Injection molding has become one of the most popular manufacturing processes for mass producing plastic parts and products. From Legos to car bumpers, many everyday items are created using this efficient and versatile technique.
While injection molding can be used to produce small, intricate products, it has unique value for fabricating large plastic components as well. As the name suggests, large part injection molding refers to using injection molding technology to manufacture sizeable plastic parts.
But what exactly constitutes a “large part”? And what benefits can this process offer over alternatives? Let’s dive in.
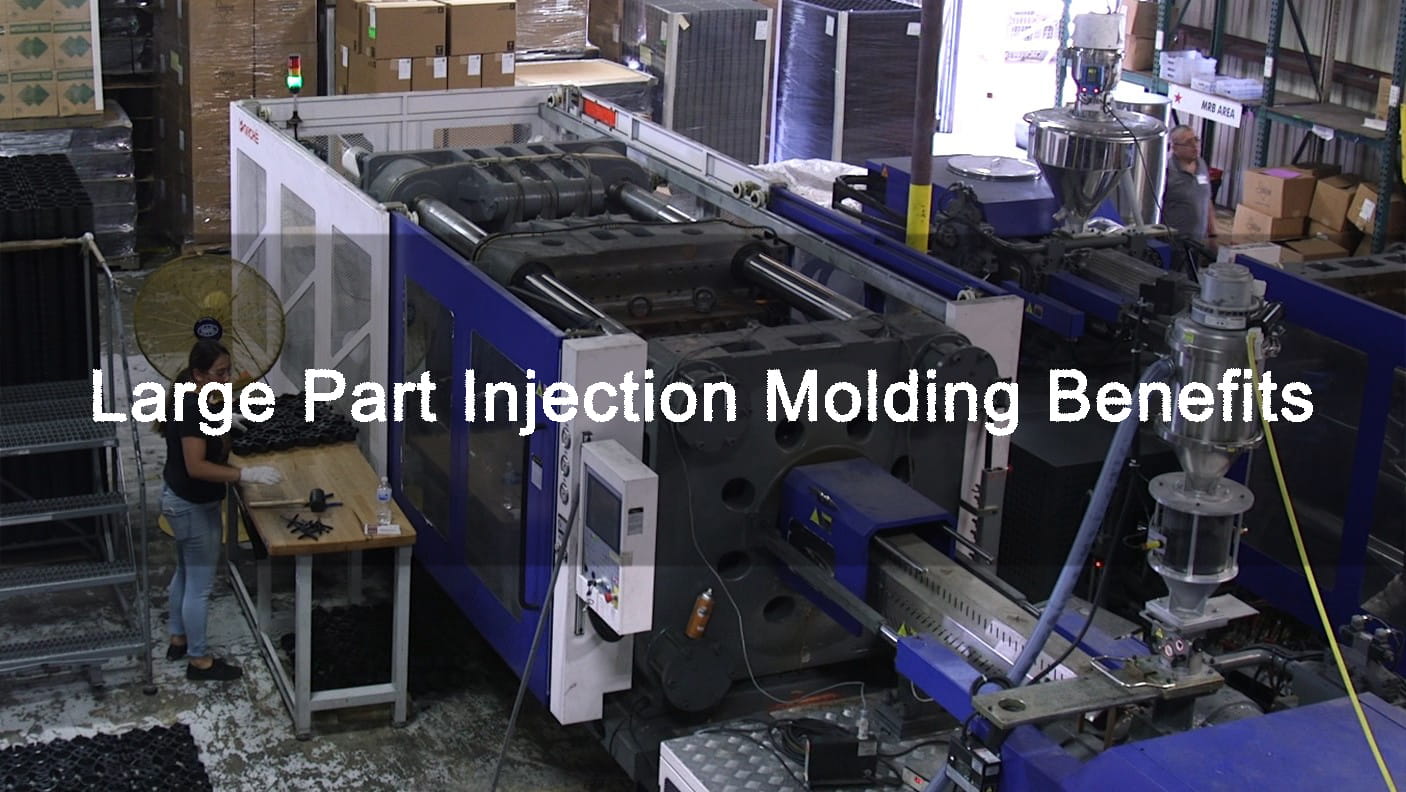
Defining Large Parts in Injection Molding
There isn’t an official consensus for what dimensions categorized a plastic part as “large” in the injection molding process. However, industry experts typically consider anything over 18-30 lbs as a large part.
Some injection molding machines have a clamping force rated in the tons. A higher tonnage indicates the machine has the force required to effectively mold heavier, bulkier parts. Presses rated over 500 tons are often used for large part production.
Additionally, plastic parts over 3 feet in any direction tend to require specialized large part injection molding machines. Producing plus-sized components on standard smaller presses would be inefficient, driving up per unit costs.
With those general sizing guidelines in mind, let’s explore why you may opt to injection mold big plastic components versus smaller items or products made from alternate materials.
The Benefits of Large Part Injection Molding
There are a number of reasons why large part injection molding is an advantageous option worth considering, especially if your product or parts meet the size requirements covered above.
1. Faster Production Times
For starters, large part injection molding delivers much faster cycle times compared to alternatives like metal fabrication or 3D printing.
Where an additive printer may require hours to output one product, large injection molding presses can turn out plastic pieces every few minutes. This accelerated process drastically cuts down total production time for batches.
