PPE, or Polyphenylene Ether (also known as Polyphenylene Oxide, PPO for short), is widely used in injection molding across industries, from automotive and aerospace to medical devices. As a high-performance thermoplastic, PPE offers exceptional mechanical properties, heat resistance, and chemical resistance, making it an ideal material for injection molding intricate and durable components.
But can PPE be injection molded? What are the specifics of utilizing this versatile material in injection molding operations? In this comprehensive guide, as a professional ppe injection molding manufacturer, we’ll explore PPE injection molding in-depth, covering critical factors ranging from optimal processing parameters to innovative mold technologies and advanced applications. Let’s get started!
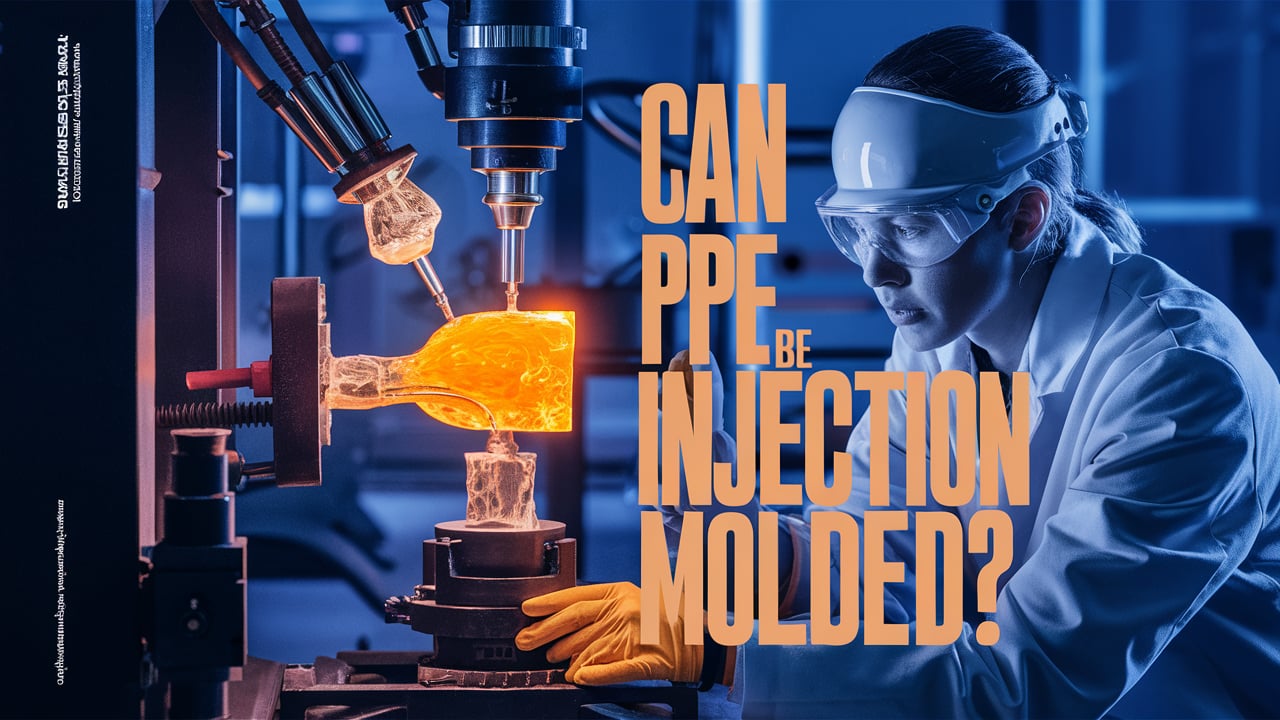
Can PPE be injection molded?
Yes, PPE can be readily injection molded to manufacture a diverse range of products due to its excellent flow and thermomechanical properties. PPE has emerged as a widely used injection molding material across industries such as electronics, automotive, and healthcare.
Key benefits of injection molding PPE
Here are some of the major advantages of injection molding PPE:
- Dimensional stability: PPE maintains exceptional dimensional stability as well as mechanical properties despite fluctuations in temperature and humidity levels. This makes it suitable for precision components.
