Acrylic injection molding is the process of shaping acrylic plastic by injecting it into a mold. It allows acrylic to be formed into products like lenses, screens, and panels. As a professional acrylic injection molding manufacturer, I’ll walk you through the entire acrylic injection process step-by-step.
The acrylic injection molding process begins by designing a mold to create the desired part. The acrylic granules are then dried, loaded into the injection machine, and injected into the mold. After cooling and hardening, the acrylic part is ejected and can go through additional finishing steps.
Keep reading as I break down each stage of acrylic injection molding to help you understand exactly how it works.
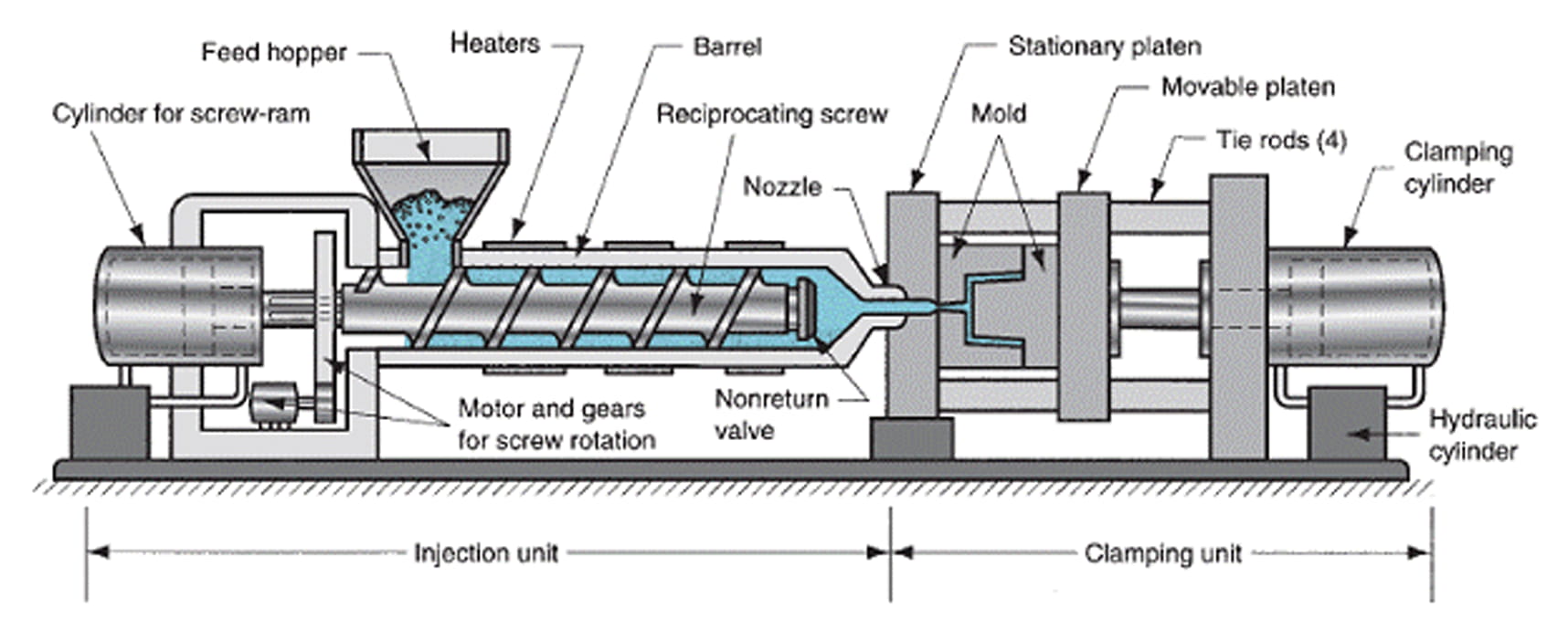
Acrylic Injection Molding Process
Step 1: Mold Design
The first step is creating the injection mold to form the acrylic parts. The mold consists of two halves—the cavity half and core half—that join to form the interior mold space. The acrylic takes this shape once injected.
Mold designers use 3D CAD software to precisely model injection molds. Complex geometries and features can be designed to detail and converted into machining code for the mold shop. Holes, inserts, texturing and other specifications are considered as well at this early stage.
Getting the mold design right is crucial. Smart gates, vents, draft angles all ensure a proper acrylic flow and quality end result. An experienced mold maker will take these nuances into account when fabricating the final production mold tool.
Step 2: Acrylic Material Preparation
In its raw form, acrylic comes as translucent beads or pellets that resemble granulated sugar. Manufacturers keep the acrylic resin dry in a climate-controlled environment to maintain the proper moisture content. Too much moisture creates bubbles and other defects once injected into the mold.
Some acrylic resins are hygroscopic. As such, manufacturers load material from a drying hopper unit that contains desiccant beds. Then heated dryers warm the acrylic above 200°F to drive off residual moisture before molding.
The dried acrylic flows down into surge bins to wait for injection. Some injection molding machines even have built-in resin dryers to simplify the material delivery system.
