Injection molding is one of the most common and versatile manufacturing processes today. From electronics to medical equipment to consumer products, injection-molded plastic parts are in nearly everything around us. The process is fairly straightforward: plastic resin is melted under extreme heat and pressure into a liquid plastic, then injected into complex, closed metal molds to create intricately shaped parts.
Large part injection molding shares the same basic concept, but involves larger processes, equipment, and molds. Just like smaller parts, large injection-molded components require a delicate balance of dozens of different variables to produce a good part, from the formulation of the resin itself to the precise timing of the injection process. And when you’re working with larger volumes of plastic material, it becomes even more challenging to control and optimize the process.
A key metric of success for large part injection molding is the cycle time: the amount of time it takes from injecting the plastic into the mold cavities to ejecting the finished part and starting over again. Because plastic molding companies often make high volumes of parts, longer cycle times mean lower part outputs. And that can have major impacts on the part costs for customers who pay per component. For that reason, large injection molding companies are constantly working to trim cycle times as much as possible.
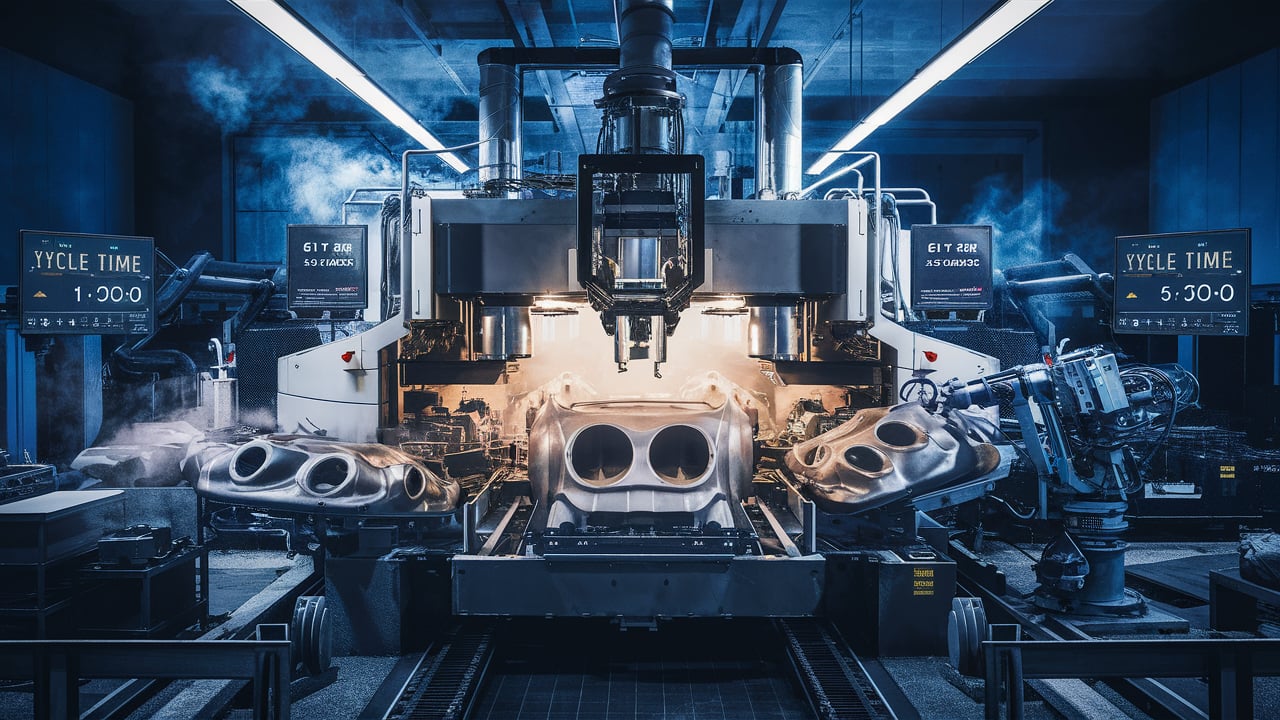
How to Reduce the Cycle Time of Large Part Injection Molding
When it comes to large part injection molding, there are opportunities to reduce cycle times starting from the earliest planning stages. Nearly every component of the process has an impact on part production throughput rates, from the molds themselves to the size of the machines. And each step can be leveraged through process optimization or advanced technology. Let’s take a look at some of the ways large injection molding companies are improving cycle times for massive plastic components.
Design With Cycle Times in Mind
Reducing large part injection molding cycle times starts with the part design itself. In general, the wider and thicker the walls and the overall dimensions of a plastic part are, the longer it will take to solidify. So the absolute best way to improve cycle times is to reduce wall thicknesses and the overall size of plastic components where possible.
Today’s computer-aided design (CAD) software provides far more advanced control of parameters to optimize the design early on.