- Heat resistance: With a high heat deflection temperature and glass transition temperature exceeding 210°C, PPE retains its stiffness, strength, and creep resistance at elevated temperatures, enabling use in high-heat applications.
- Chemical resistance: PPE offers broad chemical resistance, withstanding oils, acids, bases, alcohols, and hydrocarbons. This resistance to chemicals is better than commonly used engineering thermoplastics like ABS, nylon, and acetal.
- Surface finish: Molded PPE parts can achieve glossy, aesthetic finishes that match stringent optical requirements without secondary finishing. This helps reduce post-processing needs.
Given these significant benefits, PPE has become ubiquitous in injection molding lightweight, durable, and high-performance parts across industries.
Optimizing PPE injection molding parameters
To reap maximum benefits from PPE injection molding, manufacturers must precisely optimize key parameters:
Temperature
- Nozzle temperature: 240-300°C
- Feed zone temperature: 60-105°C for amorphous PPE grades and up to 230°C for semi-crystalline grades
- Mold temperature: 60-105°C for glossy finishes
Pressure
- Injection Pressure: 60-150 MPa
- Holding pressure: 30-100 MPa
Drying
As PPE resin is hygroscopic, drying it before injection molding is critical. Typical drying involves heating PPE pellets at 110-140°C for 2 to 4 hours. Insufficient drying can undermine the material’s properties and cause splay, dielectric failure, and fusible deposits on molds.
Precisely tuning these injection molding settings is key to manufacturing consistent, high-quality PPE parts while minimizing scrap and defects.
Cutting-edge PPE injection molds
Specialized injection molds are pivotal for unlocking PPE’s full potential. Advanced mold technologies provide enhanced precision, cycle time efficiency, and complexity.
Multi-cavity molds
These molds contain multiple cavities for producing several identical parts per cycle, accelerating production. A 16-cavity mold, for instance, can increase output 16 fold compared to a standard single-cavity mold.
Hot runner molds
In hot runner molds, heated melt delivery channels allow the material to stay molten as it flows into the cavities. This technology provides exceptional thermal consistency and minimizes sprues, limiting material waste.
Conformal cooling molds
Conformal cooling uses cooling channels that tightly follow the contour of cavities for targeted, even cooling. This novel approach slashes cycle times significantly.
Rapid tooling
Emergent rapid tooling methods like metal 3D printing facilitate fast turnaround of complex PPE injection molds, reducing lead times and costs.
By harnessing such cutting-edge mold technologies, manufacturers can maximize productivity, part quality, and cost-savings in PPE injection molding production.
Groundbreaking PPE injection molding applications
The exceptional performance that PPE offers has paved the way for trailblazing injection molded applications across sectors:
Automotive: Airbag housings
PPE’s heat resistance allows it to withstand the explosive temperatures inside airbag housings upon rapid inflation in the event of a crash.
Aerospace: Aircraft vents
With its strength and dimensional stability across fluctuating temperatures, PPE is widely used in injection molding sturdy, lightweight aircraft ventilation components.
Medical: MRI compatible devices
PPE parts can operate safely in high magnetic field environments like MRI machines without distorting images, unlike metals, making PPE invaluable for molded MRI-compatible devices.
5G infrastructure: Microwave components
The excellent dielectric properties of PPE facilitate molding durable, precision parts for 5G microwave systems to enable ultra-high-speed data networks.
Underpinned by advances in injection molding technology and PPE material science, manufacturers can create novel solutions that reshape industries through high-performance, reliable PPE components.
Conclusion
As a versatile high-performance thermoplastic, PPE empowers manufacturers to injection mold extremely durable and dimensionally stable parts capable of surviving demanding mechanical, thermal, and chemical conditions.
Optimizing injection molding parameters like temperature and pressure settings, coupled with leading-edge multi-cavity and conformal cooling molds, unlocks PPE’s immense potential for pioneering applications, from automotive airbag housings to 5G microwave devices. By harnessing PPE injection molding, manufacturers can keep pushing the boundaries of innovation across sectors.
So in short, yes PPE can be readily injection molded with significant benefits, spurring its expansive use as a 21st-century wonder plastic powering the products and infrastructure of the future.