PVC, or polyvinyl chloride, is one of the most versatile and widely used plastics in manufacturing. With excellent durability, flexibility, and chemical resistance, PVC has become an incredibly popular material choice for injection molding applications across industries.
But before diving into your next PVC injection molding project, it’s smart to understand exactly what PVC is, how injection molding works with this material, key design considerations, and overall feasability. In this comprehensive guide, as a professional plastic injection molding manufacturer, we’ll cover all that and more.
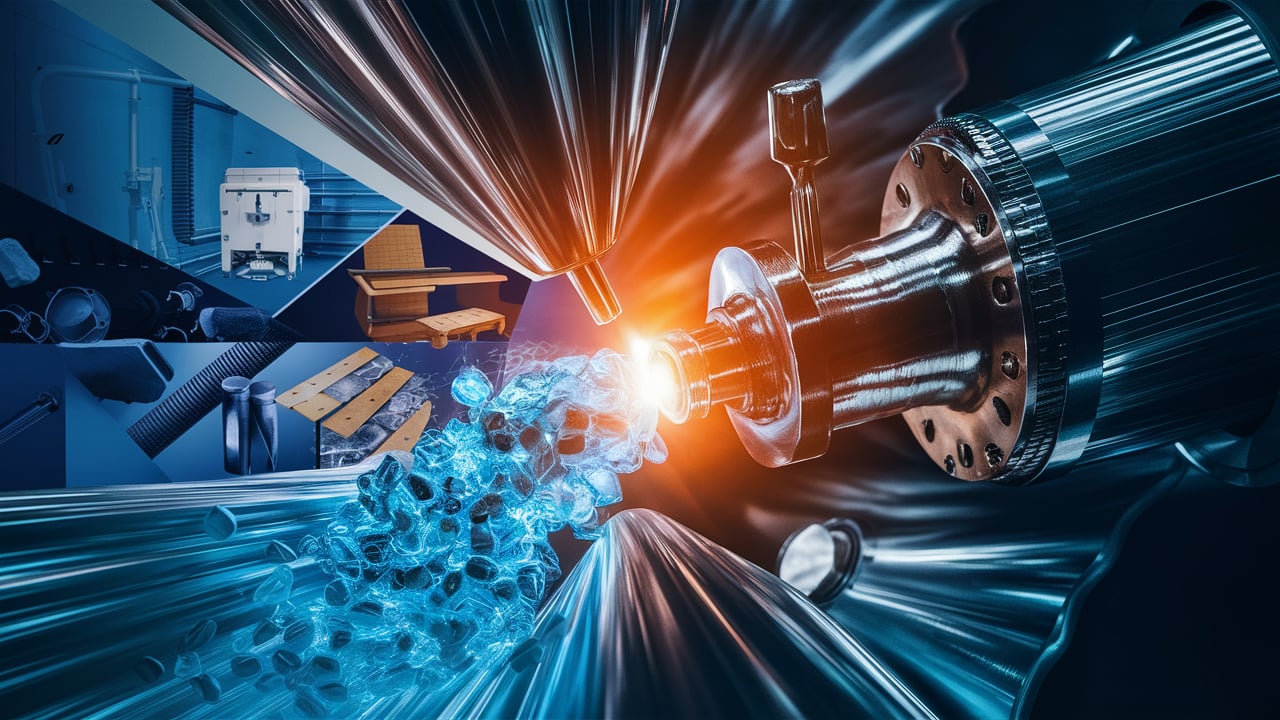
What is PVC?
PVC stands for polyvinyl chloride, which is a thermoplastic polymer made from vinyl chloride monomers. It was first created commercially in the 1920s by BF Goodrich Company.
PVC comes in two main forms – rigid and flexible. Rigid PVC is naturally hard and strong, while flexible PVC has plasticizers added to make it more bendable and soft.
Common uses of rigid PVC include:
- Pipes
- Windows
- Door frames
- Bottle caps
Flexible PVC is often used for:
- Wires and cables
- Artificial leather
- Inflatable products
- Flooring
In injection molding, both rigid and flexible PVC are used to create all kinds of products. The type selected depends on the specific needs and intended application of the final part.
Now let’s look specifically at whether or not PVC can be injection molded.
Can PVC Be Injection Molded?
The short answer is yes – PVC is commonly injection molded for a variety of applications.
A few key properties make PVC well-suited for injection molding:
- Thermoplastic: Unlike thermoset plastics, PVC can be repeatedly melted and solidified without material degradation. This allows it to be injection molded.
- Viscosity: PVC has suitable viscosity while in molten state to properly flow into injection molds.
- Shrinkage: PVC has low shrink rates, minimizing part defects like warping.
- Strength: Injection molded PVC parts can have high tensile and impact strengths for durability.
- Versatility: It comes in grades with different levels of flexibility, tailored to product needs.
With proper mold design and processing parameters, injection molding allows PVC to be shaped into diverse, high-performing plastic parts.
Common examples of injection molded PVC products include pipes, fittings, machine housings, furniture, and consumer electronics.
So in summary – yes, PVC is absolutely injection moldable. Next let’s look at some design considerations when working with this material.
Design Considerations for Injection Molded PVC Parts
When designing parts made from injection molded PVC, you need to account for the material’s unique properties and how they will affect manufacturability.
Here are some of the most important design guidelines:
Uniform Wall Thickness: Strive to maintain an equal wall thickness throughout the part to prevent defects from uneven cooling rates. Gradual transitions in thickness are best.
Draft Angles: Include a slight draft angle, usually 0.5-1°, on any vertical walls to support easy ejection from the mold.
Corner Radii: Sharp corners lead to stress concentration. Use corner radii of at least 25% of the wall thickness.
Ribs and Gussets: Adding structural ribbing inside the part removes mass while retaining strength. Useful for minimizing sink marks too.
Textures and Patterns: Molded textures help hide weld/knit lines. But keep textures shallow with draft angles.
Accounting for these factors in the design stage is crucial for producing functional, durable PVC parts via injection molding.
Is Injection Molding the Right Process?
With an understanding of PVC properties and part design essentials, a key remaining question is if injection molding is truly the ideal process for a given application?
Here are a few factors to help with this assessment:
Part Geometries: Injection molding excels at producing complex, 3D geometries not easily possible with other methods. Is this complexity needed?
Production Volumes: The high upfront costs of injection molds make it best suited for mid to high production volumes. Lower volumes may be better fit for other processes that use lower-cost tooling.
Cost Targets: While injection molding benefits from economies of scale, process/material selection shoul align with budget. Thermoplastics like PVC are more affordable than advanced polymers.
Performance Requirements: Properties like strength, UV/chemical resistance, appearance, etc. should match target application. Injection molding can accommodate broad material selections to meet specifications.
Prototyping Needs: Adjustments to a plastic part are easier and cheaper early on. Will the ability to quickly iterate prototypes before committing to injection mold tooling be beneficial?
Considering factors like these helps determine if injection molding PVC is the right match for manufacturing goals, or if an alternative process better fits requirements.
Conclusion
PVC’s versatility, durability, and processability make injection molding an ideal production method for countless applications. With a suitable mold design tailored to PVC’s properties, diverse and cost-effective plastic parts can be manufactured.
So in summary:
- PVC can be injection molded
- It’s properties allow molding of high performance, complex parts
- Careful design considerations are needed
- Assessment of all manufacturing requirements should occur before process selection
If after reviewing the feasibility it’s determined injection molding meets project needs – PVC is likely an excellent material choice worth pursuing. Reach out to discuss how our injection molding expertise can make your next endeavor with this versatile plastic a success!