Can PETG be injection moulded? Yes, PETG can absolutely be injection molded. In fact, injection moulding is one of the most common and effective manufacturing processes for working with PETG plastic.
PETG, which stands for polyethylene terephthalate glycol-modified, is an excellent thermoplastic for injection moulding applications requiring high clarity, strength, chemical resistance and durability. Its ability to be injection moulded into complex geometries makes it suitable for diverse products across medical, electronics, packaging and consumer industries.
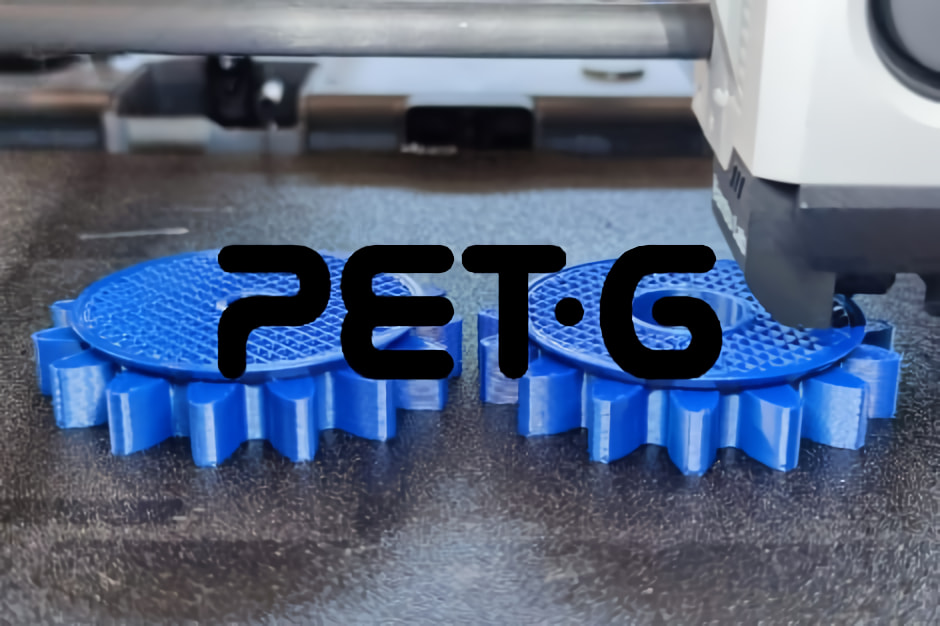
What is PETG Plastic?
Before diving into PETG injection moulding, it’s important to understand what exactly PETG plastic is.
PETG is a co-polyester – a modification of the commonly known PET (polyethylene terephthalate). It’s produced by adding a glycol during the polymerization process, which introduces irregularities into its molecular structure.
This molecular structure modification gives PETG some advantageous characteristics over regular PET:
- Higher impact strength and ductility
- Enhanced chemical resistance
- Excellent clarity and light transmission
- Easier processing and lower molding temperatures
- Wider processing window
Essentially, PETG combines excellent processability and optical clarity with enhanced mechanical performance versus standard PET. This unique balance of properties of this engineering thermoplastic makes it suitable for a wide range of injection molding applications.
Can PETG Be Injection Molded?
Yes, PETG can absolutely be injection molded to create complex, transparent parts for diverse applications. In fact, injection molding is among the most common and cost-effective manufacturing processes for working with PETG plastic.
The thermoplastic nature and melt-flow properties of PETG makes it an excellent candidate for injection molding. PETG easily flows into complex mold geometries and cures into durable end-use products.
PETG Injection Molding Applications
Thanks to its well-balanced performance portfolio, PETG is used across many industries to produce injection molded parts. Some common applications include:
Medical and pharmaceutical products – Clear clamshell packaging, trays,custom medication bottles, blood sample tubes.
Food packaging – Clear containers and lids for various food items. Provides an excellent oxygen and carbon dioxide barrier.
Electronics – Lighting components, insulators,clear covers and cases.
Displays – Brackets, stands, housings with excellent clarity.
Consumer goods – Household items, toys, decorative objects.
Essentially any application requiring good strength, clarity, chemical resistance combined with the ability to injection mold intricate geometries can benefit from PETG plastic.
Its versatility and wide processing window makes it an economical choice versus other clear plastics for producers looking to injection mold transparent parts.
