Injection molding is a versatile manufacturing process used to produce plastic parts and products in all shapes and sizes. From small and intricate components to large molded parts, injection molding can handle it all.
But when it comes to large part injection molding specifically, the process becomes more complex. The material requirements change as the molded components increase in size and thickness. Factors like strength, durability, flexibility, chemical resistance, and cost play an even bigger role.
So what materials work best for large part injection molding? Let’s break it down.
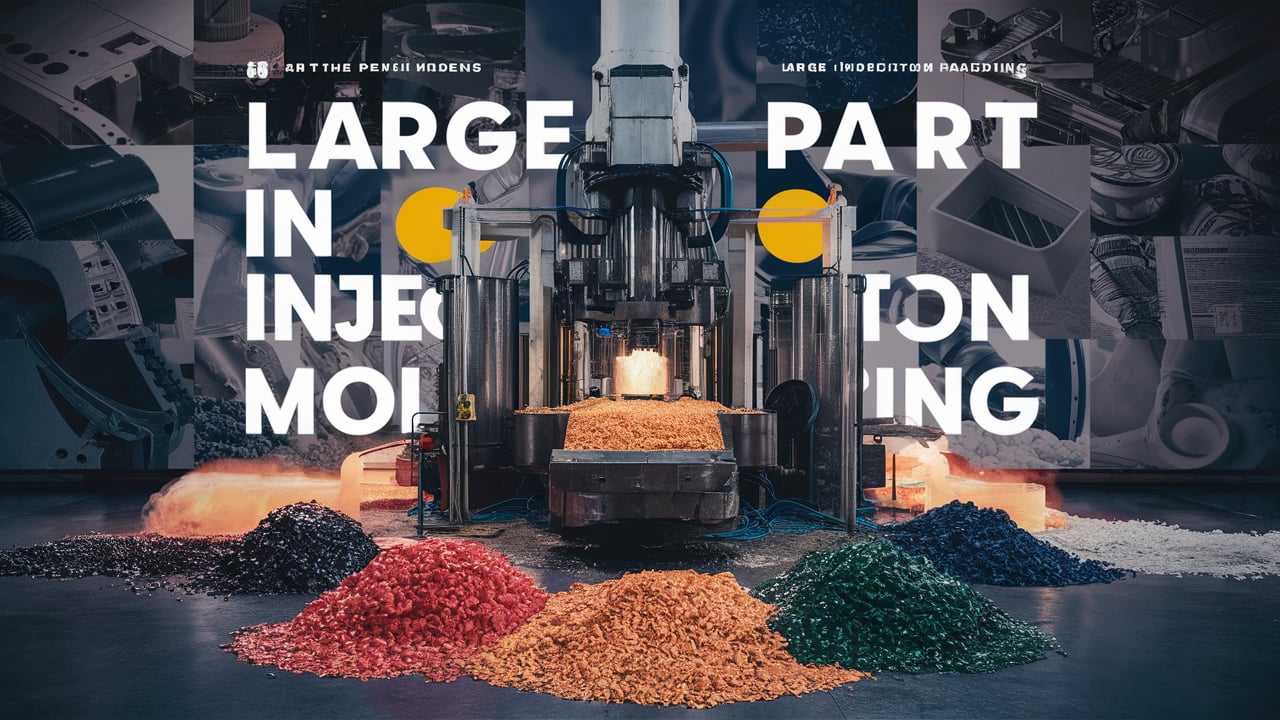
Overview of Large Part Injection Molding
First, what constitutes a “large” molded part? There’s no definitive size cutoff, but generally parts with:
- Surface areas over 16 square feet
- Weights exceeding 8 pounds
- Wall thicknesses over 1⁄4 inch
…are considered large components suitable for large tonnage injection molding machines.
Producing big molded pieces requires some key equipment considerations beyond just size and clamping force capacity, including:
- Robotic parts handling systems
- Conveyor systems
- Temperature and pressure control instrumentation
- Material drying and handling systems
But the most critical factor is choosing the right thermoplastic material.
Molded Material Properties To Consider
With large surface areas and volumes, the thermoplastic resins must maintain structural integrity across the entire molded component. Some key material properties include:
Strength and Impact Resistance
The large molded part must withstand various forces during manufacturing, assembly, and operation without cracking or deforming. High tensile and flexural strength are essential.