Reduced manufacturing timelines also translate to parts getting delivered to clients quicker. The high-volume nature makes this form of injection molding ideal for industries like automotive or aerospace that demand vast quantities of products or components regularly.
2. Lower Costs Per Unit
Another benefit closely tied to faster cycle times? Decreased per unit price points. Being able to churn out plastic parts rapidly significantly cuts down on operation overheads associated with equipment usage, facility leasing, labor, etc. Makers pass substantial savings from maximized efficiency rates on to buyers through reduced part costs.
Higher mold cavitation also lowers expenses because it allows more components to be fabricated per cycle. Ultimately, buyers ordering large injection molded components in bulk can realize sizable cost reductions that wouldn’t be possible with traditional fabrication or 3D printing.
3. Excellent Consistency
When working at smaller scales, inconsistencies between units or batches tend to get magnified. But large part injection molding delivers excellent consistency even when generating hundreds or thousands of units.
Thanks to sophisticated computer-controlled processes, modern molding machines can replicate plastic parts precisely from one cycle to the next. This reduces waste from defects and ensures components or products meet original specifications throughout a production run.
Exceptional consistency gives manufacturers assurance parts will function as designed while granting buyers peace of mind regarding dependability. For items like car seats or medical devices, this reliability is non-negotiable.
4. Material & Design Flexibility
In addition to consistency in the fabrication process itself, large part injection molding also provides extensive material and design flexibility. Engineers can select from thousands of plastic types to meet specialized requirements related to durability, weight, corrosion resistance, etc.
The injection molding method likewise accommodates complex geometries and detailed features unfeasible through other processes. Undercuts, varied wall thicknesses, molded-in inserts, and custom textures can be incorporated for superior part performance or aesthetics.
This freedom enables product designers to innovate while ensuring the final plastic components meet desired mechanical properties and quality benchmarks. Items ranging from football helmets to rugged electronic enclosures leverage these versatile design and material possibilities unique to large part injection molding.
5. Lightweighting Capacity
Design flexibility pairs with exceptional lightweighting potential as an advantage for big injection molded plastic components. Manufacturers can frequently replace heavy, dense metal parts with lighter weight injected molded plastics without compromising strength or structural integrity.
Thoughtful design choices and advanced materials like long glass fiber thermoplastics with comparable durability allow for substantial weight reductions. This lightweighting directly benefits industries like automotive and aerospace – even minor weight decreases accumulate fleet-wide to cut massive amounts of fuel.
Replacing conventional metals with slimmed-down yet robust injection molded parts made of plastic or advanced composites boosts environmental sustainability through enhanced efficiency. Less weight hauled also leads to reduced emissions.
6. Post-Molding Machining
One last benefit offered exclusively by plastic parts from large injection molding? Additional post-molding modifications remain possible through machining processes.
While metals have some capacity for after-production enhancements, plastics provide expanded opportunities. Activities like tapping screw holes or precision boring can be executed following initial injection molding relatively easily.
Performing such secondary machining allows for consolidation of more features into single components. Rather than requiring separate fasteners or sub-assemblies, attributes like threaded metal inserts for securing can get incorporated into the monolithic molded parts.
Is Large Part Injection Molding Right For You?
Now that we’ve surveyed some of the core benefits – from faster fabrication times and lower per unit pricing to exceptional consistency – it’s worth considering if large part injection molding aligns with your project.
Below are a few key factors which may indicate if your application calls for outsourced production of big molded plastic components:
- You require 100+ moderate-to-large sized parts weighing over 10 lbs
- Dimensions exceed 18 inches on any given side
- Seeking to replace dense metal elements with plastic equivalents
- Need complex geometries with strict tolerance requirements
- Consistent quality and reliable performance are non-negotiable
If your specifications align with multiple points above, partnering with a specialized large part injection molding company could be the optimal route. Leading plastic product manufacturers possess massive molding presses boasting 2,000+ tons of clamp force paired with experienced engineers capable of bringing your project vision to fruition.
Closing Thoughts on Big Plastic Parts
When designed thoughtfully, large injection molded components fuse accelerated manufacturing velocities, lower costs, and enhanced customization versus conventional fabrication techniques. As the technology and materials continue advancing, expect lighter and stronger plastic parts displacing additional metals traditionally used in automotive, aerospace, and consumer industries.
To determine if your application fits the large part molding profile and which material solutions may work best, consulting a plastic manufacturing specialist is encouraged. With their design for manufacturing (DFM) guidance and in-house engineering expertise, they can help assess if injection molding massive components merits consideration while locating areas for optimization.
Ultimately by merging innovative design, advanced materials, and efficient high-volume molding processes, businesses are better positioned to develop groundbreaking products that push boundaries in their relative markets. In the coming years,increasing numbers of category-defining solutions containing large functional plastic parts fabricated via injection molding will likely emerge. The technology provides the springboard; you simply need to make the leap.
The Bottom Line
To recap, adopting large part injection molding methods enables:
- Faster per unit production cycle times
- Reduced overall manufacturing costs
- Exceptional repeatability and consistency
- Expansive material and geometric design possibilities
- Lightweighting through plastic material replacements
- Post-molding enhancements via machining
Factoring these performance-enhancing and cost-cutting advantages against conventional smaller plastic part fabrication or alternate build techniques proves worthwhile for many buyers and engineers. Review your project demands to decide if outsourcing big molded plastic parts is the most strategic direction.