Packing time is a critical yet often misunderstood phase of the injection molding process. As a professional injection molding manufacturer, I want to help you clear up exactly what packing time is, why it matters, and how the process goes.
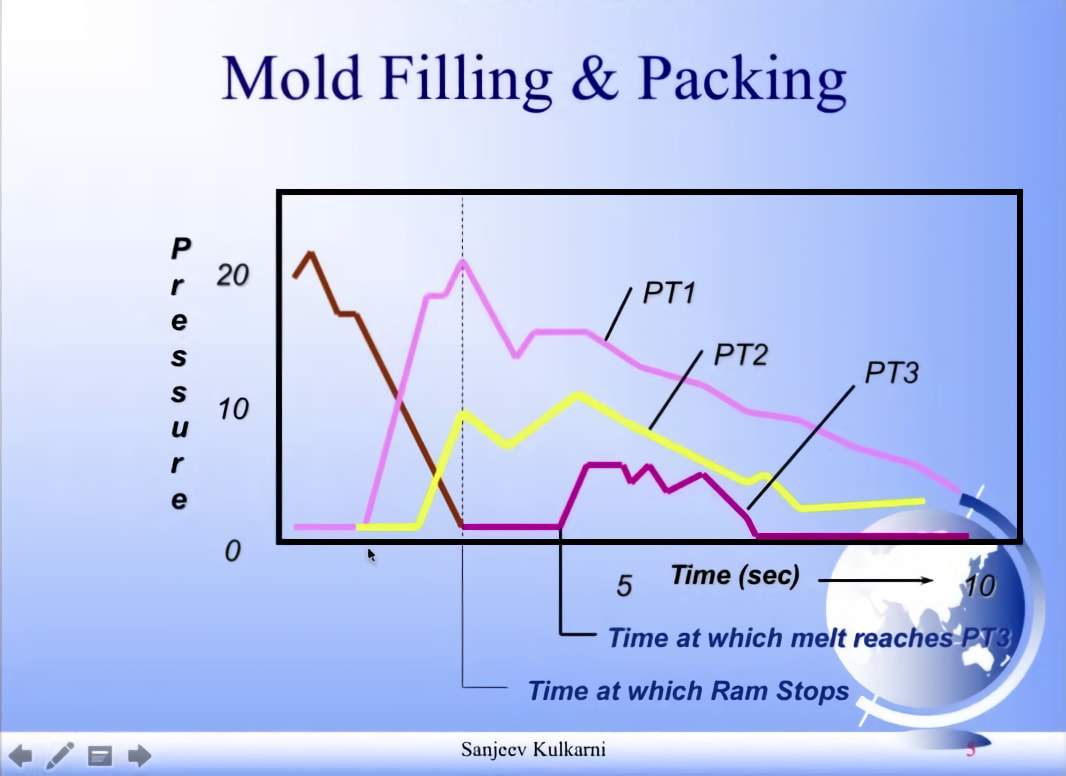
What Is Packing Time in Injection Molding?
Packing time in injection molding refers to the period during which additional material is injected into the mold after the initial filling phase. This phase is crucial for compensating for material shrinkage that occurs as the plastic cools and solidifies.
The Importance of Packing Time
Packing time allows us to pack more molten plastic into the mold cavity. This extra material gets compressed as the plastic starts to solidify.
Why do we need to add this extra plastic? When molten polymers cool down, the molecules start to draw closer together. This shrinks the final part. No bueno!
By packing additional material into the cavity, we’re able to compensate for this shrinkage. The end result? Parts that meet our exact specifications. Cha-ching!
Now, you might think:
Can’t I just fill the mold 100% during the initial injection phase?
Great question! When plastic is in molten form, it’s compressible. So even if you think you’ve filled the cavity completely, you likely haven’t.
Packing time gives us that extra OOMPH we need to truly fill ‘er up.
This isn’t a perfect analogy, but think about packing a suitcase.
You can cram in clothes until you think you’ve filled every square inch. But it always seems like you can finagle in a couple more pairs of socks after jumping on the suitcase.
Molten plastic works similarly. The packing phase gives us that “jump up and down on the suitcase” time.
Let’s break down exactly how packing time works…
The Packing Time Process
Packing time typically occurs in three distinct stages:
1. Fill
This initial injection phase fills around 95-98% of the mold cavity. I say “around” because hot plastic is compressible. So it’s impossible to precisely fill a specific percentage.
During this fill period, injection velocity is most important. We want to ram that plastic in as fast as possible before it starts to cool.
Once the cavity is almost full, we switch from velocity control to…
2. Pack
Now we apply packing pressure. This added oomph injects additional material to compensate for shrinkage.
Our goal is to completely fill the cavity and freeze the gate (so no molten plastic leaks out of the mold).
We want to avoid applying too much pressure here. Excess force can “over pack” the mold, causing flash and other defects.
Finding the sweet spot takes testing and optimizing pack pressure.
3. Hold
The final stage keeps packing pressure applied until the gate freezes off completely. Now plastic is packed tightly — no room for shrinkage.
We enter hold time once packing pressure hits steady-state equilibrium. This keeps material from back flowing as the gate solidifies.
Getting this timing right prevents sink marks, warpage, and other quality issues.
And duration varies based on material viscosity, part thickness, etc.
How Long Should Packing Time Last?
Packing duration depends on several factors:
- Material Used: More viscous polymers require longer pack times.
- Mold Complexity: Basic shapes pack faster than complex geometries.
- Part Size: Larger components need extended packing.
- Industry Standards: Medical devices often have tighter requirements.
As a general rule, packing lasts a fraction of the overall injection cycle:
- Typical Cycle – 25 seconds
- Typical Fill – 5 seconds
- Typical Pack – 2 seconds
But regardless of time, our top priority is part quality. We want to prevent defects like shrinkage, warpage, and sink marks.
So don’t be afraid to tweak pack times until you nail the optimal duration.
Takeaways
The packing phase of injection molding is critical, but complex. To quickly recap:
- Packing time adds material to compensate for shrinkage. This prevents part defects and dimensional issues once plastic cools.
- Pack duration is short compared to overall cycle length. But don’t be afraid to optimize time to enhance quality.
- Pressure and timing must balance one another to completely fill the mold and freeze the gate.
Adjusting even one second here or 100 psi there can have huge implications on part quality and efficiency. Make packing time a top priority for process optimization.
Getting packing time right takes testing, data, and experience. But it’s worth the investment for companies seriously committed to part quality.
So dive deep into packing science — and take your injection molding quality to the next level!