Injection molding is one of the most common manufacturing processes used to produce plastic parts and products at scale. But how can you actually tell if an item was made using this method?
As a professional plastic injection molding manufacturer, I will share some clear signs to look for that indicate injection molding. Being able to identify these markers can help you determine how a product was fabricated and gain insight into its quality and construction.
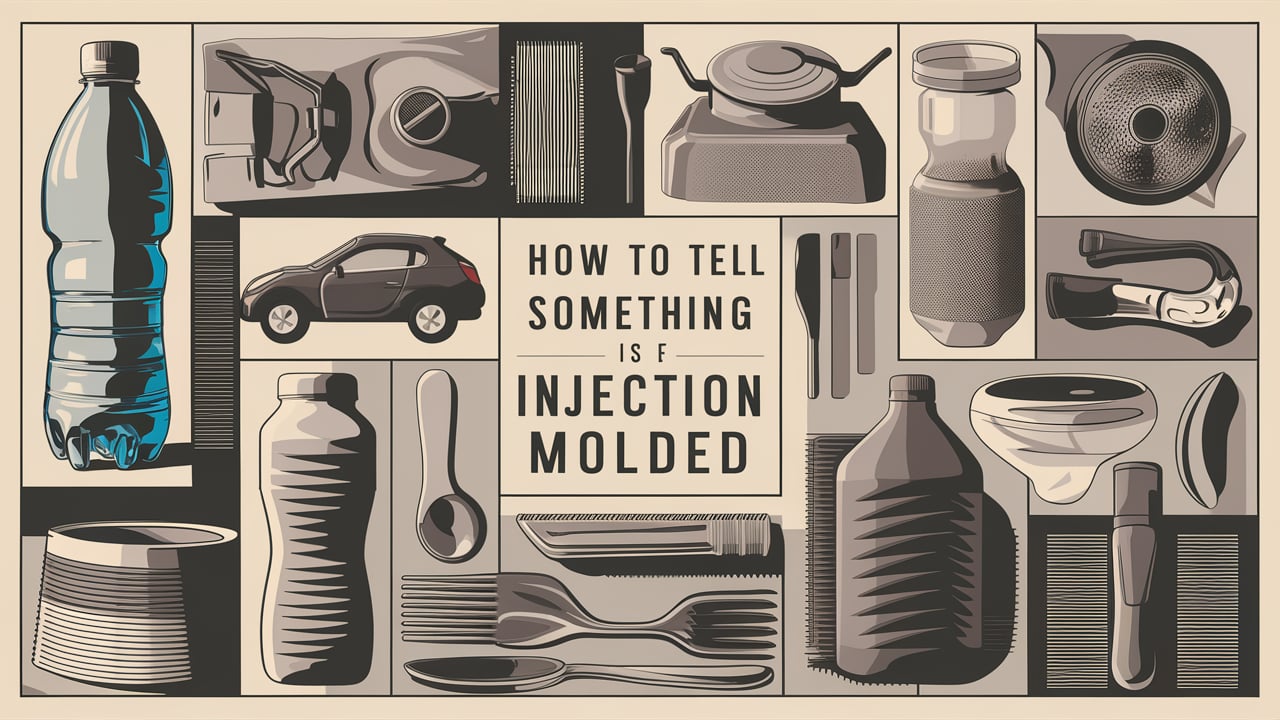
Examining Parts for Evidence of Injection Molding
When taking a closer look at a plastic part to determine if injection molding was used, there are three key things to look for:
Parting Lines
A parting line is perhaps the clearest indicator that a plastic product was injection molded. This is a visible seam running along the surface of the part where the two halves of the injection mold separated.
As the molten plastic cools and hardens within the mold, it retains an outline of where the two mold halves met before opening to eject the solidified part. This leaves a line, often faintly visible upon close inspection.
Parting lines may run along the outer edges of a part or be found bisecting its surface where splits in the mold occur. Their prominence can vary based on factors like mold precision and plastic used.
Under magnification, parting lines become more readily visible. Their presence is a strong confirmation that injection molding fabricated the component.
Gate Marks
Gate marks signify where molten plastic entered the mold cavity during the injection process. They manifest as small vestiges on the molded part surface once the gate is removed after solidification.
Gate marks are typically subtle and may be spotted as a small raised bump or slight depression in the plastic. Oftentimes they are purposely placed in inconspicuous locations, like hidden faces or edges, to minimize aesthetic impact.
The gate vestige appearance and size can differ based on gate design. Pinpoint gates leave tiny marks while edge gates may leave larger, more visible remnants. Gate marks require close inspection but often can confirm injection molding manufacture.
Ejector Pin Marks
Ejector pin markings result from the pins that eject cooled, molded parts from the mold. Usually small and round or rectangular, these indentations mark where pins pushed the part out upon opening the mold.
They are found on surfaces that contacted the mold itself while cooling and hardening. Ejector pin spots are recognizable by their uniform appearance and distribution corresponding to the pin layout.
The impression depth and definition varies, based on factors like mold complexity and plastic choice. Numbers or codes are sometimes molded via these pins for tracing IDs. Magnification helps spot these marks.
Their presence undoubtedly signifies the part was injection molded and ejected using these mechanisms.
Other Methods to Confirm Injection Molding
Beyond analyzing the physical part for marking evidence, there are some other ways to determine if injection molding produced a plastic component:
- Check part complexity – Injection molding economically fabricates elaborate, detailed plastic parts unachievable with other methods. If a part has complex geometries impossible through basic machining, there is a very strong likelihood it was injection molded.
- Identify non-uniform wall thicknesses – The injection molding process readily accommodates variances in wall thicknesses across a single part. This is very difficult to achieve otherwise with plastic. Unique thickness dimensions suggest injection molding.
- Material properties – Certain plastics like engineering-grade thermoplastic resins are primarily processed via injection molding, due to the capabilities required. Identifying one of these materials indicates this method was utilized.
- Manufacturer certification – Part suppliers will often specify the manufacturing technique implemented, typically injection molding. Sourcing this confirmation can reliably verify fabrication process.
Benefits of Identifying Injection Molded Parts
Being able to conclusively identify injection molded plastics is useful across many domains and applications. Beyond mere technical curiosity, there are some significant benefits this knowledge delivers:
- Quality assurance – Recognizing parts formed via injection molding provides confidence regarding consistency and performance, based on industry standards. This aids quality control.
- Design assessments – Observing molded part details gives clearer understanding around production limitations, useful when assessing new applications. It focuses possibility evaluations.
- Process validations – Certifying vendor fabrication methods through in-house verification of injection molding builds better supplier relationships via process corroboration.
- Forensic analysis – In failure investigations, positively confirming manufacturing methods provides systemic insights unavailable otherwise. This greatly bolsters root cause determinations.
In 2024 and beyond, properly assessing fabrication approaches remains key in plastics-based industries. Identifying injection molded components through detailed molded-in characteristics, plastic traits, and manufacturer disclosures helps deliver these critical quality, design, and performance assurances across global markets.