Urethane casting and injection molding are two of the most common manufacturing methods used to produce plastic parts at scale. But with different capabilities in terms of volume, cost, speed, precision and more, how do you know which process is right for your specific product?
In this comprehensive guide, as a professional injection molding manufacturer, we’ll compare urethane casting vs injection molding across a number of factors. By the end, you’ll understand the strengths and limitations of each approach so you can make an informed decision for your manufacturing needs in 2024 and beyond.
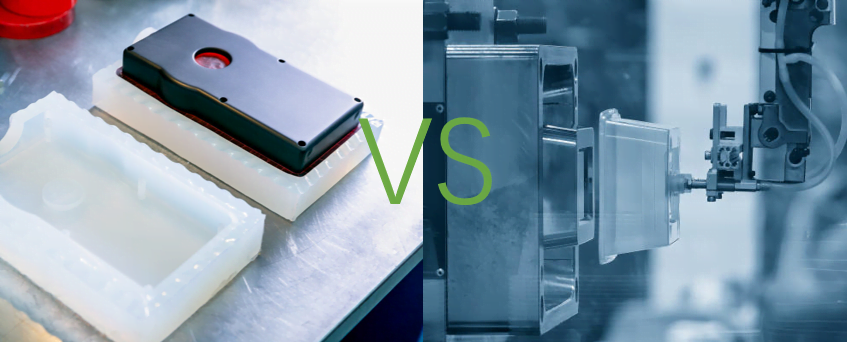
Overview of Urethane Casting
Urethane casting is a process where liquid urethane resin is poured into a silicone mold and cured, either at room temperature or with heat. It’s commonly used for prototypes, short-run production, and to bridge the gap between prototyping and high-volume manufacturing with injection molding.
The process starts with a “master pattern” – essentially a detailed model of the final part created via CNC machining or 3D printing. This pattern is then used to create the silicone mold that the resin will be poured into.
Once cured, parts can be post-processed with techniques like painting or sanding to achieve certain finishes or enhanced functionality. Let’s explore some of the key benefits and downsides of urethane casting:
Advantages
- Lower startup costs: Silicone molds are significantly cheaper than steel/aluminum injection molds
- Faster iteration: New molds can be made in just days/weeks rather than months
- Design flexibility: Better supports complex geometries, undercuts
- Smaller volumes: Ideal for prototyping plus short runs from 1-100 units
- Material options: Wide range of urethane formulations available
Disadvantages
- Larger volumes: Silicone molds deteriorate faster than injection molds
- Consistency: More variation part-to-part, especially over long runs
- Choices limited: Mostly thermoset polyurethane materials available
Now let’s look at injection molding and how it stacks up.
Overview of Injection Molding
Injection molding uses metal molds and high heat/pressure to produce plastic parts to extremely tight precision and at large volumes. Materials like ABS, polypropylene, and other thermoplastics are injected in a molten state then cooled rapidly within the mold.
The process requires extensive design and machining of the steel or aluminum molds prior to production. This makes tooling costs high (often tens of thousands of dollars). However, these durable molds enable extremely high part volumes once up and running.
Advantages of injection molding:
- High-volume production: Output can be in the millions of units
- Consistency: Very repeatable results part-to-part
- Precision: Tolerance down to 0.005 inches achievable
- Material choice: Many advanced thermoplastics available
- Automation: Highly efficient process once running
Disadvantages:
- Initial costs: Very high tooling expense
- Lead times: Several months from design to production
- Design limitations: Changes require new molds
- Lower volumes: Becomes pricey at <10k units
Now that we understand both processes better, let’s directly compare some of their key attributes.
Urethane Casting vs Injection Molding
To determine which method – urethane casting or injection molding – makes more sense for a product, here are some of the most important factors to consider:
Production Volumes
- Urethane Casting: Typically used for volumes of 1-100 units. Labor-intensive process makes higher volumes expensive.
- Injection Molding: Output can range from 100 units into the millions. Automated process means cost/part drops significantly at scale.
If you require small batches or limited production runs, urethane casting is likely the better fit. But for mass production volumes, the consistency and cost efficiency of injection molding can’t be matched.
Lead Times
- Urethane Casting: Rapid prototypes possible in 1-2 weeks; end-use parts in 3-4 weeks
- Injection Molding: 4-6+ months from product design through production
Urethane casting enables validation of concepts much faster through rapid prototyping. If speed-to-market is critical, look to urethane first before transitioning to injection molding at higher volumes.
Costs
- Urethane Casting: Lower mold costs ($100s-$1000s) but higher per-part cost at low volumes
- Injection Molding: Far higher tooling costs but cost per part drops sharply at mid+ volumes
For short runs where few parts are required, the lower startup costs of urethane casting make far more economic sense. But amortized over 100k, 500k+ units, injection molding delivers better economies of scale.
Part Size
- Urethane Casting: Generally smaller components up to roughly 5 lbs
- Injection Molding: Capable of producing much larger parts of up to 50 lbs+ in weight
If dimensions allow, injection molding enables higher consistency and accuracy in large part sizes unavailable through urethane casting methods.
Tolerances
- Urethane Casting: +/- 0.010 inch (for the 1st inch) down to +/- 0.005 inch typical
- Injection Molding: As precise as +/- 0.002 inch achievable
For assemblies requiring extremely tight fit, form, and function, injection molding and its industry-leading precision is likely the better route.
Design Complexity
- Urethane Casting: Supports complex geometries and surface details easier
- Injection Molding: Design changes require entirely new molds
If exploring iterative changes around complex shapes, undercuts, etc. urethane casting can adapt quicker through minor tooling tweaks rather than re-machining from scratch.
Finishing
- Urethane Casting: Requires secondary processes like sanding, painting, etc.
- Injection Molding: Finishes replicable directly within mold
For products where appearance matters most, injection molding can achieve higher-quality finishes direct from the initial molding process. But urethane casting also reaches excellent visual results with some additional refinement.
Key Takeaways: Choosing What’s Right for You
Deciding between urethane casting vs injection molding requires thoroughly analyzing multiple factors from production volumes to timelines to costs and design intent.
While injection molding makes the most sense for mass manufacturing of high precision parts, urethane casting enables rapid iteration early on and can more affordably produce smaller batches.
Focus on what matters most around quality, capabilities and budget for your specific product. By fully understanding the manufacturing implications, you’ll be best positioned to choose a process that transforms your vision into reality.