Injection molding is one of the most common manufacturing processes across industries. It involves injecting molten plastic material into a mold cavity under carefully controlled temperature and pressure conditions. The material then cools and solidifies into the desired shape.
One of the most widely used plastics for injection molding is ABS (acrylonitrile butadiene styrene). Can abs be injection molded? Absolutely! In fact, ABS is ideal for injection molding applications due to its versatility, strength, heat resistance, and cost-effectiveness.
As a professional ABS plastic injection molding manufacturer, I will share everything about ABS in injection molding.
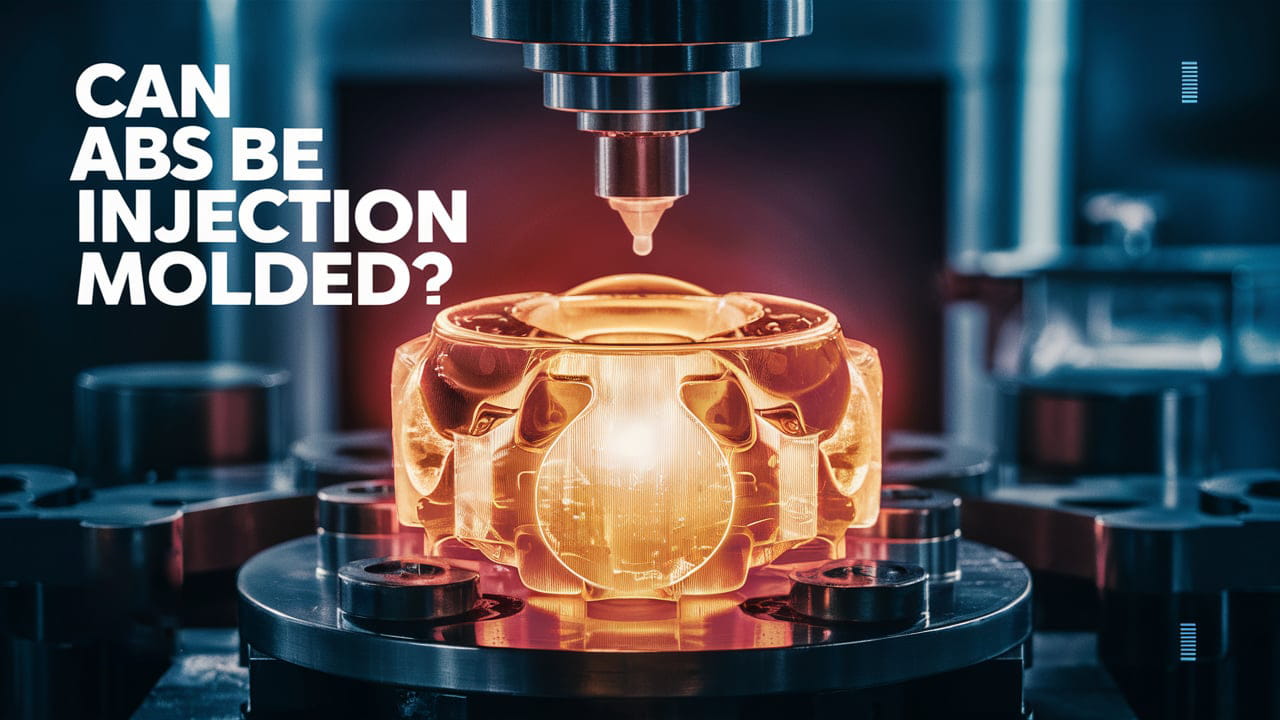
What Is ABS Plastic?
Before diving into injection molding specifics, let’s quickly go over what ABS plastic actually is.
ABS stands for acrylonitrile butadiene styrene. It’s made by combining three different monomers in varying ratios:
- Acrylonitrile provides chemical resistance and thermal stability
- Butadiene offers toughness and impact strength
- Styrene gives ABS its shiny, impervious surface
By tweaking the ratios of these three components, manufacturers can produce ABS grades with different characteristics. This versatility is what makes ABS one of the most widely used plastics today.
Overall, ABS offers exceptional strength and rigidity. Yet, it’s still lightweight and can withstand relatively high temperatures. These material properties lend themselves nicely to the injection molding process.
Benefits of Injection Molding ABS
There are several key reasons why ABS is an ideal candidate for injection molding:
1. Heat Resistance
ABS has high heat deflection temperatures between 80°C and 100°C depending on the grade. This thermal stability allows it to withstand the high temperatures inside the injection molding machine without losing its integrity.
The result is consistent, high-quality ABS parts batch after batch.
2. Strength
With tensile strength ranging from 42 MPa to 45 MPa, ABS is no slouch. It’s tough enough for products that need to handle some abuse.
At the same time, you can add reinforcements like glass fibers or carbon nanotubes to ABS during processing to make it even stronger. The high native strength of ABS means you need lower loadings of reinforcements to hit strength targets.
