Molding the right plastic is crucial to creating durable, functional parts. That’s why getting injection molding material selection right is one of the most important (and confusing) steps of the entire manufacturing process.
In this complete guide, as a professional plastic injection molding manufacturer, I’ll will share answers to all of your most burning injection molding material questions like:
- What are the most common injection molding materials? And what are the pros and cons of each (so you can choose the right one)?
- What key characteristics should you look for when browsing through material data sheets?
- How do you make sure that you choose an injection molding material that meets strict medical and food compliance regulations?
- And way, way more.
Let’s get to it!
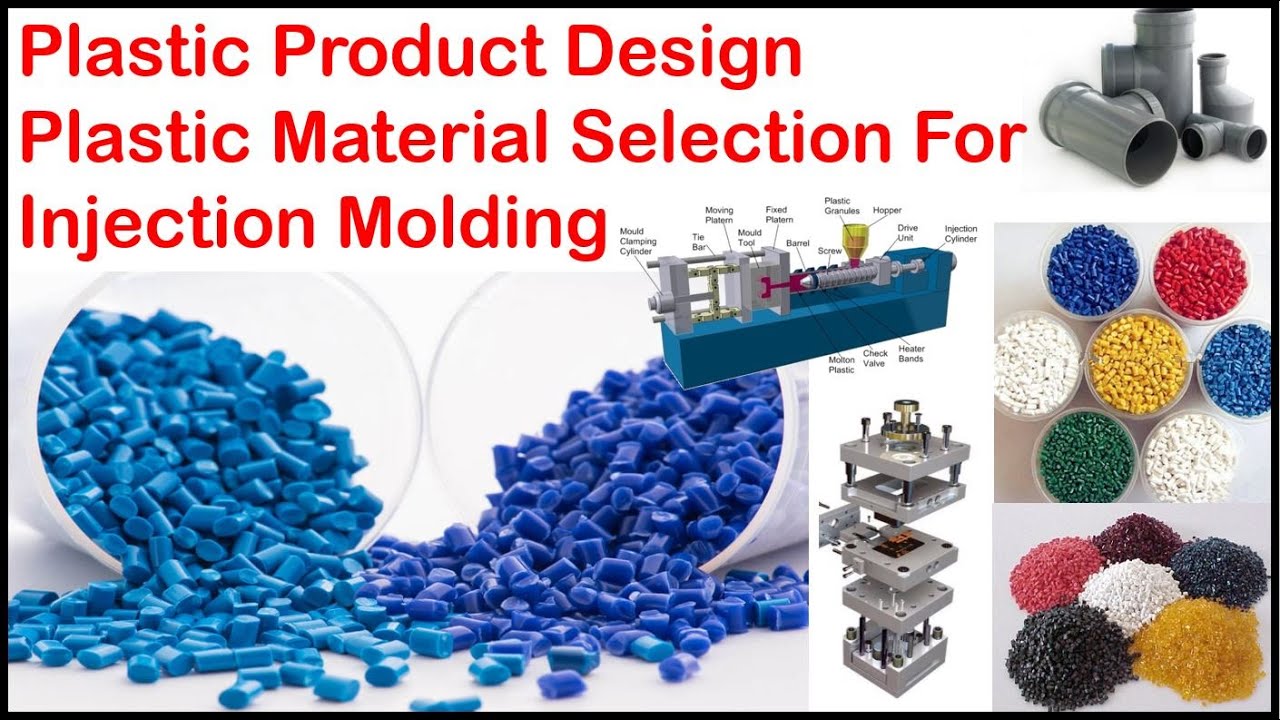
Common Injection Molding Materials (With Applications)
Here’s a quick rundown of the most frequently used injection molding materials in 2024, along with the types of products that they’re best suited for:
1. Acrylonitrile Butadiene Styrene (ABS)
ABS is an engineering thermoplastic that is equal parts durable, dimensionally stable AND affordable. Perfect for injection molding complex parts.
Best for: automotive trim components, sporting equipment, musical instruments, LEGO bricks
2. Polypropylene (PP)
Polypropylene (PP) strikes an unbeatable balance between very high rigidity and fatigue resistance…at a very low material price point.
Oh, and PP has first-rate chemical resistance properties and dampening qualities.
