Plastic injection molding has become one of the most common manufacturing processes across various industries. And for good reason. This versatile technique offers numerous benefits that can give your business a serious competitive edge.
In this comprehensive guide, as a professional plastic injection molding manufacturer, I’ll walk you through the key advantages of plastic injection molding so you can determine if it’s the right fit for your manufacturing needs.
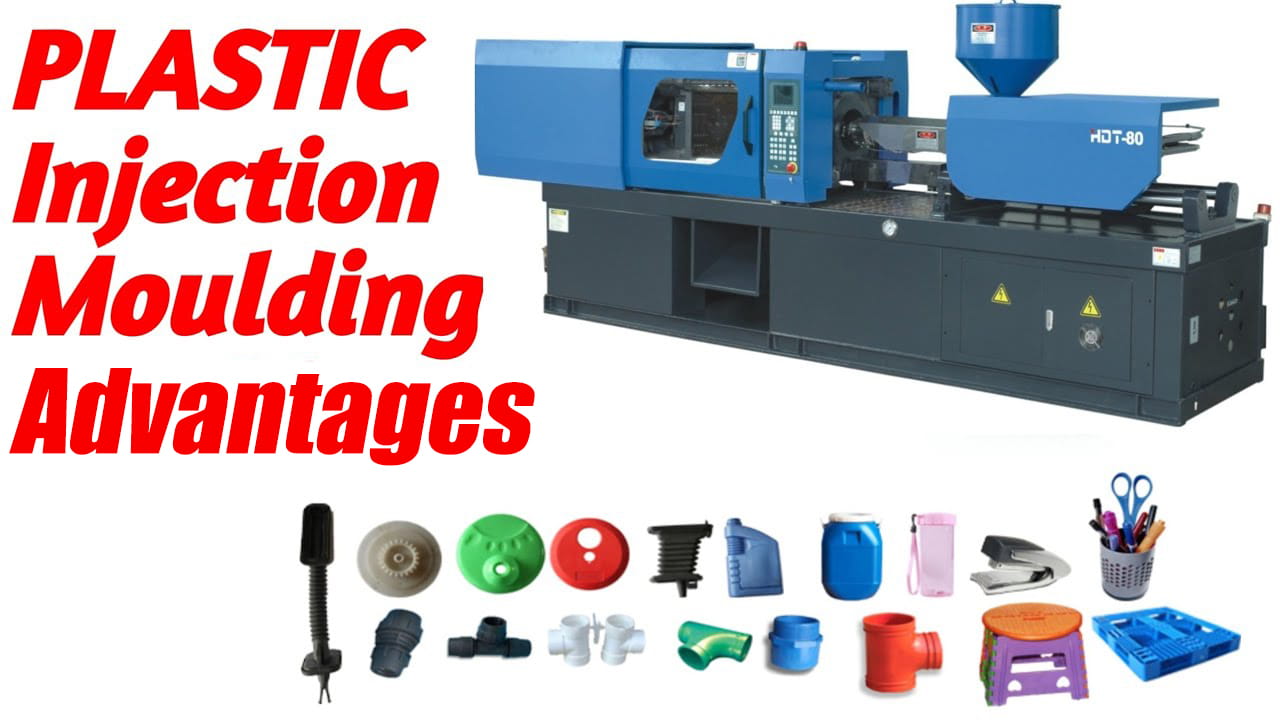
What Are the Advantages of Plastic Injection Molding?
High Volume Production Capabilities
One of the biggest upsides of injection molding is its ability to produce high volumes of plastic parts efficiently.
The whole process is highly automated using machines and robots. Once you have the injection mold tool designed and built, you can crank out thousands of identical plastic components at a rapid pace.
In fact, the molding cycle time can be as low as 10-15 seconds. Which allows you to manufacture hundreds of items per hour depending on part size and complexity.
This high rate of production makes injection molding extremely cost-effective. The more parts you produce, the lower your per unit cost becomes.
So if you need to create large quantities of plastic parts – we’re talking thousands or millions – injection molding is the way to go. The high outputs keep overall manufacturing costs low and product pricing competitive.
Tolerance for Complex Geometries
Another major benefit of injection molding is its tolerance for producing complex plastic part designs.