For example, simulation software like Moldflow allows manufacturers to see how the plastic will flow within a virtual mold cavity and highlight potential problems. That means you can experiment with different wall thicknesses, gate placements, and part geometries— and evaluate the impacts on fill times and cooling rates—all within the software. This lets you make rapid design changes to minimize cycle times long before expensive steel molds are ever cut.
Design for Efficient Cooling
Cooling is by far the longest part of the injection molding process, so designing the mold for optimal heat transfer is paramount. Most large part molds incorporate internal cooling channels to circulate chilled water or oil and rapidly draw heat away from the part surface.
Modern cooling system design is extremely precise, allowing cooling channels to be placed extremely close to part features. And advancements in technologies like conformal cooling (which uses 3D printing to create curved channels that precisely match complex contours) provide opportunities for even faster cooling rates.
As a plastic part manufacturer, working closely with your injection mold designer to optimize cooling channel placement can yield major improvements in cycle time reduction.
Choose the Right Plastic Material
Choosing the right material formulation is another factor in improving large part injection molding cycle times. Properties like melt temperature (how hot the resin needs to be before it flows) and thermal conductivity (how quickly heat transfers through the plastic) can have an immense impact.
For example, an acrylic resin might require around 480 degrees Fahrenheit to melt and flow into the mold cavities. But nylon melts at a lower 420 degrees, and will solidify more quickly as well. These differences may translate into several seconds or even minutes shorter cycle times per part when you consider the immense amount of material in large injection molded components.
Consulting early on with your material supplier to select the ideal formulation for faster cycles is invaluable. And customizing the resin properties to your application can help as well.
Leverage Simulation Software
As touched on earlier, sophisticated simulation software provides immense value in designing parts and processes for faster injection molding cycles. Moldflow plastic injection molding simulation takes into consideration numerous variables and simulates the way resin will flow, cool, and solidify in the closed mold cavity.
For example, Moldflow allows you to experiment with different injection points, cycle variables (like melt temperature), and cooling channel setups to strike an optimal balance. You can evaluate the impacts on cycle variables like fill times, cooling rates, total cycle duration, clamp force requirements, and part quality—all within the simulation.
Virtual molding software cuts tremendous time and guesswork once production molds are manufactured. Most leading plastic injection molding companies leverage simulation tools in nearly every project.
Harness Process Monitoring Technology
Process monitoring systems that analyze sensor data from molds in real-time are immensely useful at optimizing the injection parameters that impact cycle times on large parts. These systems (like RJG Technologies eDART) monitor key variables throughout the injection molding process, collect data, and provide detailed molding analysis like fill pressure curves, injection velocities, and cooling rates.
This kind of feedback data allows process engineers to “microoptimize” all the process parameters that impact cycle times, like melt temperatures, injection speeds, pressures, and cooling rates. And for demanding applications like overmolded plastic components, process monitoring helps ensure part quality while cutting vital seconds.
Even small adjustments in variables like injection speed, mold clamping pressure and cooling time can result in significant productivity improvements over long production runs of massive plastic parts. The data transparency which process monitoring provides is indispensable for continuous improvement.
Invest in Faster Machines
With the immense clamping forces and injection pressures required to produce massive commercial parts, conventional plastic injection molding machines can sometimes become process bottlenecks.
Rather than trying to eke out every last bit of performance from aging equipment, many large part manufacturers choose to invest in state-of-the-art machines. Technologies like electric mold clamp drives (rather than hydraulic), multi-axis robotic arms and presses with immense tonnages provide the cycle speed increases necessary to remain globally competitive.
Large part molding involves major capital investments—so purchasing additional machines for higher volume production can be a smart long term investment to improve the bottom line. When evaluating the costs of new machines, always consider potential productivity improvements in your projections.
Implement Data-Driven Optimization
Ultimately, any plastic injection molding process has dozens of variables at play. So part quality and overall productivity improvements really come down to continuous data-driven optimization of the process. State of the art factories utilize process monitoring, automated data collection, simulation tools and data science to constantly fine tune process parameters.
When it comes to reducing injection molding cycle times for large parts, creating a smarter, more connected factory ultimately wins out. By systematically improving key variables like material fill/pack rates, cooling times and process parameters, plastic parts manufacturers drive higher outputs, better compliance and lower piece part costs over time. And advancements in machine learning and artificial intelligence make the injection molding process data more useful by the day.
Conclusion
There are always opportunities to enhance throughput and productivity in large part injection molding, starting from part design and selection of plastic resins all the way to factory robotics and analytics. Companies with expertise in scientific molding, material science, machine simulation and optimization are going to be the ones who excel.
The future factory will leverage every process sensor, material dataset and modeling tool to systematically drive incremental improvements in part quality, cycle times, yield rates and productivity. Large plastic part manufacturers who embrace digital transformation and connected factories will tap into continuous improvements that lift financial outcomes.
Effective cycle time reduction for large part molding requires a systems level approach across the value chain—from part design engineering all the way through the injection molding factory operations. But the substantial gains in part costs, productivity and revenues are well worth the investment.