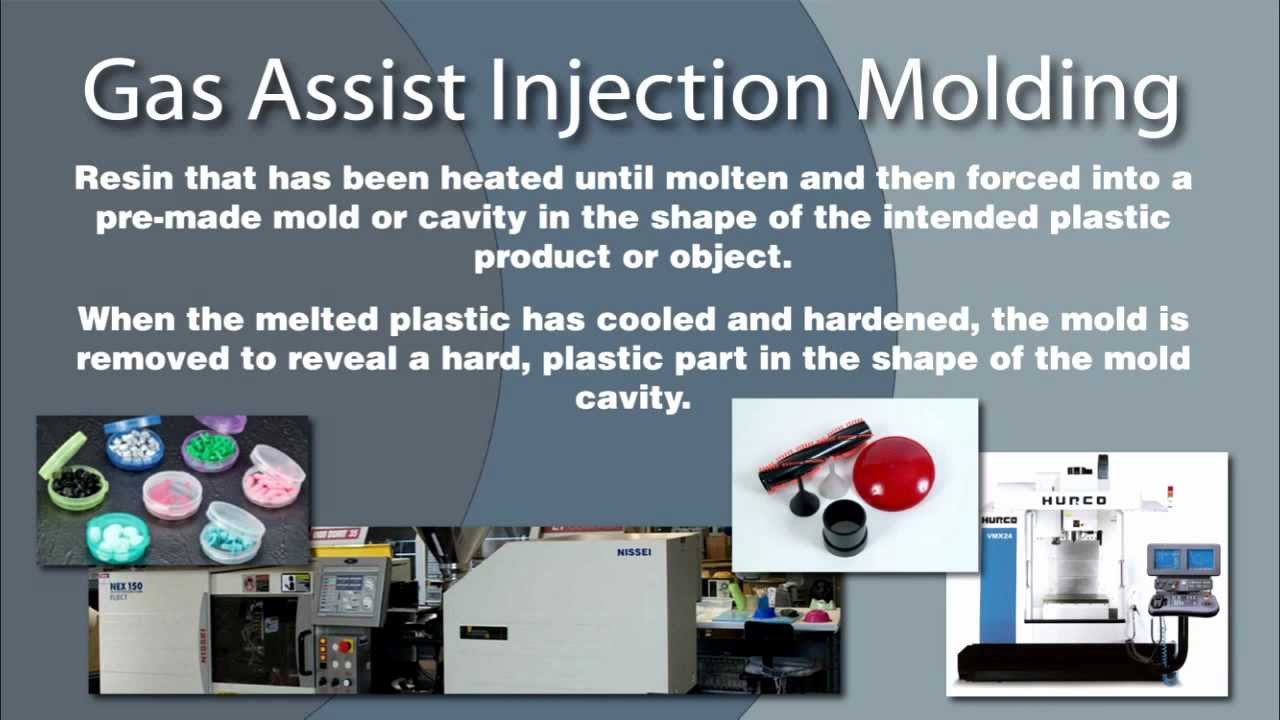
What is gas assist injection molding
Gas assist injection molding, sometimes referred to as gas injection molding, is a modified version of the conventional injection molding process. The key difference is that after the mold cavity fills partially with melted plastic, an inert gas (typically nitrogen) gets injected under high pressure.
The pressurized gas then pushes the plastic fully into the intricate areas of the mold. As the plastic starts solidifying, the gas applies constant pressure to pack the material tightly.
This gas pressure gets maintained throughout the cooling phase. Finally, the gas vents out once the part gets sufficiently rigid, resulting in a hollow interior.
The whole process allows creating hollow, lightweight parts with superior strength, surface finish, dimensional accuracy and more. When designed and executed correctly, gas assist injection molding can be a game-changer!
How gas assisted injection molding works
Now that you know what gas assist molding is at a high level let’s get into the nitty-gritty details of how the process works.
There are five main steps:
- Clamping – The mold closes and clamps together, same as regular injection molding.
- Filling – Melted plastic fills about 65-85% of the mold cavity volume, called the short shot volume.
- Gas Injection – High pressure nitrogen gas injects into the molten plastic through the sprue, runners or directly inside the cavity.
- Gas Penetration – The pressurized gas pushes the plastic fully into the intricate extremities of the mold.
- Packing – As the plastic starts solidifying, gas pressure maintains pack against the mold walls. This happens throughout the cooling phase.
So in a nutshell:
- Plastic half-fills the mold
- Gas pushes plastic fully into the mold
- Gas pressure holds plastic against mold during cooling
- Result: strong, hollow lightweight molded parts
Understanding these fundamentals helps appreciate why gas assist molding creates such high-quality plastic components.
Types of gas assist injection molding
There are two main types of gas assisted injection molding:
Internal gas assist
This process is more common. The pressurized nitrogen gas penetrates inside the molten plastic from the sprue or runner system. It expands within the material, hollowing out internal volumes.
The constant gas pressure during solidification provides stability to the parts. It prevents defects like warpage while achieving tight dimensional tolerances.
Internal gas assist works very well for injection molding large, flat items. It reduces their tendency to bow or deform, resulting in flatness.
External gas assist
In external gas assisted molding, the gas flows into an external channel between the part and core mold surfaces. Instead of creating an internal void, the gas packs the plastic against the cavity mold.
As the material solidifies, the uniform gas pressure holds it accurately against the mold. This ensures that even the finest mold details replicate onto the external plastic surfaces.
So external gas assist injection molding is perfect for getting flawless surface finishes. It completely eliminates sink marks, achieving a smooth, cosmetic surface.
Benefits of gas assist injection molding
Now that you understand the gas assist injection molding process, let’s discuss the key benefits it provides:
Superior part strength
The hollow sections and ribs possible with gas molding lend incredible strength despite reduced weight. Cleverly placing these structural enhancements imparts rigidity and durability.
Lower manufacturing costs
Gas assisted molding uses less plastic raw material per part, directly cutting costs. The faster cycle times due to faster cooling also boost production efficiency.
Complex geometries
Gas assist simplifies producing complex shapes with negative drafts, undercuts or deep draws that are otherwise difficult to injection mold.
Dimensional stability
The stability imparted by persistent interior gas pressure minimizes shrinkage. Parts maintain precise dimensions without warping or distortion.
Flawless surface finish
The gas holds the cooling plastic evenly across even the most intricate mold surfaces. This prevents defects like sink marks, achieving class-A surface finishes.
Lightweighting
Hollowing sections of the plastic part with gas decreases weight. This allows creating larger yet lighter components.
Consolidated parts
Gas assist enables combining previously separate injection molded components into a single multi-featured part by integrally molding inserts and ribs.
Extended tool life
The lower clamping pressures prolong tool longevity, extending mold lifecycles. This reduces maintenance costs and production downtime.
So in summary, gas assist injection molding simplifies manufacturing lightweight and high-strength parts with excellent surface quality by leveraging gas pressure.
The coming years will likely see gas assist molding adopted increasingly to push the limits of injection molding! Let me know in the comments if you have any other questions.