In molding industry, some people may want to know about manufacturing processes like compression molding and injection molding. They want to know which method is better for creating plastic parts and components.
Both techniques have their advantages, but is one clearly superior overall? Based on my research, there is no definitive “winner” between compression vs injection molding. The best process depends significantly on factors like:
- Part geometry complexity
- Production volumes
- Materials used
- Cost considerations
In this guide, as a professional injection molding manufacturer, I’ll compare compression molding and injection molding across these key attributes. My goal is to help you determine the ideal technique for your specific application. Let’s dive in!
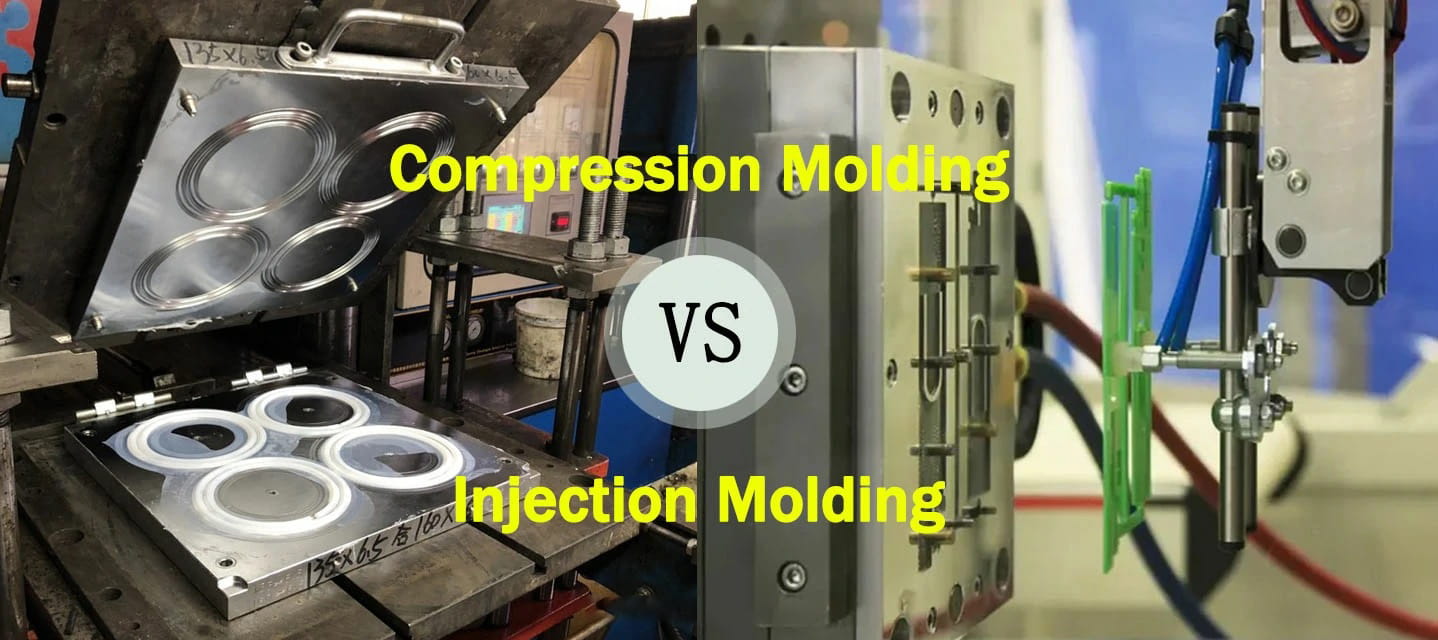
How Compression Molding and Injection Molding Work
Before comparing compression vs injection molding, it helps to understand what each entails. Both processes shape plastic resin using heat, pressure, and specially designed molds. But the way the materials enter the mold differs:
Compression Molding
This technique preheats a mold cavity, then places a pellet or powder resin into the cavity. Next, the mold halves close and apply heat and direct pressure to force the material to conform to the mold. Once cured, the molded part gets ejected.
Compression molding works well for less complex components using thermoset materials with high viscosity flow properties. It allows flexible part geometries.
Injection Molding
In this process, plastic granules get fed into a heated barrel. As they are slowly pushed forward by a reciprocating screw, the material melts. Once enough molten plastic accumulates, the screw injection occurs, forcing resin into the closed mold cavity under intense heat and pressure.
After adequate cooling time, the mold opens and robotically ejects the solidified part. Injection molding enables intricate parts and lends itself to automation, but has higher tooling costs.
Now let’s analyze how these fundamental differences impact compression molding vs injection molding across several key factors.
Compression Molding vs Injection Molding
Complexity of Part Geometry
A primary point of comparison between compression and injection molding is complexity of permissible part geometries.
