Injection molding is a popular manufacturing process used to produce plastic parts at scale. During this process, molten plastic is injected into a mold cavity to take on a desired shape.
One of the most important yet overlooked components in injection molds are shut-offs. What is a shut off in injection molding? As a professional plastic injection molding manufacturer, I will help you find it out.
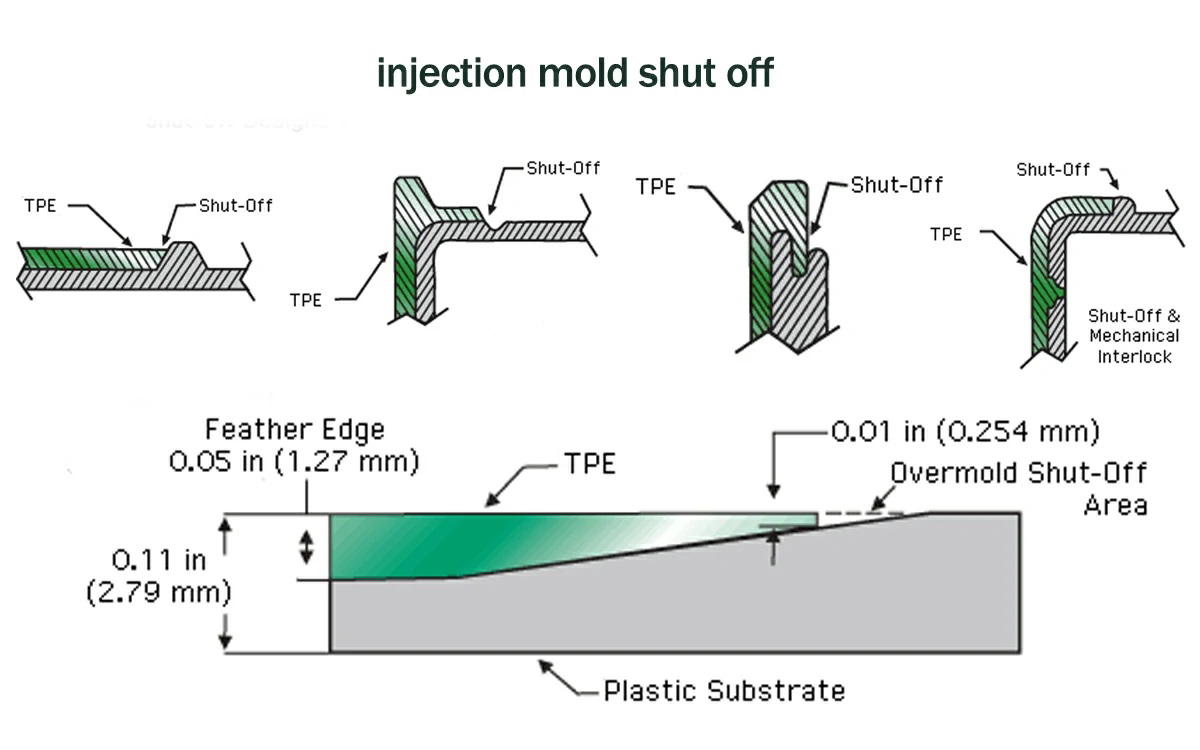
What Is a Shut Off?
A shut off refers to a specific area in an injection mold where the two halves meet to close off holes or cavities in the final plastic part.
Essentially, shut offs enable plastic to completely fill intricate mold cavities by sealing off sections. Without proper shut offs, the molten plastic material would simply leak out of cavities during injection and fail to fill the mold correctly.
So in summary, a mold shut off:
- Is an area where the two mold halves meet and seal
- Enables complete filling of complex mold cavities
- Prevents molten plastic from leaking and flashing
Now that you know what a basic mold shut off is, let’s look at the 4 main types of shut offs:
4 Main Types of Shut Offs
1. Shut Off Surface
A shut off surface simply refers to the area in the mold where the two halves meet. This surface essentially acts as a seal to enclose plastic within the mold cavity.
A shut off surface creates a seamless opening to fully enclose plastic within cavities.
Common examples include:
- Holes: Shut off surfaces around holes fully seal openings to create plastic tubes or other hollow parts
- Channels: Long openings are created using shut off surfaces to produce channels
2. Shut Off Angle
The shut off angle is the sloped region where the core and cavity halves intersect. This angle is extremely important for:
Preventing collisions when closing mold halves and avoiding damages
The shut off angle also contributes to proper sealing when plastic is injected at high pressures.
A minimum angle over 3 degrees is normally used.
3. Shut Off Nozzle
The injection nozzle has a channel that opens and closes. When closed, it stops plastic from leaking from the nozzle.
So in summary:
The shut off nozzle has a sealing mechanism to stop plastic leakage
This allows switching from a packed shot to an empty shot without material drool.
4. Sliding Shut Off
Some molds feature a sliding shut off design where two mold faces slide across each other when closing.
A sliding shut off provides flexibility for complex cavity designs. But if designed incorrectly, it can cause severe mold damages from the friction.
So in essence:
Sliding shut offs involve dynamic contacting surfaces that enable design flexibility.