Heat Resistance
Big molded components can be exposed to high temperatures during manufacturing or use. The material must retain properties despite heat exposure during injection molding or later during product operation.
Chemical Resistance
Depending on the application, the large scale plastic part may come into contact with oils, solvents, or other chemicals. The optimal molding material will resist deterioration or changes in critical properties upon chemical exposures.
Dimensional Stability
Larger molded components have less margin for error. The chosen plastic must produce dimensionally consistent, uniform products within tight tolerances, despite molding challenges posed by large part tooling.
Best Materials for Oversized Injection Molded Components
With key material performance factors covered, what plastic resins work for big injection molded parts? Here are five commonly used materials suitable for the task:
1. Polypropylene (PP)
Polypropylene is a versatile, high-volume injection molding resin used in everything from food containers to auto parts. The high melt flow rate makes PP easy to process, even for sizable components.
PP features high flexural strength and rigidity critical for large products where deformation control is vital. The excellent chemical resistance suits many industrial components, while great fatigue strength suits repeated cyclical stresses.
Cost-effectiveness makes polypropylene useful for large yet affordable end-use plastic parts, from crates and trays to dunnage racks, bins, and pallets.
2. Acrylonitrile Butadiene Styrene (ABS)
ABS is another widely molded workhorse polymer, with properties meeting demands of weighty injection molded components.
The ABS thermoplastic blend combines strength, rigidity, and high impact resistance thanks to its butadiene rubber content. Easy flow allows molten ABS to fill intricate voids within sizable mold tooling.
From automotive body panels to enclosure clamshells, large-format ABS injection molding produces plastic parts with the durability to withstand rough handling and wear. Cost efficiency also helps heavy ABS components suit mass production environments.
3. Polyamide (Nylon)
Nylon injection molding grades make excellent candidates for substantial molded pieces where chemical resistance and mechanical performance both matter.
Strong intermolecular hydrogen bonding bestows nylons with high strength and stiffness, abrasion and wear resistance, plus stability upon repeated stresses. Though prone to moisture absorption, nylon makes long-lasting, dimensionally-stable big molded parts across manufacturing and assembly settings.
Oversized nylon components also withstand moderate heat and broad chemical exposures, ideal for demanding aspects of medical, industrial, and automotive hardware designs. From all-terrain vehicle cargo racks to medical cart tubs and covers, robust nylon molds hold form.
4. Polycarbonate (PC)
For plastic parts too large for high-impact polystyrene or acrylic, polycarbonate injection molding represents the next step up in strength, temperature resistance, and dimensional stability for transparent components.
PC retains high tensile and flexural strength from room temperature up to 150°C heat conditions. Large molded polycarbonate leverages these mechanical advantages across larger surface areas, suiting mechanically demanding applications.
Big PC molding projects span from equipment exteriors and covers to riot shields, machine guards, structural building profiles, and bullet-resistant barriers. The oversized yet shatter-resistant plastic parts also serve medical imaging and electronics enclosures at macro scales.
5. Polyetherimide (PEI)
As an advanced engineering thermoplastic, PEI polyetherimide delivers exceptional thermomechanical performance suitable for very substantial molded pieces used in demanding equipment environments.
Made from bisphenol-A and aromatic diamines, PEI offers unmatched heat resistance, holding mechanical strength past 170°C – critical for spacious plastic components facing hot hydraulic fluids, steam, or high-temperature cycling in industrial systems.
On top of heat and stress crack resistance, PEI also boasts broad chemical compatibility. Large molded parts withstand oils, alcohers, dilute organic acids, and alkalies. PEI makes lasting injection molded structural and fluid handling parts in aircraft and machinery where other plastics fail.
Start Your Large Part Injection Molding Project
Designing and manufacturing oversized injection molded components comes with unique complexities. Material selection plays a defining role in part performance, longevity, and cost-efficiency across full production cycles.
If starting a big plastic molding project, get in touch with our engineering experts. We leverage decades of experience producing all manner of large injection molded components to help identify the optimal combination of molding material, machinery, and manufacturing methods for your application.