Injection molding can seem like a major investment, with mold costs often reaching $10,000+. But what exactly makes this process so pricey?
In this post, as a professional plastic injection molding manufacturer, I’ll break down the real costs behind injection molding – from materials and labor to maintenance – so you know what to expect. My goal is to help you budget properly and make informed manufacturing decisions.
Let’s get to it!
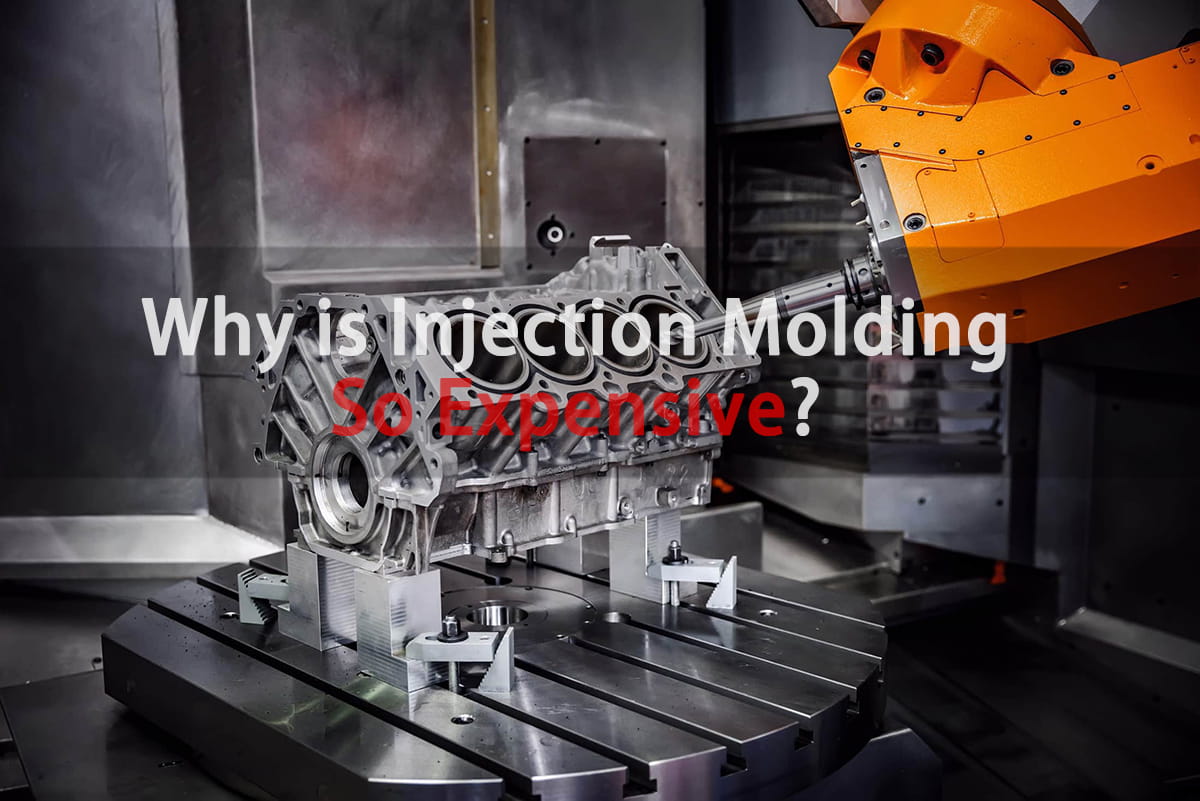
The Shockingly High Price Tag on Injection Molds
The injection mold itself is where most costs come from. We’re talking $1,000 on the very low end, ranging up to $80,000+ for a large, complex multi-cavity mold.
On average, expect to pay $12,000.
What makes these molds so gosh darn expensive?
Precision-Machined Metals
Injection molds need to withstand thousands of PSI and cycling temperatures of 400°F+. So they must be precision CNC machined from hardened metals like tool steel or aluminum.
These chunks of metal don’t come cheap! Just the raw material costs run $1,000 to $5,000 for simpler molds.
Complex Geometries
Undercuts, side-slides, conformal cooling channels…complex mold components radically increase costs but also improve part quality and cycle times.
A basic 2-plate mold may run you $3,000. The same part design with side-slides? Closer to $15,000!
Tight Tolerances
Mold components must align perfectly with tolerance of 0.005″ or less. This extreme precision guarantees accurate, flash-free parts from the very first shot.
Highly-skilled operators running 5-axis CNC machines are needed to hit tolerances this tight. And their time doesn’t come cheap!
Long Lead Times
You can’t just order an injection mold on Amazon Prime. reputable mold builders often quote 4-6 weeks for delivery of finished tooling.
Why the long lead time?
Well first, the mold design itself takes 1-2 weeks. Then skilled operators need lots of machine time to CNC precision cavities and cores from steel blocks.
Let’s not forget about polishing, gating, venting, approval checks…many important steps go into building a robust, efficient mold.
Rushing the process risks cracking the mold weeks or months later. And NO ONE wants that!
Sky-High Operating Costs
You got your shiny new mold. Now what?
Well get ready to pay for presses, plastic resin, plant utilities and more during production. Here are the main operating costs to consider:
Injection Molding Machines
Plunk down $75,000+ for a new machine rated to your part size and injection pressures. Then allot budget for repairs down the road.
Electric bill averaging $3,000 per machine/month. And you’ll need a skilled tech to operate and maintain the cell – $25/hr + benefits. It adds up!
Raw Plastic Material
You’ll easily blow through thousands per WEEK on plastic resin for high volume production. Even commodity materials like ABS and polypro cost $1 to $5 per pound.
Fancier resins like ULTEM and PEEK run $50 per pound or more!
Facility Costs
From cooling towers to air handlers, it takes serious infrastructure to run an injection molding plant. Expect utility bills in the tens of thousands monthly for medium-large operations.
The Hidden Costs of Maintenance
Insert a chunk of hot plastic into steel tooling thousands of times per week…what could go wrong?
Plenty actually! Worn mold components, material contamination, press crashes – so many issues threaten production.
Smart manufacturers build at least 10% “spare” budget to keep lines running via:
Preventative Maintenance
Expect mold reworks costing hundreds to thousands of dollars throughout the mold’s operating lifetime. This mostly involves replacing common wear items like gates and sealing components.
You should also budget for periodic benchtop cleanings and laser scanning to spot issues early.
Spare Parts Inventory
Stock common mold components like ejector pins, sleeves, and return pins for quick repair turnaround. Downlines from mold issues cost WAY more than the parts themselves!
Extra Mold Cavities
Order your molds with +1 or 2 extra cavities. If one core/cavity pair goes down, you can swap in the “spare tire” backup and keep producing.
The Verdict: Is Injection Molding Expensive?
Well…yes and no.
Upfront, expect BIG investment into injection molds and manufacturing infrastructure before producing the first part. We’re talking tens of thousands minimum.
However, this process shines for mass production of hundreds, thousands or millions of identical plastic pieces. With volume, your fixed costs get amortized over more and more parts produced.
Let’s say you sell those parts for $10 each. On the 20,000th unit, your production costs may dip below $5 per piece. Now THAT’S economy of scale!
So while scary at first glance, understand the mold and machine are fixed assets that pump out parts for years with proper maintenance. The incremental cost per piece drops tremendously in high volume production.