The large part injection molding is the process of using high-powered machines to produce massive plastic components. Everything from washing machine tubs to car body panels.
In this post, as a professional large part injection molding manufacturer, I’ll outline the most common applications of large part injection molding that I’ve come across.
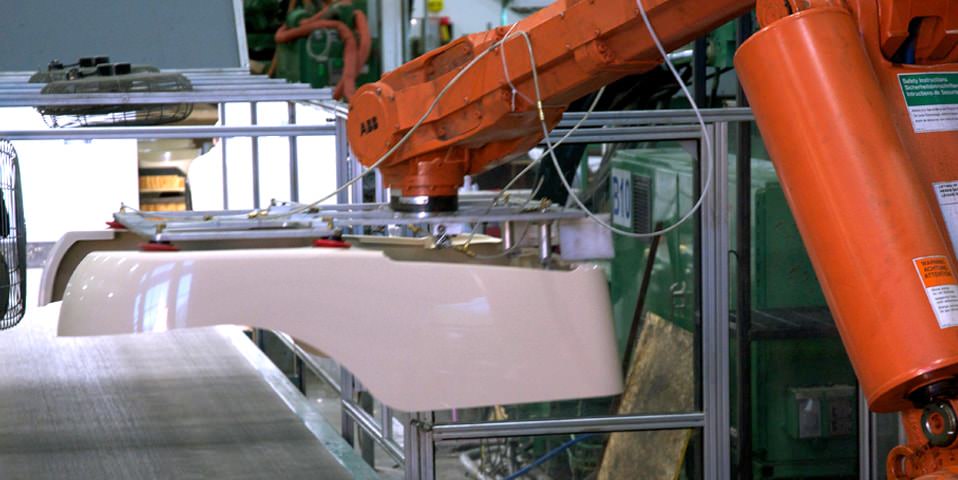
Why Large Part Injection Molding Is Used
Before jumping into the applications, it helps to understand why manufacturers use large part injection molding in the first place.
Here are three of the main reasons:
1. Cost Savings
For high volume plastic part production, injection molding offers drastic per-unit cost savings over other processes like CNC machining or 3D printing.
These savings get amplified with large part injection molding. That’s because you can fit more parts into each production cycle. Which spreads the upfront costs of things like the injection molding mold over a higher number of units.
2. Design Flexibility
Modern injection molding presses offer incredible clamping force and precision. This lets you create large plastic parts in virtually any shape or configuration your design calls for.
Want a 5 foot long plastic enclosure for an industrial application with ribs for strength? No problem. Need a geometrically complex dashboard for an automobile? Large part injection molding can handle intricate designs.
3. Material Versatility
Injection molding works with just about any thermoplastic material.
That includes common choices like:
- Polypropylene (PP)
- Acrylonitrile butadiene styrene (ABS)
- Polycarbonate (PC)
Along with high performance plastics such as:
- Ultra high molecular weight polyethylene (UHMWPE)
- PEEK
- Torlon®
You can even combine resins. Such as ABS alloyed with polycarbonate. Giving designers ultimate flexibility.
This material flexibility – along with design freedom and cost efficiencies – makes large part injection molding ideal for producing big plastic components across a number of industries.
Common Applications of Large Part Injection Molding
Now that we’ve covered why large part injection molding is commonly used, let’s get into some specifics on applications.
White Goods & Appliances
One major application is large home appliances. Also known as white goods. This includes things like washing machines, refrigerators, ovens, microwaves, and dishwashers. For example, washing machine tubs are often produced with large part injection molding.
As you know, these components need to stand up to chemicals, heat, and mechanical stresses from constant use. Making injection molded plastics like polypropylene an ideal fit. The same goes for dishwasher trays. These demand both heat resistance and durability.
Large injection molded parts also show up in the outer shells of appliances. For instance, injection molded polycarbonate is perfect for its clarity, toughness, and heat resistance. This allows it to stand up to bumps and spills while enabling features like see-through panels on refrigerators.
Automotive
Another major user of big injection molded components is the automotive sector. In fact, injection molded plastics make up 50% of the volume in today’s cars while only being 10% of the weight. And large part technology produces many of the more sizable plastic components.
For example, front-end body panels and bumper fascias like this require large 500-2000+ ton injection molding presses to manufacture. The same goes for bigger interior trim pieces and body side moldings.
Plastic fuel tanks capable of holding 25+ gallons of automotive liquids are also produced on large part injection molding machines.
Aircraft Interiors
Another large scale application for big injection molded components is aircraft interiors. For example, overhead stowage bins on passenger jets can be manufactured as one piece injection molded parts. Same with intricate seat back trays holding passenger amenities.
Producing these large, fairly complex components with plastic injection molding provides airline manufacturers with cost efficiencies at their needed production volumes. It also allows for weight savings versus other materials – which directly translates into sizable fuel savings.
Fluid Handling
One last large part molding application I wanted to highlight is injection molded plastics for fluid and chemical handling. For instance, 1000+ liter IBC tanks like this are often rotationally molded polyethylene. But smaller tanks and vessels of around 500 liters or less tend to go the injection molded route.
The design flexibility injection molding provides allows for inlet, outlet, sight glass, and fork truck base features to all be integrated into tanks like these in the molding process. No secondary operations needed.
Which are some common applications that utilize large part injection molding you’ve encountered? I’d be interested to hear about them in the comments!
In Summary
As you can see, applications of big injection molded components are diverse. play a pivotal role across industries from appliances to aerospace. And demand continues to grow as manufacturers realize the cost and performance benefits over other materials like metal or composites.
So if you’re a product company looking to produce large components, large part injection molding is worth exploring. Modern injection molding presses offer the needed clamping forces and precision controls to manufacture a variety of sizable plastic parts.
Large Part Injection Molding Opens up Mass Production Applications for Sizable Plastic Components
As we covered here, large part injection molding facilitates manufacturing big plastic components – from washing machine drums to 1000 liter chemical tanks.
The technology provides:
- Cost savings through production efficiencies
- Design flexibility to create virtually any shape
- And material versatility to pair the right thermoplastic resin with application needs
Making it an enabling technology for mass production across sectors.
So if you’re looking to produce sizable injection molded parts, be sure to explore large part injection molding processes to enable your product designs.