Polypropylene (PP) is one of the most versatile thermoplastics used in injection molding applications today. As an experienced plastic injection molding manufacturer, I often get asked, “Can polypropylene be used in injection molding?”.
The short answer is yes – polypropylene is an excellent material choice for injection molding and is used widely across countless industries. From packaging to automotive parts and medical devices, polypropylene injection molding enables manufacturers to produce an array of products efficiently and economically.
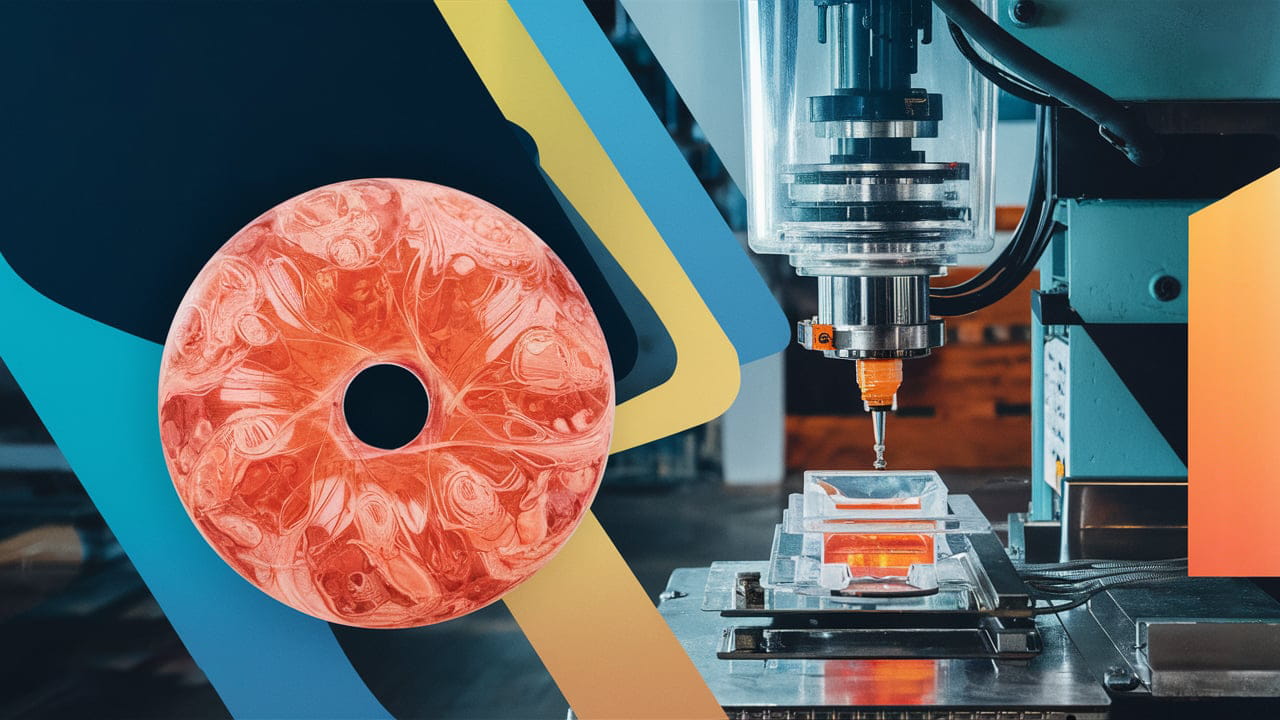
Why Polypropylene Works Well for Injection Molding
So what makes polypropylene such a popular option for injection molding? There are several key properties that set polypropylene apart:
Low Viscosity
Polypropylene has a relatively low melt viscosity compared to many other thermoplastics. This means the molten PP flows smoothly and easily into the mold tooling to replicate intricate shapes with precision. The excellent flow also minimizes the injection pressure required, reducing potential manufacturing issues and costs.
Good Dimensional Stability
The semi-crystalline structure gives PP favorable dimensional stability during processing. Parts maintain shape and size accuracy without too much shrinkage or warpage. This consistency allows for tighter dimensional tolerances to be held.
High Fatigue Resistance
With impressive fatigue and flex life properties, polypropylene withstands cyclical loading well without compromising strength. Parts can be bent or twisted repeatedly over long periods with minimal chances of failure.
Easy Processability
Polypropylene is simple to work with, with forgiving process parameters. The polymer flows easily into complex tooling and solidifies relatively fast. Parts can be demolded rapidly, speeding up overall cycle times. This makes scaling up mass production runs efficient.
Excellent Chemical Resistance
Polypropylene offers broad chemical resistance, with high immunity to acids, bases, solvents and other corrosive substances. This durability suits the material for items like tanks and pipes carrying chemicals and solvents.
Low Coefficient of Friction
The slick surface helps to facilitate the ejection of PP parts from injection molds, overcoming the problems of parts sticking within tooling. This improves manufacturability and reduces overall costs.
