Plastics manufacturing has come a long way in the last few decades. With continuous innovation and new technologies, we now have a variety of molding and forming processes to create all kinds of plastic products. Two of the most popular manufacturing processes are blow molding and injection molding. While both involve molding plastic, there are some key differences between blow molding and injection molding. As a professional injection molding manufacturer, I will share these differences in this post.
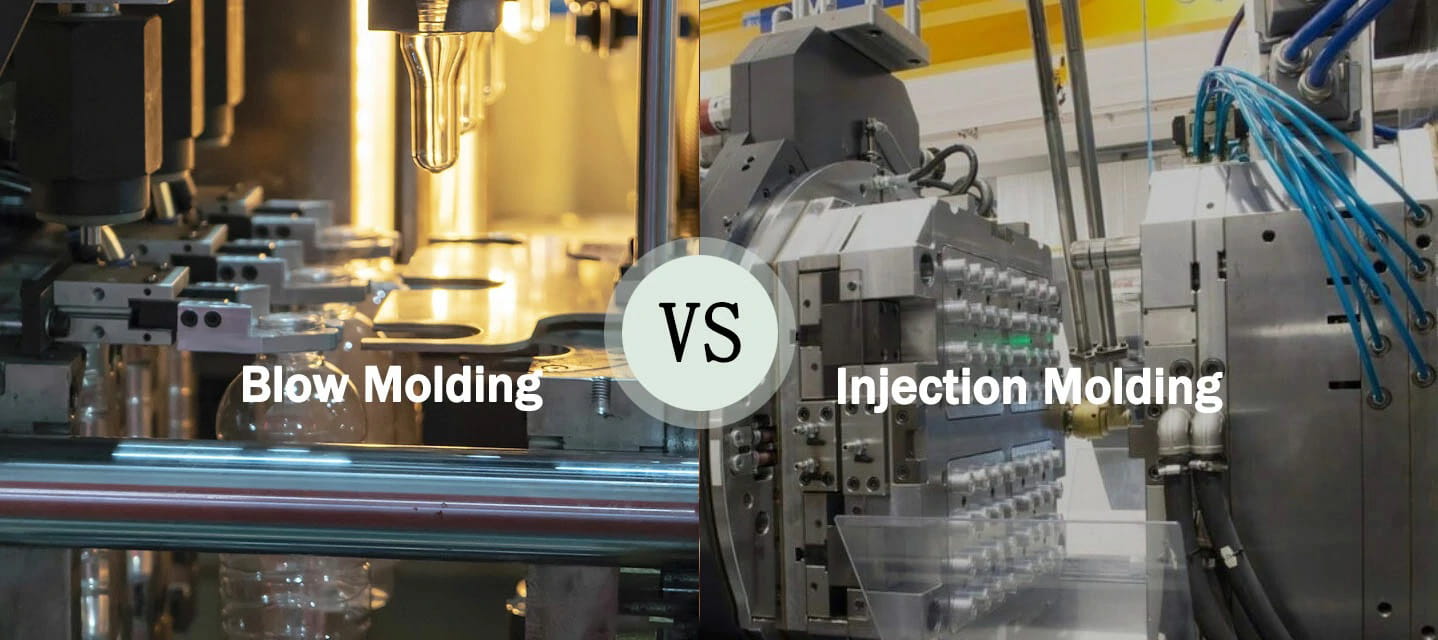
What is Blow Molding?
Blow molding is a plastic forming process used to create hollow plastic parts like bottles, containers etc. The blow molding process starts by heating up a thermoplastic material to make it pliable. The plastic is then extruded to create a tube-like structure called a parison.
This parison is then clamped into a mold and air is blown into it. As the air fills up the parison, it takes the shape of the mold cavity. Once cooled and hardened, the mold opens up and the plastic part is ejected. Trimming of excess plastic is done to get the final blow molded product.
Some benefits of blow molding are:
- Ability to create hollow parts and shapes
- Low cost of production
- Faster process compared to injection molding
- Variety of blow molding techniques available
Blow molding is commonly used to manufacture bottles, containers, tanks, toys, automotive ducts and various other hollow products. Materials like HDPE, PVC, PET etc. are commonly used for blow molding.
What is Injection Molding?
Injection molding is a manufacturing process in which solid plastic resins are liquefied and injected into a mold under high pressure. It solidifies into the shape of the mold after cooling.
In injection molding, plastic pellets are fed into a heated barrel. As they move forward, a rotating screw melts the pellets. When enough molten plastic collects, the screw moves forwards and injects the plastic into a closed mold under high pressures.
The mold is cooled constantly during this process so that the plastic solidifies quickly after injection. The mold then opens up and the molded part is removed. Intricate and precise parts with excellent finish can be created using injection molding.
Here are some benefits of using injection molding:
- Capability to manufacture intricate and detailed parts
- Excellent dimensional stability
- Wide range of plastic and metal alloys can be used
- Higher strength products compared to blow molding
- Automated mass production possible
Injection molding is used to make parts for various industries like automotive, medical, construction, electronics etc. Materials like polyethylene, ABS, nylon, epoxy etc are commonly molded using this process.
