Troubleshooting for injection molding process is a critical skill for anyone working in plastic manufacturing. As an intricate production method with many variables, issues inevitably arise that require quick identification and remediation to avoid costly downtime. In this comprehensive guide, as a professional injection molding manufacturer, we’ll cover proven troubleshooting methodologies to efficiently resolve defects and stabilize processes.
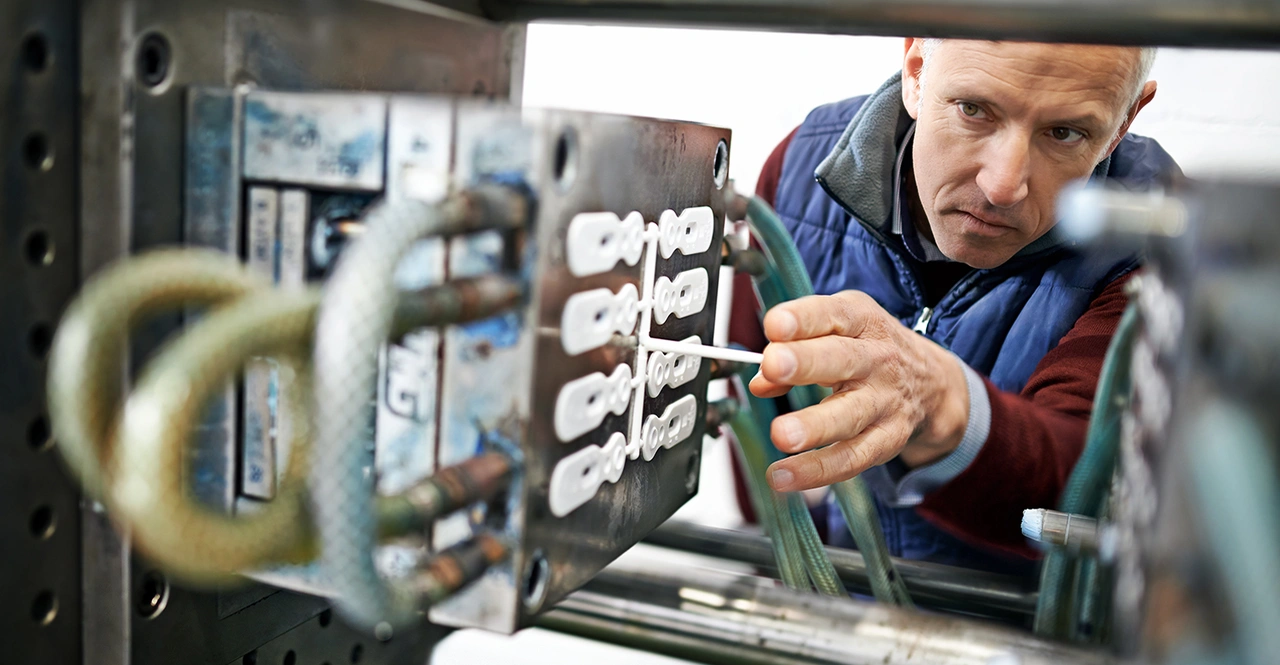
Introduction
The troubleshooting for injection molding process entails both reactive and proactive measures. Reactive efforts involve addressing defects as they occur through systematic root cause analysis and correction. Proactive efforts optimize processes for stability through robust machine setups, process control, and capability studies.
Mastering sound troubleshooting principles is essential for injection molders seeking operational excellence. By detecting issues early and quickly identifying solutions, processors can achieve higher throughputs, less scrap/rework, improved quality, and lower costs.
A Structured Approach to Injection Molding Troubleshooting
Effective troubleshooting requires structure to methodically walk through potential issues. Steps typically include:
Inspect Thoroughly
Carefully check the part for defects and measure critical dimensions. Photos aid analysis. Clean the mold and ensure moving components function properly.
Understand Baseline Conditions
Compare process setpoints to baseline parameters of a validated process. Review checklists for machine, material and mold preparation.
Analyze Root Causes
Evaluate possible process, material, mold, and machine factors according to the defect pattern. Analyze trends using process data.
Implement Solutions
Corrective actions should address root causes directly, starting with adjusting process conditions. Hardware changes are made only if necessary.
Confirm Results
Run tests to confirm the issue is resolved fully. Update process documentation and share findings across teams to prevent recurrence.
Now let’s examine some of the most common injection molding defects and practical tips to address them efficiently.
Common Injection Molding Defects and Solutions
Warpage
Warpage refers to the distortion or twisting in the molded part after ejection. It arises from uneven shrinkage, typically due to non-uniform wall thicknesses or cooling variations. Warpage is common in large, flat items with minimal ribs for structural rigidity.
Causes
- Uneven cooling from thick and thin sections
- Orientation from high injection velocities
- Residual molding stresses
- Ejecting before proper solidification
Solutions
- Optimize cooling circuits for uniform cooling
- Reduce injection speed and pack at lower pressures
- Increase mold temperature to reduce viscosity variations
- Delay ejection until plastic temperature drops sufficiently
Sink Marks
Sink marks are small, glossy depressions in the molding from insufficient packing pressure. They frequently appear when wall thicknesses change abruptly. Cosmetic in nature, sinks can be shallow dents to deep craters depending on part thickness.
Causes
- Low injection or pack pressures
- Early gate freeze-off
- High mold temperature
- Insufficient cooling time
Solutions
- Increase pack pressure, time, and melt injection rate
- Increase shot size and reduce cushion
- Relocate gate to thicker areas
- Lower melt and mold temperatures
Short Shots
Short shots refer to incomplete mold filling resulting in missing sections, usually farthest from the gate. Parts have visible flow frontlines where plastic stopped moving. Shorts arise from insufficient material volume, temperature or pressure to fully pack the mold.
