Can abs plastic be injection molded? Absolutely! Acrylonitrile butadiene styrene (ABS) is one of the most commonly used plastics for injection molding applications across countless industries.
In this complete guide, as a professional plastic injection molding manufacturer, we’ll cover everything you need to know about ABS plastic injection molding, including its key properties, advantages, process overview, applications, and more. Stick with me!
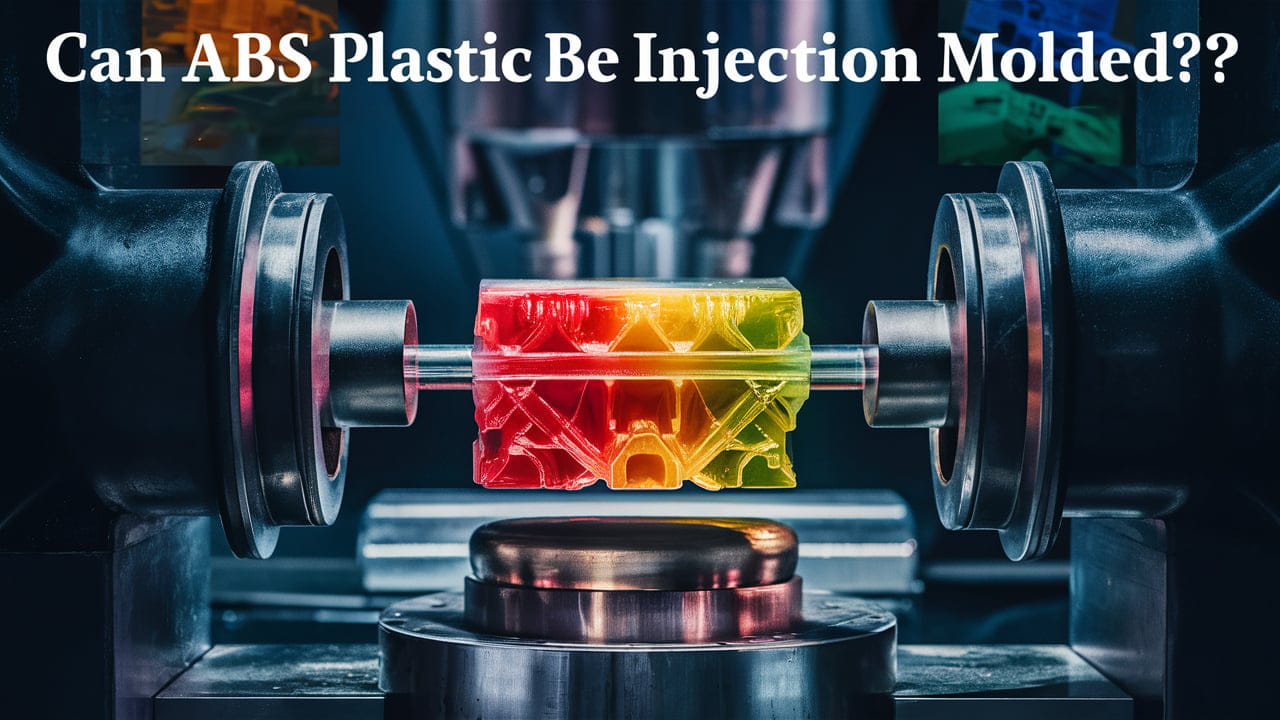
Why Choose ABS for Injection Molding?
ABS plastic combines the strength and rigidity of acrylonitrile and styrene polymers with the toughness and durability of polybutadiene rubber. This versatile plastic has excellent dimensional stability, chemical and heat resistance, mechanical strength, and impact resistance.
On top of that, ABS offers a smooth, glossy aesthetic and takes colorants well. It’s also relatively affordable compared to engineering-grade plastics. These exceptional properties make ABS a prime candidate for injection molding complex plastic parts and products.
ABS can be modified with additives like UV stabilizers for enhanced weatherability or glass fibers for increased strength and stiffness. Specific grades can be customized to suit specialized applications – from flame-retardant electronics enclosures to stainless steel-reinforced medical devices and implants.
So in a nutshell, can abs plastic be injection molded? Yes, and it’s extensively used to manufacture diverse products through injection molding technology!
Overview of ABS Plastic Injection Molding Process
Now that it’s clear ABS plastic can indeed be injection molded, let’s run through the process:
Step 1: ABS plastic pellets or granules are gravity fed from a hopper into a heated barrel with a rotating screw inside.
Step 2: Friction from the rotating screw and heaters raise the temperature to melt the ABS material. Once molten, the screw pushes the material forward through a nozzle into the mold.
Step 3: When enough material fills the closed mold cavity under extreme heat and pressure, the part solidifies. The mold opens and robotic arms with ejector pins remove the finished ABS part.
Step 4: The sprue (excess plastic attached to the parts) gets trimmed off and the plastic parts are inspected and packaged. Reusable ABS runners and sprinkles go back into the injection press hopper.
Maintaining optimal melt temperature, injection speed, pressure, and cooling rate is critical for flawless end-products. Advanced computerized controllers now automate much of this process for consistent high-quality outcomes.
Professional injection mold makers engineer molds suited for ABS plastic, incorporating specialized design elements compatible with its thermal and mechanical properties.
Key Applications of ABS Injection Molded Parts
Owing to its versatile properties and moldability, companies across sectors use ABS injection molding to make tough and resilient plastic components.
Consumer appliances: Mixer casings, vacuum cleaner bodies, fan blades, microwave trays
Automotive: Instrument panels, center consoles, door handles, trim, lenses
Construction: Piping, joints, tiles, roofing
Electronics: Computer and monitor casings, sockets, control panels, keyboards
Toys: Building block systems like LEGO®, action figures
And many more! New applications emerge regularly as manufacturers leverage ABS plastic’s exceptional balance of affordability, aesthetics and functionality through injection molding.
Design Considerations for ABS Injection Molds
To create a dimensionally accurate ABS injection molded component that looks and performs as intended, the mold must be meticulously designed.
Here are some key design guidelines ABS injection mold makers adhere to:
- Optimal wall thickness between 1.5mm to 5mm
- Generous internal corner radii to minimize stress concentration
- Draft angles between 0.5-1° for easy part ejection
- Venting channels to allow trapped air and gases to escape
- Uniform temperature cooling channels to prevent defects
- Robust mechanical strength to withstand repeated injection pressure
And more! With comprehensive DFM analysis guidance from your custom ABS plastic injection molding partner, you’ll ensure your product design is optimized for manufacturability and end-use performance goals right from the start.
Summing It Up: Can ABS Plastic Be Injection Molded?
In short – yes, ABS is ideal for injection molding strong, intricate thermoplastic parts cost-effectively even in high volumes.
With excellent dimensional stability and durability, ABS injection molded components serve reliably across consumer goods, automotive interiors, construction materials and industrial applications.
By partnering with a skilled custom plastic injection molding company, you can manufacture complex ABS plastic parts molded to precise geometries and dimensions every time.
So if your product needs call for resilient thermoplastic components, ABS is absolutely injection moldable into robust, functional parts for your application!