Acrylic Drying Process
It’s critical that acrylic resin stay bone dry prior to injection molding. Any trace moisture turns to flash steam as the hot plastic enters the mold.
Even the most precisely manufactured parts exhibit small fissures, bubbles, and visual defects when there’s moisture inside. No bueno!
Step 3: Clamping the Mold
To start production, a machine operator clamps the injection mold in the press. Hydraulic cylinders apply tons of pressure to securely close the core and cavity halves. This prevents the pressurized molten plastic from leaking once it’s injected at high velocities.
The clamp’s pressure must overcome the collective forces trying to push the mold halves apart during injection. Tie bars increases the sturdiness between platens.
Step 4: Injecting the Acrylic
With the mold securely clamped, molten acrylic flows from the injection barrel and into the sprue. The runner system directs the hot resin into every crevice of the tool’s cavity to completely fill the empty space.
Screw presses feed solid pellets into the barrel and use electric heaters and mechanical energy to liquefy the plastic. It shoots forward once the injection pressure exceeds the mold cavity pressure.
Pack and Hold
To prevent early solidification, more resin floods in after the cavity fills. This packs in additional molten acrylic and applies a hold pressure until gate freeze off.
Parts maintain shape and experience less distortion thanks to this secondary packing step. It allows extra time for the hot resin to seek its final form before cooling beings.
Step 5: Cooling and Curing
After packing, chilled water circulates through ports inside the tool to solidify the superheated acrylic plastic. Complex channel routing strategically targets hot spots for accelerated cooling.
Ejector pins extend slightly to shrink the plastic off the core surfaces. This prevents parts from sticking once they’re ready to be pushed out of the mold.
Cooling times vary based on wall thickness. Thicker plastic holds heat longer than thinner cross sections. Newer molds use conformal channels to speed up cooling for shorter cycle times.
Step 6: Ejecting Acrylic Parts
To manually eject a cured acrylic component:
- The clamping force releases, allowing the injection mold halves to separate
- Using guide rods, the ejector plate advances forward to push parts out of the cavity side of the tool
- Robotic arms or workers grab finished items outside of the molding press
For simpler shapes with straight pull mold designs, automatic ejection systems function best. They instantly clear parts off each tool face without needing manual labor.
Additional Finishing Steps
After basic ejection, acrylic parts often undergo additional post molding processes that:
- Trim away extra plastic flashed
- Sand or polish mating tool marks
- Flame and vapor polish surfaces
- Apply hard coatings for enhanced protection
- Bond assemblies together via adhesive or welding
This finishing work improves cosmetics and prepares the acrylic components for shipment or the next manufacturing process.
The acrylic injection molding process continues as additional components get overmolded, labels adhere, hardware mounts, and final testing validates part quality.
Applications of Acrylic Injection Molding
Clear or colored, acrylic plastic offers production flexibility using injection molding techniques. Let’s look at some common applications.
Auto Headlights and Tail Lights
Carmakers mold custom headlights and taillights from acrylic. This material stands up to years of road abuse without degrading from UV exposure.
Headlight assemblies feature complex reflectors that require precision injection molding capabilities. The acrylic plastic also creates ideal optical lenses to diffuse light beams where needed.
Synthetic Ice
You can injection mold specialized grades of acrylics to mimic the appearance and friction properties of ice. Synthetic ice rinks address the high cost of keeping traditional ice frozen solid.
Venues for curling, figure skating, and hockey stay operational year-round thanks to injected acrylic. The material also travels well for temporary ice events that don’t have permanent refrigeration infrastructure.
LCD Screens
Flat screens rely on acrylic viewing windows and optical light tubes for vibrant display clarity. Mold makers precisely craft defect-free, ultra clear plastic to pour light through the various LCD layers.
Skilled technicians polish molded parting lines away after demolding. This removes blemishes before sandwiching other electronic components between the formed panes.
Acrylic Injection Molding Process FAQs
Here are answers to common questions regarding the acrylic injection molding process:
What machines are used?
Standard injection molding presses thermally process acrylic compounds for molding applications. Machines range from small vertical types to larger horizontal configurations with tons of clamping force.
Injected acrylic also works with metal injection molding presses. These specialized machines accommodate powdered metal mixes in addition to traditional resins.
Can you injection mold all types of acrylic?
Yes, grades like extruded acrylic, cell cast, and continuous cast acrylic all injection mold with success. Manufacturers tailor cooling routines, fill rates, mold temperature and other parameters to process different acrylic formulations.
Why plasticize acrylic?
In its raw pellet form, acrylic won’t flow and fill intricate part details. Plasticizing transforms rigid acrylic resin into a free-flowing fluid. This allows complete mold penetration before cooling resets the acrylic into a solid shape.
Heating acrylic between 240°C and 320°C melts the material for proper injection viscosity. The acrylic won’t chemically decompose until over 380°C, well above standard molding temperatures.
Conclusion
Understanding the complete acrylic injection molding process allows you to plan a product launch that efficiently uses this clear plastic material.
Leveraging the right injection molding partner helps avoid manufacturing delays and costly iteration mistakes. Their experience will make the difference during acrylic mold qualification.