Common Applications of Polypropylene Injection Molding
Thanks to its outstanding balance of properties, injection molded polypropylene components feature across many vital industries:
Automotive Industry
Polypropylene is used to produce countless interior and exterior auto parts like bumpers, panels, battery cases, fluid reservoirs, and ventilation system components. The material stands up to prolonged mechanical stresses while keeping part weights modest.
Medical Sector
The exceptional chemical resistance allows polypropylene products to avoid degradation in contact with the harsh disinfectants and cleaning agents used within healthcare. Typical applications include syringes, IV connectors, pill dispensers, vials, medical trays, test tube racks, and disposable gowns.
Consumer Goods
Injection molded polypropylene lends itself to the diverse parts found in modern appliances and gadgets. Microwaveable containers, dishwasher components, fans, power tool housings all exploit polypropylene’s strength, stiffness and heat resistance while meeting aesthetic requirements.
Food Packaging Industry
As a food-contact safe material resistant to moisture and grease/oil, clear polypropylene containers and closures keep contents fresh. The translucency provides excellent product visibility as well. Yogurt cups, deli packs, sauce bottles, ice cream tubs are some examples.
Other Notable Uses
Polypropylene injection molding also creates garden furniture, sports safety gear like helmets/guards, home storage solutions, electronic casings, toys, stationery sets, garden tools, pet carriers, laboratory consumables and more on an immense scale annually.
Polypropylene Grades for Injection Molding
Polypropylene for injection molding is supplied in pellet form by resin manufacturers to be melted and molded. The pellets come in various standard grades tailored to different niche applications.
Homopolymer Polypropylene
This is the basic grade, consisting of only propylene monomers. The highly ordered chain structure lends high rigidity, hardness and heat resistance. Homopolymer PP suits parts needing high strength like industrial containers and automotive components.
Random Copolymer Polypropylene
As the name suggests, this grade has random ethylene units distributed along PP molecular chains. The ethylene enhances flexibility, durability and optical properties relative to homopolymer. Copolymers give molded products improved transparency and surface finish.
Impact Copolymer Polypropylene
Here a small portion of ethylene-propylene rubber is introduced into the PP matrix. The rubber phase boosts impact energy absorption drastically without compromising stiffness greatly. The toughened material brings better crack/stress resistance for demanding applications.
Filled/Reinforced Polypropylene
Fillers like mica, talc, glass fibers and carbon fibers can be added to enhance dimensional stability, temperature resistance, stiffness and strength in line with specific targets. The composites widen the design possibilities substantially.
Polypropylene Molding Conditions
To achieve defect-free, consistent injection molded polypropylene components, close attention is necessary to set optimum conditions:
Machine Barrel Temperatures: 200-280°C; excessive heat degrades material.
Melt Temperature: 200-250°C ensures low viscosity for smooth flow.
Mold Temperature: 10-60°C (preferably around 30-45°C); rapid cooling induces internal stresses.
Injection Speed: Medium to high, augment gradually once filling begins.
Injection Pressure: 50-100 Mpa holding time: 3 – 30s (depending on part thickness)
Back Pressure: 0.5-1 MPa improves melt homogenization.
Maintaining the above guidelines helps avoid common defects like warpage, sink marks, hollow sections, and poor replication of part details.
Part Design Rules for Polypropylene Injection Molding
Several fundamental design principles must be followed when creating parts intended for polypropylene injection molding:
- Uniform wall thickness as much as possible
- Minimum draft angles of 1° taper on vertical faces
- Generous external radii at transitions and corners
- Appropriate placement of weld/melt lines away from areas of high stress
- Minimum rib thickness less than 50% of adjoining wall thickness
- Sufficient space for gas bubbles to vent smoothly
Accounting for these during the design phase alleviates many downstream manufacturing headaches and prevents costly tooling modifications further along the timeline.
Prototype builds should be carried out before progressing to full production runs to identity potential design drawbacks.
Why Work with a Specialty Injection Molding Partner?
As we have covered here, polypropylene is clearly an exceptional choice for injection molding across an array of key industries. To leverage the full potential of the material though, world-class manufacturing facilities and expertise are vital.
Rather than gambling on substandard, unreliable suppliers, the smartest strategy we have found after years in the business is collaborating with an established, vetted injection molding partner intimately familiar with polypropylene.
The right partner offers round-the-clock engineering assistance to finesse part designs for functionality and efficient moldability. They bring insight into suitable PP grades from reputable material companies that best match application requirements.
On the production floor itself, seasoned technicians oversee a regimented, ISO-certified process flow utilizing high-accuracy injection molding machines expressly for polypropylene handling. Stringent inspection procedures utilize advanced measuring devices to guarantee every dimension, weight and feature conforms closely to specifications.
This degree of quality control and assurance across the entire value chain is unattainable without a trusted injection molding ally. From rapid turnaround of functional validation builds to streamlined ramping of full-scale manufacturing, the support provided reduces overheads substantially when working with polypropylene.
So in summary – yes, polypropylene is undoubtedly one of the most versatile engineering thermoplastics for injection molding. To fully unlock its advantages for your specific application and part though, team up with a specialty injection molding partner today!