3. Dimensional Stability
When processing conditions fluctuate, ABS does an admirable job of maintaining its dimensions once it cools. This dimensional stability ensures every single part meets specifications, even for large production runs.
Dimensional stability also enables ABS to hold tight tolerances of ±0.08 mm when manufacturing intricate injection molded components.
4. Chemical Resistance
ABS offers decent resistance to acids, alkalis, salts, oils, and aliphatic hydrocarbons. This chemical resistance suits ABS for pipes, fittings, connectors, and housings that need to shrug off exposure to harsh substances.
5. Range of Finishes
The smooth, impervious surface ABS forms lends itself nicely to decoration. Want a metallic look? No problem — metal plating ABS is commonplace. Custom colors and special effects through painting? Not an issue.
ABS even supports in-mold labeling and texturing for additional scope when designing end-use products.
6. Recyclability
One of the major advantages of thermoplastics like ABS is recyclability. Parts made through ABS injection molding can be reground and made into new products at the end of service life. Recycled ABS grades are a popular choice for non-critical components and cost-sensitive applications.
Is ABS Easy to Injection Mold?
Though ABS does have superb injection molding characteristics, it isn’t always a walk in the park. Let’s look at some of the processing particulars you need to stay on top of:
Viscosity Challenges
Unlike most plastics where viscosity decreases as temperature rises, ABS shows the opposite behavior. As the temperature increases above the plasticization point, viscosity spikes and ABS becomes more difficult to injection mold.
To get around this issue, processing temperatures should be kept below the plasticization point. Doing so ensures the lowest possible viscosity for smooth flowing.
Moisture Control Critical
Like all hygroscopic plastics, residual moisture can wreak havoc when manufacturing ABS components through injection molding. Just 0.2% to 0.4% moisture content is enough to cause surface defects like bubbles, pitting, and a cloudy appearance.
That’s why properly drying ABS to less than 0.05% moisture before injection is mandatory. Part design also plays a role — adding ribs helps vent trapped moisture.
Narrow Processing Window
There’s a relatively narrow temperature range to injection mold ABS between 180°C and 230°C. Venturing much outside this window makes processing more difficult and can cause quality issues.
The situation demands tight control over temperature settings and heating element calibration to stay within this zone. Using higher grade ABS resins helps alleviate matters through intrinsically lower viscosities.
Precise Pressure Needed
To completely fill intricate molds, ABS requires injection pressures ranging from 55 MPa to 150 MPa. Pressure requirements also go up for thinner walled components.
Since ABS is sensitive to pressure fluctuations, modern electric and hybrid injection molding machines with fine pressure control work best. On the other extreme, insufficient pressure leads to short shots and defective parts.
Best Practices for Injection Molding ABS
When armed with the right information and equipment, injection molding ABS isn’t overly difficult. Here are some best practices:
Dry Thoroughly
As mentioned already, drying is non-negotiable. But exact protocols depend on the situation:
- For general purpose ABS, 80°C for 2 to 4 hours works well
- Flame retardant grades need 4+ hours at this temperature
- High humidity environments call for longer times still
Regardless of protocols used, bringing moisture levels down below 0.2% is key. Setting up handling procedures to avoid reabsorption of moisture also helps improve quality.
Mind the Temps
Use barrel and nozzle temperatures between 220°C and 260°C for most grades of ABS. Things like filler loadings and viscosity modifiers alter temperature needs.
What matters more than hitting an exact melt temp is keeping things steady. Fluctuations as small as ±5°C can create processing issues and defects.
Optimize Cooling
Cycle times for injection molding ABS range from 10 seconds to 3 minutes, with thinner parts solidifying quickest. Cooling channels in the mold speed up solidification by pulling heat out of the plastic.
Strategically placing channels to generate turbulent — rather than laminar — flow maximizes heat transfer. Coolant temperature and flow rates also require tweaking to prevent warpage and optimize cycle times.
Applications of Injection Molded ABS Parts
The unique balance of properties ABS possesses, combined with injection molding’s design freedom and repeatability, cater to diverse applications like:
Automotive: grilles, trim, ducts, bumper beams, and interior components like dashboards
Consumer appliances: refrigerator liners, microwave trays, and vacuum cleaner bodies
Electronic devices: computer keyboards, monitor covers, and smartphone cases
Power tools: trigger handles and housings for drills, jigsaws, angle grinders and more
Medical components: inhalers, IV connectors, and tool handles that need to withstand sterilization
Toys: building blocks, action figures, and toy vehicle bodies
Ready to Injection Mold ABS?
This overview looked at why ABS and injection molding go hand in hand, along with processing guidelines and applications. The key takeaway: Yes, ABS can absolutely be injection molded!
Its jack-of-all-trades material attributes allow ABS injection molded components to deliver on expectations across industries. Just partner with a knowledgeable mold maker and injection molder to put this versatile plastic to work for your next project.