Causes
- Low injection rate or pressures
- Early gate freezing
- Excessive viscosity
- Moisture inhibiting flow
- Plugged vents trapping gases
Solutions
- Increase shot size, injection speed, melt temperature
- Raise pack/hold pressure, time
- Ensure adequate vent depth
- Dry material according to specifications
Flash
Flash consists of thin plastic layers with fin-like protrusions along mold parting lines, ejector pins, slides or inserts. Flashing arises when the clamp force is inadequate to resist injection pressures, allowing mold faces to separate slightly.
Causes
- High injection pressure or speeds
- Insufficient mold clamping force
- Improper vent depth
- Poor alignment of mold plates
Solutions
- Lower injection pressure and increase time
- Increase clamp tonnage or boost pressure
- Adjust flash land depths
- Improve mold alignment and machining
Burn Marks
Burn marks refer to the darkened or discolored specks and streaks on a molded part, usually near gates, vents or runners. Burning arises from overheating in these flow restricted areas, either from excessive shear or lack of cooling.
Causes
- High injection rate raising shear heat
- Poor gate, runner, land design
- Lack of cooling near gates
- Material compatibility issues
Solutions
- Reduce injection speeds and pressures
- Upgrade gates, runners, nozzle
- Add cooling channels near gate
- Ensure proper material drying
Jetting
Jetting refers to flow lines or high gloss streaks caused by the melt fountain effect. It occurs when the melt doesn’t impinge upon the cavity walls and creates turbulent, rushing flow. Jetting arises from high injection speeds without sufficient back pressure.
Causes
- High injection velocity
- Low back pressure
- Small gate diameter
- Lack of impingement
Solutions
- Reduce injection speed
- Increase back pressure for laminar flow
- Open gate size for smooth entry
- Impinge melt on thick ribs/bosses
Voids
Voids are small air pockets appearing within parts, usually in thicker areas. They arise from gases dissolved in the melt under heat/pressure that come out of solution when pressures drop suddenly. The gases are then trapped inside the part body.
Causes
- Moisture outgassing
- Early gate freezing
- Low packing pressure
- Poor venting design
Solutions
- Dry material according to guidelines
- Increase pack pressure, gates
- Relocate gates to heavier sections
- Add properly-sized vents
Flow Lines
Flow lines refer to visible weld lines along the flow front boundaries arising from fountain flow. They appear as surface ripples or roughness in line with melt flow, accentuated by orienting additives. Flow lines indicate packing before gates freeze off.
Causes
- Low melt temperatures
- Slow fill rate allowing skins formation
- Non-uniform cooling
- Geometric shapes causing flow splits
Solutions
- Increase melt, mold temperatures
- Boost injection fill rates
- Equalize section wall thicknesses
- Round internal corners
Surface Defects
Surface defects cover molded-in textures causing poor aesthetics instead of designed high gloss. They arise from fillers, moisture, or other contaminants altering surface finish. Defect types range from pits, streaks and dimples to rough skin textures.
Causes
- CarryoverCross contamination
- Poor mold polishingMoisture in materialsGate blushRegrinds with contaminants
Solutions
- Production sequencing
- Mold cleaning
- Dryers operating correctly
- Venting
- Shorter cycles
- Clean regrind
Color Streaking
Color streaking consists of uneven color distribution in the molded part, appearing as light/dark stripes. It results from poor dispersion of colorants in the resin or an non-homogenous melt. High shear or temperatures degrade additives.
Causes
- Inadequate mixing/blending
- Partial clogging of hot runners
- Excessive resin residence time
- High screw rpm, injection speeds
Solutions
- Increase back pressure and screw rpm
- Clean out hot runners fully
- Reduce cycles and residence time
- Lower injection velocities
Splay Marks
Splay marks refer to silver streaks radiating irregularly from flow fronts caused by minor separation of melt layers. They resemble cracks under magnified inspection. Splay arises from contamination, moisture, or decomposition in shear zones.
Causes
- Material overheating and degradation
- Trapped moisture flashing off
- Regrind contamination
- Excessive shear heating
Solutions
- Lower barrel temperatures
- Dry materials properly
- Eliminate contamination sources
- Increase venting depth
Weld Lines
Weld lines are visible seam lines where separate melt flow fronts meet up. They have lower strength than bulk material. Holding pressure must pack the mold before skins completely freeze off into a weak knitline.
Causes
- Premature skin formation
- Low melt temperatures
- Non-uniform cooling
- Improper venting
Solutions
- Boost melt/mold temperatures
- Increase injection fill rates
- Equalize section thicknesses
- Enlarge vents for trapped gases
Brittleness
Brittleness refers to the loss of impact strength or ductility of parts, causing cracking or fractures under stress. Fillers, reinforcements and pigments can embrittle materials. Thermal or mechanical degradation also reduce toughness.
Causes
- Contamination from degraded materials or cross-mixed resins
- Excessive fillers reducing impact resistance
- Overheating from high shear or temperatures
- Internal voids initiating crack propagation
Solutions
- Prevent cross-contamination
- Optimize filler loadings for impact strength
- Lower process temperatures
- Boost packing pressure to minimize voids
Effective Injection Molding Troubleshooting
Learning to quickly recognize defects, comprehensively evaluate their root causes, and identify corrective actions separates average from elite injection molders. Developing process control through scientific molding principles minimizes troubleshooting firefighting.
By leveraging a structured approach and this overview of common molding issues, processors can achieve high uptime, yields and capability. Mastering troubleshooting for injection molding process establishes stability required for lean operations.