Best for: food containers, laboratory equipment, automotive components, hinges
3. Acrylic-Polymethyl Methacrylate (PMMA)
PMMA (acrylic) is crystal clear, rigid and remarkably shatter-resistant. It’s also FDA compliant, making acrylic the material of choice for medical devices and scientific ware.
Best for: lenses, transparent surfaces, sanitary ware, illuminated signage
Critical Factors To Consider When Selecting Materials
Okay, so now you know the most popular injection molding materials used today. But how do you figure out which plastic resin is the RIGHT material for your particular application?
Here are the 6 essential factors to keep top of mind during the material selection process:
Strength + Durability Requirements
Will your part undergo any physical stress during regular use? If so, pay close attention to elongation/tensile material properties to ensure that your plastic can withstand applied loads without cracking.
Pro tip: opt for a glass or carbon fiber reinforced material (like nylon or PBT) for the ultimate durability.
Thermal Considerations
What environments will your component be exposed to? Freezing Arctic temps? Sweltering heat?
Compare the maximum service temperature of prospective resins to anticipated operating conditions to prevent material failures.
Dimensional Stability Specs
Dimensional precision paramount? Then dimensional stability should be a main evaluation criteria during injection molding material selection.
As a rule of thumb, amorphous plastics (ABS, PC, PMMA) hold tighter tolerances than semi-crystalline materials.
Target Cost Per Part
Run a cost analysis early on to determine $/part thresholds based on production volumes. High-performance polymers can run $25+ per pound…so keep budget limitations in mind.
Pro tip: consult with your injection molder, as changing tooling parameters can reduce material costs substantially.
Production Efficiency Requirements
Certain materials flow better than others, minimizing knit lines and short shot occurrences. Discuss gate location preferences and tooling tweaks with your molder to boost efficiency.
Compliance Considerations
Using a resin that is FDA/EU compliant is non-negotiable for food contact products and medical devices. Many common plastics (like PET or PP) have compliant grades available.
Research regulatory standards upfront to avoid costly reworks.
How To Select The Right Injection Molding Material (Step-By-Step)
Choosing a plastic resin seems easy enough…until you actually start evaluating options!
To take the pain out of injection molding material selection, follow this 5-step system:
Step #1: Define “Must-Have” Requirements
Start by making a list of absolutely essential performance characteristics and operational requisites based on part function.
For example, does your component need to withstand boiling water? Support a 10 kg load? Or pass certain outgassing criteria?
Building this “must-have” list first significantly narrows the playing field.
Step #2: Determine “Like-To-Have” Properties
Next, make note of useful (but non-critical) properties that would optimize functionality, durability and end-user experience.
Like resistance to certain chemicals. An anti-static surface. Or self-lubricating qualities.
Jot down 4-5 “like-to-have” attributes (in priority order).
Step #3: Browse Material Categories
Now, browse plastic resin categories that meet essential requirements, starting with thermoplastics:
- Commodity resins: PP, PE, PS, PVC
- Engineering thermoplastics: PC, ABS, nylon, acetal
- Advanced engineering resins: PEEK, ULTEM PEI, PPS
Evaluate whether amorphous, semi-crystalline or elastomeric materials best fit the application.
Step #4: Research Top Contenders
Next, dig into the fine print on technical data sheets for promising material candidates.
Scrutinize key performance metrics like tensile modulus, flexural strength, impact resistance, HDT, chemical compatibility, etc. against specifications.
Step #5: Order Samples
Finally, ask your molder for molded samples of one or two top contenders to test firsthand.
Evaluating functional prototypes will prove out whether an injection molding material can successfully stand up to real-world conditions.
Finding The Right Material Partner For Your Project
At the end of the day, ASKING FOR HELP is my #1 tip for painless injection molding material selection.
Why (fruitlessly) try to become an overnight injection molding material expert when you can lean on people that live and breathe this stuff?
From day one, I HIGHLY recommend partnering with an experienced injection molder who provides complimentary material guidance.
Here’s what to look for in a superb injection molding material partner:
- Detailed material expertise from real production experience (not just data sheet regurgitation)
- Documented validation protocols proving out whether resins meet requirements
- Material sampling services to test top candidates firsthand
- Guidance around material compliancy limitations
Finding an exceptional injection molding partner simplifies what is otherwise an overwhelming material selection process.
So don’t hesitate to lean on industry experts. The collective brain trust will fast-track your path to the perfect injection molding material for YOUR unique application challenges.