Blow Molding Vs Injection Molding
Now that we have understood the blow molding and injection molding processes independently, let’s compare these two popular manufacturing techniques.
Types of products
One of the main differences between blow molding and injection molding is in the types of products each process can manufacture economically.
Blow molding is ideal for making hollow objects like bottles, cans, containers etc. The process allows for flexibility to manufacture various hollow shapes and sizes. Due to the hollow forms, walls of blow molded objects are quite thin as well.
Injection molding on the other hand, excels in manufacturing solid and intricate parts. From small plastic components to complete body panels of cars, injection molded parts have excellent finish and sturdiness. The molds and forming pressures give great precision and complex geometries can be achieved.
Speed and volume of production
Both blow molding and injection molding can deliver high production speeds and volumes. But injection molding allows much faster cycle times due to the high pressures involved. Parts solidify quicker inside the temperature regulated molds, reducing production time per part significantly.
Blow molding cycle times can vary depending on the size of the product. Formation of larger hollow products takes more cooling time which increases overall cycle time. But smaller products can be churned out rapidly from blow molding machines as well.
Multi-cavity molds allow running multiple operations in parallel for both types of molding. This drastically improves production volumes without affecting cycle times. In terms of numbers, injection molding produces faster volumes, but large-scale blow molding manufactures at rapid speeds as well.
Cost implications
Injection molding equipment and running costs are generally higher than blow molding. Much tighter process control, complex molds, high-pressure injection systems contribute to its overall expenses per unit. But injection molding also minimizes material waste and manual labor required post-production.
The cost of blow molding equipment and tooling is significantly lesser in comparison. This establishes blow molding as an economical process for creating simple hollow plastic objects cost-effectively even in higher quantities. Additional finishing procedures may be needed for products from blow molding.
For small batch production, injection molding proves more economical while high-volume manufacturing tilts the scale towards blow molding. But specific product requirements must also be factored for determining cost-effectiveness.
Part complexity
Design complexity is not an issue with injection molding. Intricate shapes, fine details, close tolerances can be achieved by precision machined molds. The high pressure injecting molten polymer evenly into every crevice of such molds gives excellent surface finish.
The malleable hollow blow molded forms do not lend themselves to such fine details or geometric complexities as injection molding. Most products from blow molding have relatively simple surface features without fine details or accuracy.
Material Suitability
A variety of metals and plastic polymers can be used with injection molding. Engineering grade materials like ABS, acetals, nylon etc can be molded into strong solid parts via injection molding. Materials like silicone, epoxies, composites can also be molded using this process.
Blow molding works well with amorphous polymers like HDPE, LDPE, PET which form parisons easily and set into lightweight hollow profiles. Recently, more advanced polymers are also being used in structural blow molding applications. But the range still falls short of injection molding plastic & metal alloys usage.
Quality Control
Consistent product quality is much easier to control with injection molding. The closed metal molds and precise reproducible process parameters in injection molding ensure minimal defects. Automation also allows keeping tight oversight in injection molding.
Although tooling and processing for blow molding has improved vastly, there still lies variability in material thickness and properties of the final products. Additional testing may be required to ensure quality consistency from blow molding. The process by nature has certain limitations allowing defects unlike injection molding.
Design & Tooling
Tooling includes mold cores, cavities, ejection systems – basically components affecting the final plastic product design and finish. Injection molds are machined to fine precision out of metals to handle the high pressures and temperatures during the process. They cost quite a bit to manufacture but give excellent part consistency.
Blow molding mostly relies on the mold material, typically steel, and air pressure to create the hollow plastic shape. Much simpler molds without complex cores, slides etc. are needed which significantly reduces tooling costs in blow molding.
Summary: Choosing Between Injection Molding vs Blow Molding
Parameters | Injection Molding | Blow Molding |
---|---|---|
Types of products | Intricate solid parts & products | Hollow lightweight bottles, containers |
Production speed | Very high | High |
Initial investments | High | Low to moderate |
Running costs | High | Low to moderate |
Part complexity possible | High | Low |
Typical industries | Automotive, appliances, electronics | Packaging, toys, fuel tanks |
Both injection molding and blow molding have their own set of advantages suiting different applications. With the help of the above comparative analysis, engineers can select the right manufacturing process for developing quality plastic products matching their specific needs in 2024 and beyond. Reach out to vendors or manufacturers of plastic injection and blow molding equipment for more insights on each process.
Blow Molding vs. Injection Molding: Which one is better in 2024?
In a nutshell, if you need to manufacture solid intricate parts rapidly in large volumes, utilizing advanced plastics with excellent consistency, accuracy and surface finish – injection molding suits your needs perfectly in 2024.
If your needs are cost-effective manufacturing of hollow lightweight bottles, containers, ducts, cans in medium to high volumes – blow molding checks all boxes as the ideal 2024 plastic forming process choice.
The advances in polymers, automation and competitive molding equipment pricing has made both injection molding and blow molding easily accessible for businesses of all scales. Leverage the unique strengths of each plastic molding technique in 2024 for increasing productivity and profitability!