Injection molding is a manufacturing workhorse across countless industries. It churns out everything from Legos to auto body panels using the same basic principles: heat up plastic until it’s liquid, inject it into a mold, cool it into a solid shape.
But not all injection molding is created equal. Traditional injection molding machines are typically smaller and geared towards high-volume production of small parts. Large part injection molding requires heavy-duty machinery to produce oversized components like pallets, crates, furniture, and appliance housing.
If you find yourself needing big plastic parts made, it can be tempting just to upsize from traditional to large part injection molding. However, it’s not as simple as scaling up – there are several key differences to consider first before pulling the “go” lever.
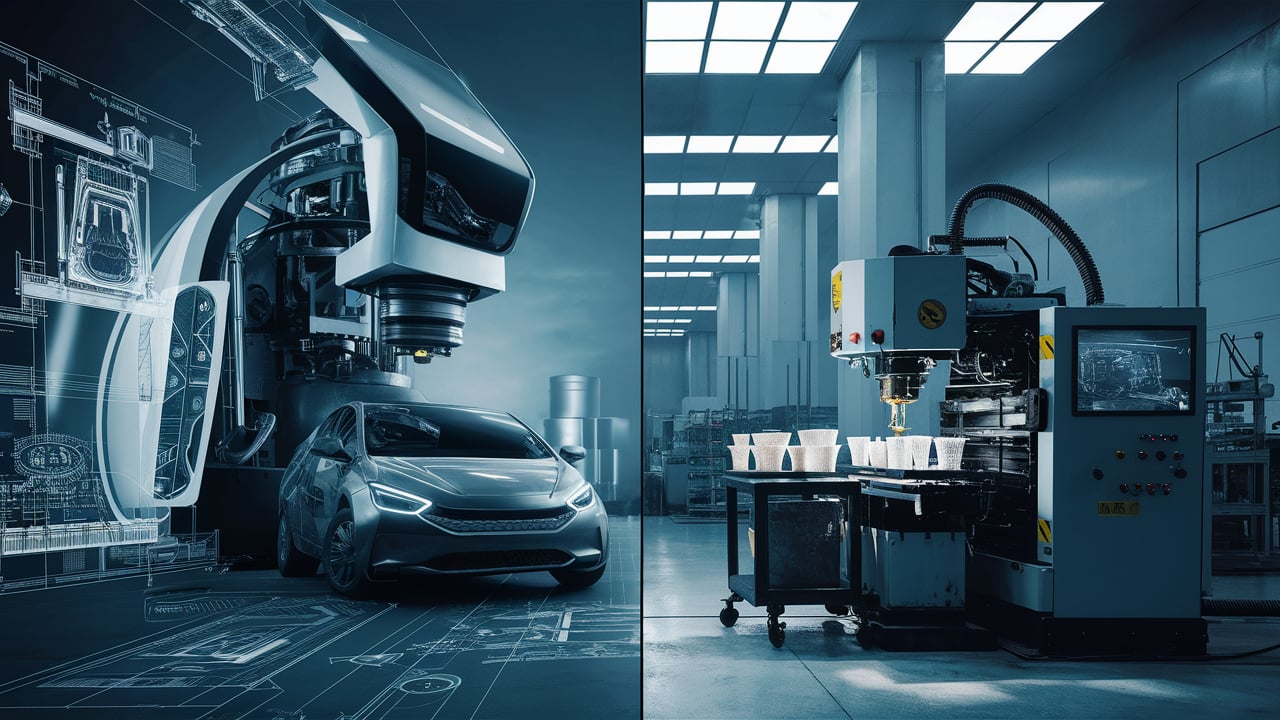
What is Large Part Injection Molding?
Let’s kick this off with some key terminology here. Traditional injection molding generally refers to machines that produce small components – think cell phone cases or food containers. Large part injection molding scales up for bigger components measured in feet rather than inches or smaller.
There’s no hard line where “large part” injection molding starts. But in general, molds over 3 feet in any direction would be pushing the “large” designation. Components over 1 cubic foot with thin walls less than 1⁄4 inch thick also require more specialized large part equipment.
Large part injection molding came into vogue in the 1980s as manufacturers figured out how to economically scale up the process for bigger and bigger components.
Today large part injection molding is right at home making:
- Pallets
- Crates
- Totes
- Car bumpers
- Kayak hulls
- Appliance housing
- Furniture
And much more. Essentially, if you need a big plastic component, large part injection molding is probably on the menu.