Injection Molding Geometry Complexity
This process can manufacture intensely complex and detailed component shapes. That includes parts with delicate features, thin walls, dimensional accuracy requirements, and complex curvatures.
Injection molding’s high-pressure injection phase literally forces material to flow into every crevice of intricate molds. This enables remarkably complex parts.
Compression Molding Geometry Complexity
Conversely, compression molding does not employ a high-pressure fill phase. So materials like thermoset plastic and rubber do not force themselves into highly complex mold cavities.
Therefore, compression molding cannot achieve the same part complexity possible with injection molding. Acceptable part shapes are less sophisticated, usually involving basic geometries and smooth contours. Sharp corners and steep draft angles should get avoided.
If an application requires intricate details and complex three-dimensional contours, injection molding is likely the better process choice.
Typical Production Volumes
Another key difference between compression molding vs injection molding relates to practical production volumes each process accommodates.
Injection Molding Production Volumes
This method is ideally suited for large production runs generating hundreds of thousands or millions of finished parts. The primary reason is automation – injection molding leverages programmable machines and robots that dramatically heighten process efficiency.
Although low-volume injection molding production is also possible, it becomes more expensive per part. But overall, no technique rivals injection molding for sheer manufacturing throughput capabilities.
Compression Molding Production Volumes
Compression molding output volumes typically fall within a lower to medium quantity range. Without the high level of automation that injection molding employs, compression molding remains labor-intensive by comparison.
While multi-cavity molds can somewhat increase parts yield, compression molding overall lacks theextreme scalability of injection techniques. As production needs expand exponentially, this approach loses cost competitiveness.
In summary, injection molding accommodates orders of magnitude higher production volumes than compression molding realistically can.
Molding Materials Used
These two methodologies also differ regarding compatible plastic molding materials for manufacturing finished components:
Injection Molding Materials
This process works very capably with standard thermoplastic resins such as ABS, nylon, polyethylene, polypropylene, polystyrene and similar widely-used mainstream plastics. Certain thermoset polymers are also injection moldable using specialized machinery.
Thermoplastics melt uniformly, flow readily into mold cavities, then re-solidify nicely upon cooling. This makes them ideal resins for injection molding processes.
Compression Molding Materials
Common materials molded under compression include thermoset polymers such as SMC,BMC, epoxy,diallyl phthalate and phenolic resins. These all cure and harden irreversibly when heat gets applied.
Compression molding also manufactures parts from elastomeric substances like silicone or natural/synthetic rubber. Such high viscosity materials with poor melt flow properties are often compression molded out of necessity.
In summary, material suitability considerations for compression vs injection molding tend to differ substantially. But some thermoplastics like HDPE work with either process.
Cost Comparison Between Methods
When examining compression molding and injection molding, few points require more careful evaluation than project cost estimations and comparisons:
Injection Molding Cost Considerations
Upfront expenses for injection molding tools and equipment easily run $50,000 to $100,000+ for a full production cell. Such high tooling costs only make economic sense given injection molding’s immense volume capabilities.
However,for a given part complexity, per-unit costs drop proportionally as production numbers rise. This makes injection molding highly economical for large part quantity scenarios.
Compression Molding Cost Considerations
Mold tooling for this method is simpler and costs notably less than injecton mold counterparts. Initial machine capital outlays are also lower for equivalent capacity compression molding equipment.
This process favors more modest production goals in the tens or hundreds of thousands of lifetime parts molded. Despite longer per-part cycle times, compression molding costs remain quite competitive within this reduced output range.
When evaluating compression vs injection molding costs, both fixed and variable expenses must get carefully analyzed against projected manufacturing volumes to determine ideal process economics.
Key Differences Summary
To recap, here are some of the main trait comparisons between compression molding vs injection molding manufacturing methods:
Compression Molding Summary
- Lower tooling and equipment costs
- Limited to basic part geometries
- Uses thermoset polymers/rubbers
- Lower to medium production volumes
- Labor participation remains essential
Injection Molding Summary
- Far higher tooling and equipment expenses
- Highly complex part geometries achievable
- Most thermoplastics can get molded
- Massive production scalability
- Extensive automation integration
Which Process is Better For Your Project?
Whether injection molding vs compression molding offers the better fit depends greatly on your application’s specific requirements and business objectives.
For very high production goals or intricate precision parts needing tight tolerances, injection molding provides distinct advantages. The process also affords more material options for plastics part manufacturing.
However, for lower-volume projects using rubbers or thermosets with basic shapes, compression molding makes good sense economically. Just match methodology carefully against each key attribute for an informed determination!
Hopefully this overview gives you greater perspective regarding compression vs injection molding process comparisons. Please let me know if you have any other questions! I look forward to helping you determine the ideal production technique for your upcoming project.