Plastic injection molding is one of the most versatile manufacturing processes available today. This innovative method can produce a vast array of plastic parts for a wide range of industries and applications. But what exactly are the applications of plastic injection molding?
In this detailed guide, as a professional plastic injection molding manufacturer, we’ll explore the numerous uses and key benefits of plastic injection molding across various sectors. Whether you’re looking to produce small precision parts or large robust components, injection molding likely has a solution. Let’s take a closer look.
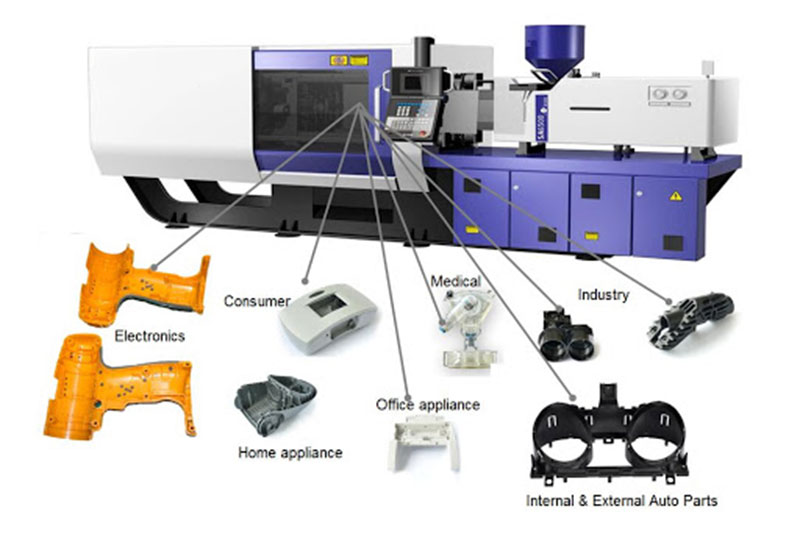
Why Is Plastic Injection Molding So Versatile?
Before diving into specific applications, it’s helpful to understand what makes injection molding such an adaptable process in the first place. There are a few key reasons this manufacturing technique can produce such a vast range of products:
Design Flexibility
Molds can be designed to accommodate complex geometries and achieve intricate details in plastic parts. This enables the creation of unique and innovative product designs not easily achieved through other methods.
Adaptability of Materials
With over 25,000 compatible plastic resins and engineering materials to choose from, injection molding can work with different polymers to meet specialized requirements. This includes advanced composites and other substances beyond just plastics.
Precision
The injection molding process can repeatedly produce extremely precise plastic components within tight dimensional tolerances. This ability enhances quality assurance across production volumes.
Efficiency
After the initial mold fabrication, injection molding enables high-volume production of plastic parts at a relatively low per-unit cost. This makes it quite efficient for mass manufacturing once setup.
With these inherent advantages afforded by injection molding technology, it’s no wonder the process has become indispensable for so many industries. Next, let’s explore some of the most common applications.
Key Application Areas for Injection Molded Plastic Parts
Injection molding produces vital components across many sectors spanning consumer products, automotive parts, medical devices, and industrial components. Here is an overview of some of the primary application areas:
Consumer Products
Injection molding creates countless everyday plastic products we use regularly, including items like:
- Kitchenware such as food containers, utensils, and appliances
- Toys and sporting goods ranging from simple to complex designs
- Electronics enclosures, frames, and protective cases
- Furnishings like chairs, organizational tools, and decorative elements
Enhanced aesthetics, ergonomics, safety, and cost-savings compared to alternatives like metal or wood make injection molded plastic an obvious choice for diverse consumer goods.
Automotive Parts
The automotive sector utilizes injection molding for both interior and exterior plastic components in vehicles. Typical automotive applications include:
- Body panels, bumpers, spoilers
- Dashboard and console parts
- Cup holders, trays, and storage boxes
- Headlight housings, side mirror covers
- Small clips, connectors, and fasteners
The capacity to integrate specialized functionality into injection molded automotive parts while achieving slim, complex geometries suits the needs of car manufacturing well.