The molten plastic material gets injected into the mold cavity at extremely high pressures. This allows the plastic to take the shape of even the most complex mold geometries.
As a result, you can manufacture plastic components with intricate contours, detailed features, and tight tolerances accurately and repeatedly.
This includes parts with ribs, bosses, threaded holes, slots, engraving, logos, and more.
The ability to create complex injection molded components opens up lots of possibilities in terms of product design and functionality.
Material and Color Flexibility
When it comes to plastic injection molding, you have seemingly endless options in terms of materials and color choices.
There are thousands of plastic materials to select from including common resins like ABS, polypropylene (PP), polyethylene (PE), nylon, and more. These all have differing properties in terms of durability, flexibility, impact resistance and so on.
You can even use specialized materials like medical-grade plastics, antistatic plastics, and engineering plastics to suit more demanding applications.
This material flexibility allows you to dial in the exact mechanical and physical properties your application calls for.
As for colors, you have millions of shades and hues at your disposal. Injection molders can produce custom plastic parts in virtually any color imaginable.
Common coloring techniques include pre-colored resins, color masterbatches, liquid dyes, or even mixing multiple materials together.
Enhanced Strength Capabilities
Today’s advanced plastic materials offer exceptional strength comparable to metal in many applications.
Injection molders have thousands of plastic formulations at their disposal with properties aligned to the strength requirements of the part.
Options include shock and impact-resistant materials as well as plastics reinforced with glass fibers or carbon fibers for added structural rigidity. These strengthened plastics can replicate or exceed the strength of die-cast metals in some cases.
You even have advanced plastic composites that combine polymers, ceramics, nano-materials, foaming agents, and other additives for superior mechanical performance.
So when designed properly, injection molded plastic components can be exceptionally strong and durable while remaining lightweight.
Lower Manufacturing Costs
As mentioned already, injection molding is highly efficient at producing high volumes of plastic parts, which intrinsically leads to lower manufacturing costs.
But beyond efficiency, it’s an automated, streamlined process that requires less direct labor compared to other techniques like CNC machining or 3D printing.
Once the injection molds are designed, robots and machines do most of the legwork when it comes to molding production. The human oversight is minimal.
Lower labor requirements directly translate into reduced manufacturing costs. And those savings can get passed onto customers.
Furthermore, because injection molding generates very little excess material waste, you conserve resources and minimize waste removal fees being baked into your overheads.
Quick Turnaround Times
The initial design and tooling phase of injection molding does take some time upfront. You first need to go through prototyping and testing before the mold tool is finalized.
However, once the mold tool is built and debugged, the component production turnaround times are very quick.
We’re talking cycle times as low as 10-15 seconds. With multi-cavity molds, you can manufacture hundreds of plastic parts per hour.
So if you already have existing mold tools, injection molding allows you to ramp up inventory very quickly to meet spikes in demand. Or quickly source additional plastic parts as needed.
The high throughput keeps production numbers high and product availability consistent despite tight turnarounds.
Precise Repeatability
Consistency and precision are hallmarks of the injection molding process. When done right, you can manufacture extremely uniform plastic components batch after batch.
That’s because injection molding uses the same mold tool repeatedly to produce each part. This allows for a very high degree of repeatability and precision unmatched by other manufacturing methods for plastics.
You can achieve plastic part tolerances within +/- 0.005 inches fairly easily depending on part size, geometry, and material used. For intricate components, that level of consistency is critical.
Environmentally Friendly
Finally, plastic injection molding is one of the most environmentally friendly processes for producing plastic parts. It generates very little excess plastic waste relative to traditional manufacturing processes.
Any extra plastic sprues or runners leftover from the injection molding process get reground and recycled to reuse in future production runs. This helps minimize new resource consumption.
Injection molding companies also rely on energy-efficient machinery and utilize automation technology to conserve electricity consumption and carbon emissions.
Many also leverage solar power or other renewable energy sources to power their facilities. This contributes to an overall smaller environmental footprint.
In Summary
The injection molding offers heightened efficiency, lower manufacturing costs, quick turnarounds, exceptional repeatability and consistency, tolerance for complexity, strength, and eco-consciousness. Leveraging these key advantages allows all sorts of businesses to improve operations and boost profit margins over the long haul.