Cold slugs are a common issue in injection molding that can lead to defects on plastic parts. In this comprehensive guide, as a professional injection molding manufacturer, we’ll cover what exactly causes cold slugs, as well as solutions for preventing them.
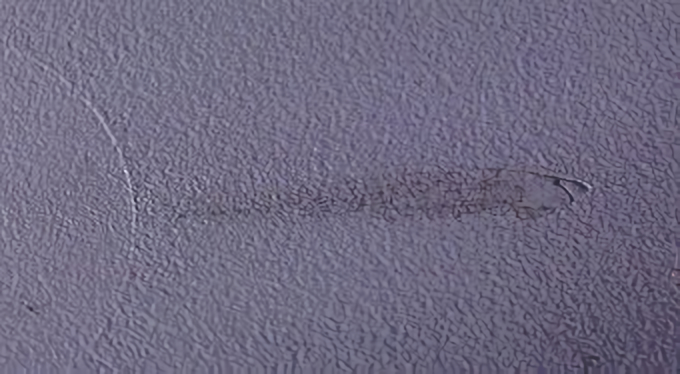
What Is Cold Slug in Injection Molding?
A cold slug refers to a small piece of plastic that has prematurely cooled and solidified inside the nozzle tip or hot runner system. As this slug of plastic moves through the mold, it can leave noticeable defects on the surface of parts.
You’ll typically see a cold slug as a visual imperfection on the molded plastic part. It may appear as:
- A rough, wavy mark
- A streak or scar
- A depression
- Discoloration
The location of cold slug defects provides clues as to their underlying cause. Marks near the gate indicate issues with nozzle or hot runner temperatures. Defects further from the gate suggest design problems like restrictive flow paths.
What Causes Cold Slugs in Injection Molding?
There are several potential root causes of cold slugs:
1. Low Nozzle or Hot Runner Temperatures
The most common cause of cold slugs is low nozzle or hot runner temperatures. The nozzle tip is in constant contact with cooled steel mold components. This makes it vulnerable to early cooling and slug formation.
Insufficient temperature in these areas fails to keep the plastic molten. As a result, the melt prematurely solidifies into cold slugs that contaminate parts.
2. Poor Gate and Runner Design
The gate is the passage through which plastic flows from the runner into the mold cavity. Poor gate design can contribute to cold slug issues by allowing build-up and stagnation.
Small gate sizes impede flow, while sharp transitions promote early cooling. These defects “trap” cold slugs that would otherwise enter the cavity.
3. Material Incompatibility
Some resins are inherently more vulnerable to early cooling and slug formation. For example, glass-filled materials and resins with high viscosities often require higher processing temperatures to remain molten.
If barrel, nozzle, and hot runner temperatures are not adjusted to match the material’s unique requirements, cold slugs can occur.
4. Processing Parameters
Variables like low injection speed, pressure, and temperature allow the melt to cool down too early. This increases viscosity and resistance to flow, allowing cold material to accumulate.
Faster cycles also limit the time available for heating plastic in the barrel, nozzle, and runners.
How Can You Prevent Cold Slugs?
Here are some key things you can do to avoid cold slug issues:
Raise nozzle and hot runner temperatures to recommended levels for the resin. Monitor and adjust as needed to keep plastic molten.
Redesign gates and runners with adequate sizes and streamlined geometries to promote smooth flow.
Select suitable materials and adjust processing conditions like temperature, speed, pressure, and cycle times accordingly.
Add a cold slug well – a reservoir at the end of runners to “trap” cold slugs before they reach the part.
Following these preventative measures will go a long way towards minimizing cold slug defects and associated scrap and quality issues.
Frequently Asked Questions About Cold Slugs
Below are answers to some other common questions about cold slugs:
What’s the difference between a cold slug and a flow mark?
Flow marks occur when the leading edge of flow cools as plastic fills the cavity. The melt front adheres to the cold mold surface, leaving behind marks.
Cold slugs form earlier, in the nozzle and hot runner system, before plastic enters the mold.
Can you eliminate cold slugs completely?
It is difficult to prevent cold slugs 100% of the time in injection molding. However, following the right processing procedures and machine setup will minimize their occurrence.
How do cold slugs affect part quality?
Cold slugs lead to visual defects and appearances issues on plastic parts. In extreme cases, they can also negatively impact strength properties. It’s best to prevent slugs to avoid these losses in quality.
In Summary
As outlined above, the main factors leading to cold slugs are:
- Low nozzle/hot runner temperature
- Restrictive runner and gate design
- Using the wrong material or process settings
- Running the machine too cold or too fast
Careful process monitoring and optimization helps avoid these common causes. Adding a cold slug well also traps slugs before they reach the molded parts.
Hopefully this guide gave you a helpful understanding of what exactly causes those pesky cold slugs in injection molding. Following the proper precautions during mold design and process setup will go a long way in preventing slug-related defects. Let me know in the comments if you have any other questions!