Injection molding is a popular manufacturing process used to create plastic parts and products. Two common plastic materials used in injection molding are nylon and PVC (polyvinyl chloride). But can these two plastics use the same injection molding equipment? As a professional nylon injection molding and PVC injection molding manufacturer, I will help you find it out!
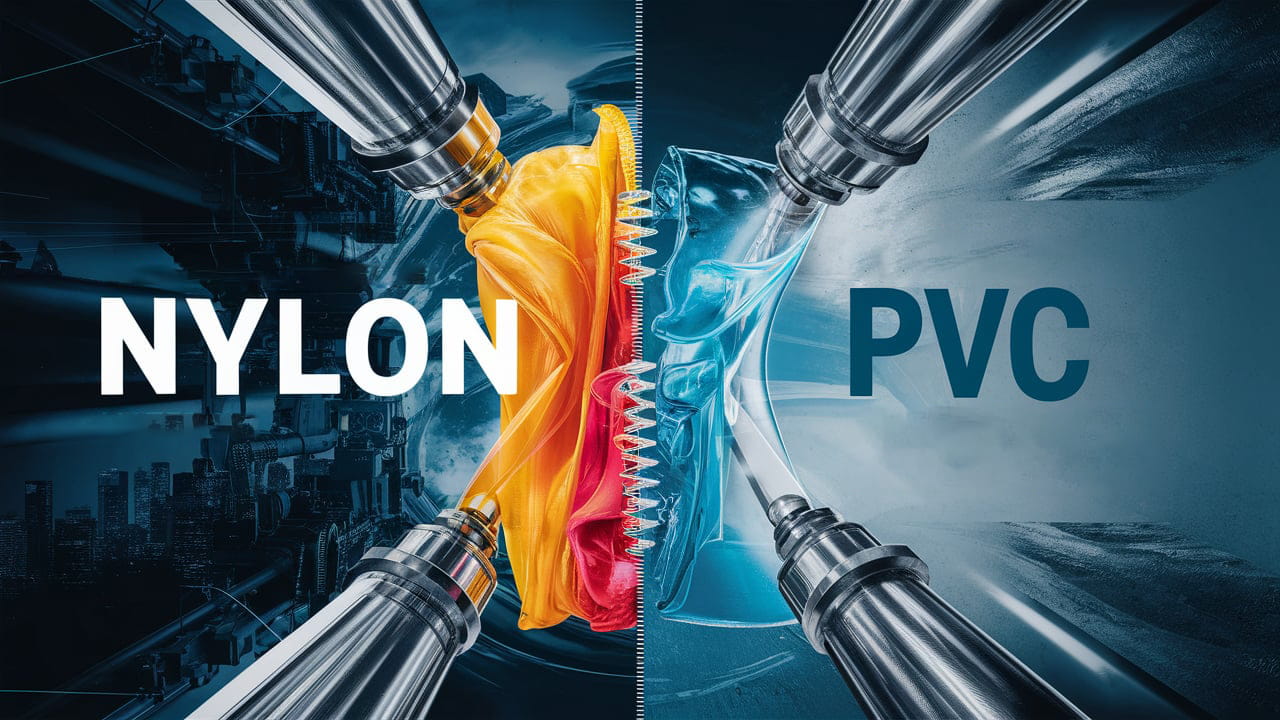
Can Nylon and PVC Use the Same Injection Molding?
The short answer is yes, it is technically possible to use the same injection molding machines and molds for both nylon and PVC. However, there are some significant challenges involved with switching between these two materials on the same equipment.
Key Differences Between Nylon and PVC
Before getting into the specifics of using the same injection molder for nylon and PVC, it’s helpful to understand some of the key differences between these two plastics:
Processing Temperatures
- Nylon – Requires high temperatures, usually 230-280°C (446-536°F)
- PVC – Has a lower processing range, around 160-210°C (320-410°F). Temps over 210°C can cause decomposition.
Mold Temperatures
- Nylon – 80-100°C (176-212°F)
- PVC – Much lower, 20-50°C (68-122°F)
Moisture Sensitivity
- Nylon – Hygroscopic, must be thoroughly dried before processing
- PVC – Not moisture sensitive
As you can see, nylon and PVC have very different requirements when it comes to injection molding. Switching between them requires significant adjustments to temperatures as well as moisture control.
Challenges of Using One Injection Molder
While it’s possible to use the same injection molding machine for both nylon and PVC, there are some distinct challenges:
1. Temperature Control Difficulties
The injection molding machine must be capable of reaching nylon’s high processing temperatures of over 400°F. Yet it also has to precisely control the much lower PVC temperatures to avoid decomposition risks. This temperature range switchover takes significant time.
2. Risk of Material Contamination
Even tiny amounts of residual nylon left in the barrel, screw, or hot runners can contaminate the PVC material and cause quality issues. Thorough cleaning between material changeovers is essential.
3. Potential for PVC Degradation
If residual heat from nylon isn’t thoroughly dissipated, PVC melt temperatures may rise to over 400°F during processing leading to the release of corrosive and hazardous gases.
4. Different Mold Design Requirements
Due to differences in shrinkage rates and cooling behavior, separate molds may be needed for nylon parts vs PVC parts. Using one mold for both materials likely won’t provide optimal results.
As you can see, there are good reasons why different injection molding machines and tooling are typically dedicated to specific materials like nylon or PVC.
Best Practices for Using One Injection Machine
However, if you need to use the same injection molder for both nylon and PVC, here are some best practices:
- Use machines with a broad processing temperature range and precise controls
- Have thorough material purging protocols between changeovers
- Allow for lengthy changeover and temperature stabilization times
- Design molds to account for differences in the materials
- Closely monitor melt temperatures and machine settings
While possible, switching repeatedly between nylon and PVC requires diligent process control and a keen eye on safety. Cross-contamination risks mean it should only be done when absolutely necessary.
The Bottom Line
So can nylon and PVC use the same injection molding equipment? Yes, with careful precautions around machine settings, temperature controls, mold designs, and changeover purging. But for efficiency and quality reasons, it is generally recommended to dedicate specific injection molders and tooling to each material.
Combining dissimilar plastics like nylon and PVC on one machine is complex, requiring stringent process monitoring and safety steps. The risks of material degradation make separate, optimized molding setups the ideal scenario for both these popular injection molding plastics.