As far as the process itself, large part injection molding works similarly to traditional injection molding. Plastic pellets are gravity fed from an overhead hopper into the injection chamber. An extruder screw mixes and shears the material, heating it up into a liquid state.
When the plastic becomes molten, the screw rams forward, injecting the material at high pressures into the mold. The mold halves clamp together to prevent leaks as the material fills the open cavity.
After a cooling period, the mold separates and robotic arms with suction cups grab and tug out hardened plastic parts. The cooled parts drop down a slide into bins for packing and shipping or secondary finishing.
How Does Large Part Injection Molding Differ From Traditional Injection Molding?
While fundamentally similar, moving to large part injection molding requires several equipment tweaks and extra considerations versus traditional injection molding. Here are some of the key differences.
1. Tonnage
When it comes to injection molding, tonnage refers to the amount of clamping force the machine can exert. This force holds the mold halves together during injection to prevent leaks.
More surface area on the part sides means more total force required. As a rule of thumb, expect 1 ton of pressure for every square inch of projected area on the part.
Large part injection molding requires some seriously beefy machines to provide enough clamping force. Traditional injection molding machines often top out under 500 tons of pressure. Large part injection molding machines start around 500 tons, with the biggest monsters out there exerting over 4,000!
All that extra pressure requires heavy duty mold platens able to withstand the force without flexing plus beefier frames overall able to move and manipulate these heavy molds.
2. Mold Design
Another major difference comes from the much larger mold halves required for large part work. These massive chunks of machined steel take much longer to create.
A traditional injection mold might use blocks around 36 by 30 inches. Common large part injection molds often stretch 72 by 60 inches, with some even larger. Hand carving these cavities takes specialized equipment and much longer lead times.
Large part molds also tend to cost 5-10x more due to increased materials, machining, shipping, and handling requirements. Any small design mistake amplifies into huge quality issues down the road. Significant engineering work is mandatory for large part tool design.
3. Lead Times
Speaking of lead times, scheduling issues come into play here. Large part injection molding averages 16-20 weeks for mold completion after approving the design. Traditional injection molds often ship within 14 weeks.
It takes longer to carve these monstrous molds, including the specialized skills, machines, and materials handling equipment. Steel availability can also slow projects down if resources run short.
As always, if you can pay the premium, expediting services might squeeze 1-4 weeks out of the schedule. Just understand custom orders cause delays across all existing queue items already on the schedule!
4. Part Cost
With increased mold expenses plus beefier injection molding machinery needed, per-part cost goes up significantly with large part injection molding. However, secondary finishing steps often reduce.
For example, a traditional plastic part might need pad printing for branding or textures. Large plastic components often have these details molded right in.
I always recommend running detailed cost analysis breaking down per-part pricing. Make sure to factor in mold cost amortization, equipment expenses, secondary finishing reductions, shipment, taxes, and duties where applicable.
This holds true regardless of part sizes or quantities. But with large part injection molding, small cost differences per part become huge over production cycles of hundreds of thousands of units.
What Affects Clamp Force Requirements?
Figuring exact clamp tonnage requires advanced mechanical engineering calculations. However, three easy inputs provide a rough idea on requirements:
- Part Wall Thickness – Thicker walls need more pressure to fill without collapsing than thin-walled components
- Part Geometry – Simple shapes require less flow force than complex geometries with contours and angles
- Material Viscosity – High viscosity resins resist flow compared to low viscosity materials
Design tweaks altering any of these contributes to changes in injection pressure and clamp tonnage needs. Getting this wrong risks incomplete cavity filling plus flash leakage if pressure exceeds containment limits.
Conclusion
Fundamentally large part injection molding works like any injection molding process. However, unique equipment, extended lead times, and engineering considerations set it apart from traditional injection molding.
If you need big plastic components, understanding these key differences help set realistic expectations. Prepared project managers bypass potential pitfalls through proper planning and wise mold and machine section.
The world runs on plastic parts big and small. Whether traditional or large part injection molding, understanding your options provides the best opportunity for manufacturing success.
Now if you’ll excuse me, my Lego bricks need sorting – plastic parts don’t make themselves after all! Let me know if this helped explain large part injection molding differences in the comments. I’m always happy to chat manufacturing!