Medical Devices and Equipment
Medical-grade injection molding produces critical diagnostic instruments, consumables, and healthcare products like:
- Test kits, culture dishes, blood collection tubes
- Feeding tubes, masks, IV connectors
- Surgical power tools, handheld dental devices
- Breathing circuits, anesthesia parts
- Prosthetics, orthotics, and mobility aids
The biocompatibility, sterility, high precision, and consistency achievable through plastic injection molding make it vital for medical technologies and ensuring patient safety.
Industrial Machinery Components
Various components for industrial equipment leverage injection molding technology, including:
- Gears, rollers, pulleys, sprockets
- Clamps, valves, nozzles
- Guards, braces, supporting fixtures
- Control knobs, levers, grips
- Filters, screens, customized fittings
Injection molding allows machinery parts to be crafted from high-performance and reinforced plastics able to withstand rugged conditions.
This list provides just a sample of the far-reaching applications for precision injection molded plastic components across major industries. But their usefulness certainly doesn’t end here. Next, let’s highlight the advantages that make them so pervasive.
Benefits of Injection Molded Plastic Parts
Plastic parts produced through injection molding provide a number of helpful benefits:
Cost-Effectiveness
Injection molding is highly cost-effective for mass production after the initial mold creation. Automation makes it cheaper per unit compared to alternatives as volumes increase.
Consistent Quality
Maintaining consistent specifications is easy with injection molding once the molds are finely tuned. The repeatability improves quality control during large production runs.
Complexity Capabilities
Intricate features and challenging geometries are feasible with injection molded plastics that cannot be achieved through other manufacturing techniques.
Material Versatility
With thousands of plastic types and composites to select from, manufacturers can choose the best resins for their specialized requirements.
Design Freedom
The injection molding process places virtually no restrictions on part design complexity or detail. This enables immense freedom compared to more limiting fabrication methods.
Thanks to these meaningful advantages, it’s easy to comprehend why so many industries adopt plastic injection molding for producing essential components.
Now that we’ve covered the major application areas and benefits let’s briefly highlight a few key examples of versatile injection molded parts in action.
Notable Examples of Plastic Injection Molded Parts
To understand the immense diversity that’s possible with injection molding, consider these select examples across vastly different industries:
Legos
These iconic interlocking plastic bricks captivate children worldwide. By injection molding ABS plastic, Lego achieves the snap-fit consistency necessary across billions of bricks for open-ended creativity.
Nylon Cable Ties
Available globally, these ubiquitous fastening ties provide unmatched convenience to bundle or affix items. Their flexibility, strength, and moldability make nylon injection molded ties useful in endless situations from households to heavy industries.
Polypropylene Syringes
This widely used medical implement consists of a polypropylene plastic barrel able to withstand sterilization paired with a precision-molded plunger to administer fluids. Injection molding enables these life-saving tools to be produced at scale cost-effectively.
Acrylic Paintball Masks
Protective eye gear is crucial for this intense sport, and injection molded acrylic masks provide lightweight, rigid, impact-resistant visors along with breathability. Their durability against abrasion makes injection molded plastics well-suited for paintball.
This tiny sample displays the exceptional range possible with injection molding. Next, let’s recap the key points around understanding its most common applications.
In Summary
To sum up, here are the most essential things to remember about the prevalent applications of plastic injection molding:
- Injection molding produces plastic components across consumer goods, automotive parts, medical devices, industrial machinery, and more.
- The process excels at complex, precise, and creative designs with visual appeal thanks to immense flexibility.
- Matching high-performance plastics to specialized material needs is possible with thousands of resin choices available.
- After initial mold fabrication, injection molding achieves tremendous efficiency and low costs at production volumes.
- Tight dimensional precision and repeatability ensure quality consistency during large mass manufacturing runs.
- From imaginative toys to acute medical instruments, injection molded plastics deliver reliable and inventive solutions not easily achieved otherwise.
Understanding injection molding’s capabilities and advantages makes it easy to comprehend its indispensable role creating the myriad plastic components used globally across virtually every industry and sector today.
This versatile manufacturing process will continue seeing expanded applications as technology evolves. But it already delivers proven utility meeting specialized needs from precision gears to decorative furniture at mass scale.
The pervasive usage and inherent flexibility of plastic injection molding for everything from precision medical implements to creative consumer goods will ensure it remains an essential industrial fabrication technique for the foreseeable future as well.