PETG Injection Molding Process Overview
The basic injection molding process for PETG consists of three main steps:
1. PETG plastic pellets are gravity fed from a hopper into the injection molding machine’s barrel.
The barrel is heated to melt the PETG into a liquid state that can easily flow into mold cavities.
2. The molten PETG is injected at a controlled rate and pressure into the injection mold.
The two halves of the mold are held together under pressure to prevent material leakages. The PETG takes the shape as it cools and cures inside the mold.
3. Once cured, the mold separates and the injection molded PETG part is ejected out. The sprues and runners – excess cured plastic from the mold – are trimmed off the part.
After ejection, some additional post-molding secondary operations may be performed as well. This includes decorating, branding or assembling multiple plastic parts together.
This completes a single molding cycle. The structured repetition of this process allows mass production injection molding of many thousands of PETG parts.
Key PETG Injection Molding Process Guidelines
While conceptually simple, successful injection molding requires careful process control between multiple interdependent parameters.
Here are some key processing guidelines specific to PETG injection molding:
- Moisture control – PETG is hygroscopic and absorbs ambient moisture. Parts molded from undesired moisture levels can have visual defects and reduced mechanical performance. PETG requires properly drying to moisture levels below 0.04% prior to molding.
- Melt temperature – Too low of a temperature can lead to incomplete melting and poor mold flow. Excessive temperatures can degrade the PETG. Typical melt temps range from 220°C to 290°C depending on grade.
- Mold temperature – Cooler molds improve clarity while hot molds improve release. Mold temps typically range from 15°C to 40°C for PETG.
- Injection speed – Starts slower to allow uniform mold filling, then increases to complete cavity packing.
- Cooling time – Balances adequate curing time with reasonable cycle times.Insufficient cooling promotes visual defects like sinks and warpage.
Adhering to these processing windows helps injection mold sound PETG parts efficiently. Tight process control minimizes rejects thereby reducing associated costs.
Benefits of PETG Injection Molding
Choosing injection molding for working with PETG plastic offers several benefits:
- Complex geometries – Precision molds can manufacture intricate shapes not possible otherwise
- Efficiency – Automated mass production with faster cycles and lower labor
- Consistency – Highly repeatable dimensional accuracy and mechanicals
- Economical – Very cost competitive at scale versus other processes
- Decorating – Integrated in-mold decorating and branding
Injection molding unlocks PETG’s fullest potential for producing clear plastic components with tight tolerances, smooth finishes and complex customized shapes.
PETG vs. Other Clear Plastics
PETG competes against other clear thermoplastics like:
Polycarbonate (PC) – Higher impact but easier to scratch with limited chemical resistance. Also considerably more expensive.
Acrylic PMMA – Greater rigidity but half the impact strength with limited chemical resistance.
Compared to these alternatives, PETG uniquely balances optical clarity, toughness, chemical resistance and ease of processing – making it an economical choice for transparent injection molded components.
Manufacturers switching existing applications or exploring new transparent plastic parts find PETG’s all-round performance and cost structure compelling.
Injection molding magnifies PETG’s advantages further – enabling mass production of crystal clear custom shapes faster and more economically.
Getting Started With PETG Injection Molding
Interested in leveraging PETG injection molding for your application? Here are some recommendations on getting started:
1. Design product and define requirements – Figure out what shapes,features and performance your PETG parts need for their end use.
2. Prototype molds – Work with your injection molder to prototype and adjust molds to meet requirements.
3. Characterize PETG grade – Different grades have varying properties. Identify one aligned with your needs.
4. Dial-in injection molding process – Takes testing across multiple molds and process parameters to optimize repeatable production.
5. Validate performance – Quantitatively benchmark molded PETG part performance to original requirements.
While it takes effort to engineer the initial molding process, once locked in, injection molding provides a consistent, economical production solution for OEMs. In fact, the effort to design and refine high complexity molds lowers per part costs at higher production volumes.
Well characterized PETG formulations, smart mold designs and tightly controlled process windows result in higher performing injection molded components.
The Takeaway
In summary, PETG is an exceptional thermoplastic for producing clear injection molded parts with elevated requirements for strength,chemical compatibility and dimensional stability across wide-ranging industries.
Injection molding PETG delivers an optimal balance of performance, design latitude and economics while preserving environmental sustainability through recyclability.
So in response to the opening question – Can PETG be injection molded? – hopefully you’re convinced of an emphatic yes from the detailed overview above!